To Part Two
There are a number of sites on the internet and articles devoted
to the one sheet boat. This is a good thing as it gives simple
plans for simple people, of which I am one. One of the best I
have come across is the web site by Hannu
Vartiala. He goes into a lot of detail in the planning
and building of a number of boats and covers the topic of one
sheet boats almost exhaustively. Others have made more of handling
properties rather than maximal volume, or maximal use of plywood.
In addition to the duckworks site, here are some more interesting
sites where there might be a one sheet design or two.
https://www.simplicityboats.com/OSchallengeresults.html
https://www.angelfire.com/ego/lewisboatworks/html/main_a.htm
https://home.clara.net/gmatkin/freedes.htm
Having read how well the topic has been covered I saw just a
couple of niches. One of these niches is the half sheet boat which
I will cover here. You may prefer to think of this as the one
sheet two boats. The other niche is the one sheet folding pirate
ship, which I will probably cover later. Here is my tale of experimentation
and joy.
Part 1 The Warnie
Firstly, I decided one sheet boats were just not radical enough
and that a half sheet boat could possibly potentially be a semi
practical alternative for the first time builder/designer. Secondly
I noticed that Hannu's "maximal volume" half sheet boat
was a hexagonal section and that an octagon gave a 4% improvement
in volume over the hexagon so here is a plan for an octagon section
boat from a half sheet of ply (8 foot by 2 foot), and my prototype.
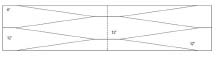 |
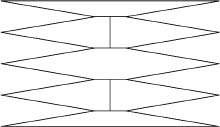 |
 |
Having test floated this boat I found it to be a vicious turner
in all directions, including fore and aft. I believe that the
correct navy parlance is that she rolls like a stuck pig and pitches
like a drunken mule. As a consequence I named her the Warnie to
warn people not to make her. Interestingly, Warnie is also the
nickname of Australian cricketing spin bowling legend Shane
Warne. [Editors note: This cricket
video shows his skill https://www.youtube.com/watch?v=LeLn8sEAKfE].
Boat names are so much better when there is more than one level
to them. The main problem that arose in early test floating is
that the boat is almost impossible to either get into or out of
without getting wet. Once inside the boat it is actually not too
bad.
This is not the maximum volume I could have made doing this but
I was trying to add some length for stability (which in retrospect
I think was a mistake as all I did was make the ends thin which
may have decreased stability). It has a very respectable flood
volume of around 190 kgs
(425 lbs) which is better than some one sheet boat patterns I
have seen on the internet. This slight variation on that pattern
would have a flood volume of around 210 kgs (466 lbs).
The joins were made with fiberglass drywall tape and Bostik
Seal N Flex FC, which I saw being used to glue together concrete
water tanks together and has the additional benefit of passing
he Australian Standard for use as an expansion joint sealant in
aircraft runways. Makes me want to go out and start on that aircraft
carrier I always wanted.
Part two: The Ollie Punt
The best thing about a half sheet boat is that it leaves you
a second half after making your first attempt. Tortured and disconsolate
over my lack of fore and aft stability in the Warnie and looking
at the ridiculous amount of freeboard on the Hattory,
I decided to go with a squashed Hattory, or if you prefer, the
middle bit out of a Dug.
 |
The dotted lines show strait guide lines while the
dotted gentle curves provide the lines to actually cut which give
gentle curves throughout the length of the boat. Focusing in on
how I made the gentle curves in my final boat, all I did was rule
a line level with the outside 12 inches in from either of my ends
and then joined the two ends of the 12 inch lines to form an angle
and then from a point six inches in from either end I took a 12
inch (30cm) ruler and from my six inch point I moved it till it
touched the long angle, thus smoothing out the angle. By using
a panel saw to cut the lines I then smoothed out what little sharp
angles were remaining in the cutting.
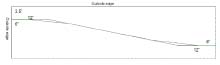 |
A small note here is that you can easily make the join in the
floor rather than in the sides of your Ollie Punt if that is your
wish. We are actually cutting the plan out of a giant ring, only
they don't usually sell plywood in giant rings so you have to
pretend the ends are already joined and swap end measurements
for middle measurements and vice versa. Similarly you could make
yours asymmetric by shifting the middle measurements towards either
end.
Stitching together was extremely easy as the boat folds together
reasonably well (with a few adjustments to the plan a potential
folding boat no less), so I was able to lay the boat together
flat, sand off rough edges, drill, loosely cable tie the lot together
and then just fold it out, brace it roughly where I wanted the
side angles and tighten the cable ties. Note the twigs helping
to keep the panels aligned (others have used dowels) and the highly
scientific way in which a stick has been used to temporarily set
the angle of the sides.
|
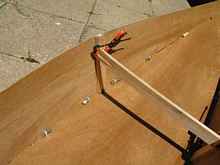 |
The end panels were cut from an old plank I had lying around.
It was 4 inches wide so I was able to add a little inward slope
to the ends. Note the usefulness of cable ties demonstrated yet
again. The end pieces are 6 inches across the bottom and 8 inches
across the top and a bit of an angle was planed into the bottom
and top edges to minimize the amount of filling required. All
wood gluing was done using Vise Supergrip, a foamy polyurethane
glue similar to gorilla glue. The angle of the sides in the middle
was adjusted so the top of the boat was relatively level (very
little rocker). I finished up with a top middle measurement of
21 and a half inches (550 mm) The sides were then glued to the
floor using fibreglass drywall tape and Bostik Gold. First I did
tack joins with a bit of the glue and a short bit of drywall tape
in the spaces between the cable ties. After waiting for the glue
to set, I removed the cable ties cut some more tape in half lengthways
- two layers of this half width tape and one of full width inside
and out. I started by spreading the glue with a Popsicle stick
and switched to a proper putty knife about halfway through when
it broke the putty knife was much easier. I used two 380gm cartridges
of glue.
 |
Because I made this boat from 3mm Luan door skin it required
more than a little reinforcement.
The gunwales were made by cutting down some half inch (12mm)
lining board. Pre-bending by wrapping in a wet towel under a few
bricks overnight worked so well, I actually over bent them slightly.
If you have good eyes and check out the photos below, you may
be able to tell my gunwales are 2400 mm long and the side it is
joined to is 8 feet (2438mm) long. That is what I get for living
in a country where houses are built in imperial and renovated
in metric.
Having fixed on the gunwales I found the ¾ inch (19mm)
thick keel piece a little trickier as I had accentuated my curving
in the floor by leaving the ends of the sides straight, which
pulled the floor up towards the ends. Half inch timber for that
too would have been easier. Putting the keel piece on first might
also have been easier. Basically I just sprayed water all over
the whole rig and then threw some wet towels and sponges so the
wood I was trying to bend would stay damp for a while.
After a day or so I took off the wet stuff and left it to dry
in the sun, (temperature was in the 90's Fahrenheit/ 30's Celsius
with about 2% relative humidity so no problem with drying where
I live). Here is how it finished up. This is the shape the gunwales
probably should have been too.
I used about 8 short bits of half inch wood across the floor
(which was the straight direction) to screw through into the keel
piece, because a screw would just have pulled through the 3mm
plywood without reinforcement. Some extra screws with washers
were required during gluing to clamp the floor to the keel piece
more evenly. These were removed later and the holes filled with
a drop of foamy polyurethane glue and bamboo BBQ skewers.
This has proved to be a great success, while the volume to flood
calculations come in at a paltry 110 Kgs (260lbs), this is perfectly
suited for people who weigh less than 60 kgs (140lbs) or so, of
which my 10 year old son is a perfect example. With my 100Kgs
(220 lb)on board it has 5mm (¼ inch) of freeboard, which
I have managed to get to last for about 45 seconds. With my son
on board (44 kgs/98lb), there was some unexplained instability.
I have yet to determine a mathematical formula but the time taken
for the boat to flip over appears to be in an inverse relationship
with the ambient air temperature, which seems to affect the hydrophilic
balance between my son and the water.
To Be Continued...
*****
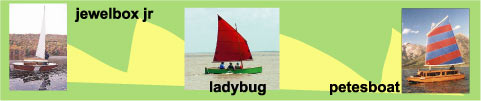
|