Simplex
A military type outboard cruiser
(reprinted from "Sports Afield" - 1954)
click image above for larger view
UP IN THE lake states where outboard motors are made—Wisconsin,
Minnesota, Michigan—you'll find a
bewildering maze of waterways ideally located tor intriguing cruising.
On these waters it either blows like
sixty and everyone stays ashore, or it
doesn't blow at all and everyone and
his brother goes afloat. For such
water and service was Simplex designed.
She is boxy and big for her inches.
She is as simple as possible to build,
giving consideration to strength and
the whopping loads that craft of this
type are asked to carry.
Simplex is not the last grunt in
speed, nor exactly the kind of boat
for open water. On these points I'd
prefer Sun Dance, the forerunner of
Simplex, which appeared in last
year's Boatbuilding Annual, a few
copies of which are still available.
But when it comes to breezing off
the girl friend, or taking out a pack of kids in calmer water, Simplex will
provide the passenger-carrying bulk
you need. She is contemporary in
looks, and should please the Neo-Whistler or Hot-Diggety school of
boating advocates, for I have borrowed something from my PT boat
designing experience and have given
her something of that military persuasion. She is a good all around
boat; simple and cheap to build.
Simplex is one of the few designs
that can handle twin engines if need
be. She will handle two 15 or two
25 hp outboards with ease, although
she'll be quite lively with one of
either.
One reader of last year's Boatbuilding Annual built a Sun Dance
for $198.50. Simplex will cost only
a few bucks more, this extra cost being chiefly in the Plexiglas for the
cabin lights.
You'll need ample space in which
to build her, as the 14-foot forward
topside plywood panels are "wung
out" very wide when fastening to
the stem, bending through approximately 45° of arc.
The deck arrangement plan of Simplex is shown in the upper half of the drawing. Note that if
more cockpit space is wanted than the plan shows, an optional coaming line is given. Lower half
shows layout of the extremely simple arrangement plan. How does this suit your requirements?
(click images for larger views) |
|
This will take space, and more
than one pair of hands. This bend
is wide and reasonably easy, but will
take some doing. But it is being done every day, and the lines of Simplex
have been generated on the developed surface principle from transom to frame No. 1 to make bending
easy.
Forward of that point, her lines
depart from purist theory, and a
faint tuck is taken in her topsides
to give the FT boat stem profile, now
being ardently copied by some hull
draftsmen.
Building outdoors is feasible if
you use a six dollar Koroseal car
garage covering, particularly in the
dry season. Rain spoils nice surfaces
and joints. Rain also knocks mating
surfaces cockeyed, making it hard
to get a tight hull. But aside from
these few pointers, there is nothing
unusual about Simplex--except her
simplicity.
Her arrangement plan has been
purposely left wide open. You can
do what you wish about running
seats, stove, lockers, and whatever
suits you. Any man who can plane
a smooth surface and who has an
eye for a fair curve can easily build
her. But wood choppers had betterleave this — and any other boat —
alone.
The beginning step in construction is to lay down her lines full
size. This means outboard profile,
half breadths, and body plan. All
must fair up and tie in on your loft
floor before you cut a single stick of
wood, or you will get into measurement trouble.
The profile must be in fair lines
as reasonably close to the heights
above baseline as is feasible with
your batten. The half breadths also
must be fair, and the body plan
drawn off these two views must check
for beamwise and heightwise intersection before you cut a single stick
of wood.
A boatbuilder doesn't need to be
told this—he understands why. But
some amateurs think they can lay
down a body plan only, from offsets,
and commence construction.
If a big enough painted floor is
not available, you can tape pink
building paper to the floor in a
couple of lengths with sufficient overlap to give you a good laying-down
surface. Snap the baseline and the
waterlines in with a chalkline; there
is nothing more accurate.
Take a straightedge and pencil in
this set of lines. Carefully erect the
perpendiculars on the baseline for
heights, and off the centerline for
half breadths. Make sure of neat station spacing as dimensioned. You
will need two battens to loft this
boat. One should be 1"x1" of some
knotless wood (sugar pine is ideal: mahogany good) and should be tapered for about 6" down to 1/4" at
the end. This is for lofting in the
sweep of the sheer line in plan view.
An untapered batten will tend to
give a "fiat" just abaft the stemhead.
To avoid this, the sheer line has
been drawn extended. This whole
line should be swept in, working
well back on the batten.
A small batten of oak, about 3/16"
on the flat and 3/4" wide will do to
fair in the stem profile, being
streamed between nails set on either
side.
All the offsets shown have been
scaled from the original drawing
from which the illustration is
printed. These have again been
checked with the scale model which
was made to check flotation and hydrodynamics. They are believed to
be accurate. But errors sometimes
occur. Once in a while the right dimension gets into the wrong column,
and so on.
The idea of laying down is to
fair all lines closely to the offset
table. Don't get into a panic if an
offset is wrong. Ignore it. Then
average the dimension in from the
sweep of batten from other points.
Simplex will float all right and run entirely all right if you'll do this.
On the body plan, you will note
that most of the frame sections are
straight. This is part of the Simplex
idea. Plywood, however, when bent
and warped will belly somewhat.
The idea is to let it. I have indicated
this probable bellying at points
where the model indicates it occurs.
And here we have a gimmick.
Frame these sections perfectly
straight when you loft them, and
build the frames straight section.
Where a belly is indicated in the
bottom lines, you can, when initially
bending the plywood over the boat's
frame for size, determine the amount
of natural plywood belly. Add curved
shim frames to pad out the curved
contour. Screw and glue these shim
frames to the main frames, and your
problem of lofting a curved or developed surface is solved.
The reverse process is employed,
on frame No. 1 where that tuck in
the topside bow panel will call for
a dished-in frame. You may trim out
the required hollow with a spokeshave from the solid according to
requirements of the bent panel. But
it would be much easier, it seems to
me, to build the topside frame on
No. 1 about an inch shy of full, bend
the panel to the sheer harpin and
chine, and, after it is secure, and
the hull turned over, add shim pads.
Their size and bevel can now be, easily determined by scribing.
Extend all frames to the floor line
indicated on the body plan. The end
of the frame that hits the floor is
called the "heel." Tie the heels together with 1"x4" cross spalls of
rough lumber, carefully marking the
centerline on the cross spall.
Because the body plan is drawn
to the outside of the planking, the
frames must be built 3/8" inside the
sectional line to allow for planking
thickness.
All planking of Simplex is of 3/8"
DFPA-Ext. grade, which means marine plywood, and good two sides.
Nothing else will hold together.
If you are fortunate enough to
live in an up and coming locality
where complete stocks of plywood
are kept, you can get marine plywood in the required lengths. You
will need two pieces 3/8"x4'x14' and
one piece 3/8"x4'x12' for the topsides;
This latter piece will be cut in half,
so two pieces 3/8"x4'x6' will do, and
may cost you less.
This exploded perspective shows the placement of hull members in
relation to each other. Note that knees are lag-screwed to the
motor apron of 3/4" 5 ply, and then they go to the sole stringers. |
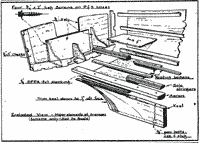
|
|
For the bottom you will need two
pieces 3/8"x4'x14' and one piece 3/8"x4'x10'. This latter piece is also cut
in two. Maybe your dealer has two
five-foot lengths-they'll do. All of
this is marine plywood, remember.
If you go to twin engines and the
boat is to take a beating, and you
want an especially long-lived job,
buy five-ply for the forward bottom,
3/8" thick. This is airplane grade,
birch-faced, and expensive. But if
you've got money enough for two
motors, you should worry.
An alternative would be to coat
the bottom with glass cloth if severe
service is intended, using ordinary
DFPA-Ext. 3/8", 3-ply.
The gussets for the frames arc of
3/8" 3-ply, glued and screwed both
sides of the frame with No. 6 3/4"
flathead brass screws. If you can't afford brass, you might go to cadmium
plated screws. But my experience
with such screws has been that they
rust out in a few years. Brass, especially Everdur screws, are long
lived.
A good source of screws, if you
must order by mail, is the Southern
Screw Company, Statesville, N. C.
All gussets are glued with casein
waterproof glue, made in small
batches and used fresh. Where indicated, the gussets are left open.
Otherwise they are filled with lumber molded same as the frame.
The setup of the frame is the
same as lor any of the plywood boats discussed elsewhere in this Boatbuilding Annual. There is no need
to rehash the obvious about that
subject here. Just make a grid on
the shop floor, erect the frames to
the floor line, fasten up the keel and the stem to the frames, properly
plumbing and horning them, and you can then install the chines, and
the sheer harpin and clamps and
get on with the planking.
A word on the harpin might be
well, as you don't often see this typically heavy boat feature on so light
a craft. I use it here because whenever a big boat shop has a yacht
with bent and sawed frames which
have a lot of flam to them, a harpin
is always put on the molds to secure
the frame ends to.
Most harpins are female, cupped
to fit the flam. Here we reverse the
procedure, and this flat shelf, or harpin, is band-sawed after being edge-scarfed. The drawings tell the tale.
I'd use mahogany for this member,
or yellow pine (if you are careful
about driving fastenings) but not
oak, which would call for expert
woodworking. Note that the harpin
ends after its purpose of holding the
shape of sheer sweep is over, and an
ordinary sheer clamp is jointed and
bolted to it, finishing out the sheer
edge to the transom.
The drawings clearly tell the story
of the subsequent construction, and
you will see perspectives which are done to save a whole lot of words.
The cockpit sides are shown parallel, but an option is shown dimensioned if you want the extra room.
The parallel cockpit sides will go in
like greased lightning, and the resulting cockpit space will be 5'x8',
which is larger than the standard
small bathroom. The side decks then
give nice cover room for multiple
cabinets and drawers - something no
boat can have too many of. In this
parallel coaminged job, only the
ends need bending. Boil them in a
washtub for 15 minutes, bend them
over a form, and horse them home
with bolts through the harpin. Handy thing, that harpin!
I'd use 5/8" mahogany for the coamings. It will be cheaper to cut the
window-lights out with a band saw
from the solid wood than to burn up
time making a mullioned and stiled
frame. A way of inserting the 1/8"
Plexiglas lights is shown.
You can take the panels to a sash
and door factory and have them rout
out the recess rabbet, or you can
back the entire port area with the
Plexiglas, and try your luck at cementing it to the frame, using a
fillet of something like Sealer 900 or
Kuhl's elastic seam compo to keep it
tight. I have not shown swing windows forward, in keeping with the
Simplex idea., but they will without
a doubt be wanted later.
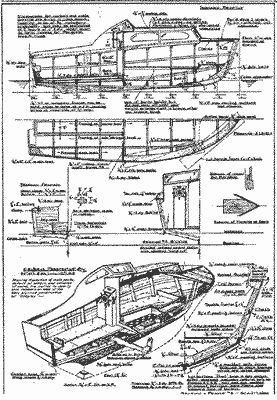
click image above for larger view
Wes Farmer

Other designs by Wes Farmer:
|