In the summer of 2006, I built a 10
foot, skin-on-frame boat of my own design. I subsequently checked
this boat onto a plane and took it with me on vacation. I named
this boat Snakedoctor, the West Tennessee colloquial name for
the dragonfly. This is the story of the boat in a bag.
As a young man in West Tennessee, in the 1960's, I spent a great
deal of time fishing. Most of this fishing was done on Kentucky
Lake, and a lot of it was done from homemade wooden boats. I first
fished with my father, Ralph Holt, and his friend, Jack Denney,
in a boat built in Mr. Denney's back yard. The first sign of spring
may be the Robin, but the first function of spring was painting
the boat. In later years, I would spend many days in a 10 foot
skiff owned by Hugh Allen Carter.
This began a life-long interest in boats. Other pursuits held
most of my attention until, in 1985, I met my good friend Mark
Brown. Mark was the first person I had met, since my childhood,
who had made his own boat. It was a beautiful 12 foot cedar strip
canoe of his own design, which he called Wood Duck. The restoration
and improvement of this boat, in 1987, led to my first hands on
experience with boat building. About two years later, Mark, Lyle
Mason, and I built a plywood boat at Lyle's house, and I was hooked.
Since then, the study of boat design and construction has been
my principle hobby. The pursuit of this hobby next led me to build
several plywood boats.
Based on a series of discussions I had with Mark Brown, I began,
in 1998, to work on a design for a light, easily built, inexpensive
boat. While I had researched many designs, they tended to be either
too complicated or too time-consuming to suit my needs. Magazine
articles of this time seemed to all feature boats that I thought
were daunting for the inexperienced builder. They also tended
to be expensive to build. There were many great boats featured
in these articles. I wanted to design a good boat for builders
with minimal experience or limited time or resources. It seemed
to me that a boat that could be quickly built would prompt more
builders to actually start projects. This type of boat would also
tie up the space needed for building for a much shorter time,
making for a more convenient building process.
I had several phone conversations at that time with Platt Monfort,
who told me that a less complicated design could be "bought"
at the price of some added weight. These discussions caused me
to look at older designs, and I settled on a modernized form of
flat-bottomed kayak. Experimenting with models produced a simplified
construction technique, which did not require building a strongback.
This drastically reduced building time, and made it possible to
move the boat quite easily during the construction.
Working on the fly, I drew a 12 foot solo canoe. Frames were
ship-lapped spruce, glued and screwed, which I then sawed to shape
with a jigsaw. Stems were assembled and sawn in the same manner.
The frames were then screwed and glued to a full-length central
floorboard. A full-length keelson was next added. This method
does not require a strongback, as the backbone of the boat keeps
it in shape. Douglas fir stringers or longitudinals were added
along with floorboards and thwarts for strength, and all that
was left was the fitting of a skin. The framework construction
had taken ten hours over the course of two days. I had never read
of a boat made in quite this way. After much research, I settled
on a skin of white vinyl upholstery fabric, stapled to the framework
along the stems and gunwale stringers. The trim was vinyl siding
trim. The canoe weighed 23 pounds and was launched in 1999. Total
construction time was 12 to 13 hours and the cost was 65 dollars.
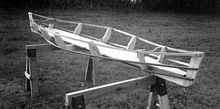 |
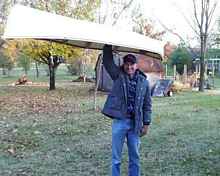 |
My next project was to build an even simpler boat. This would
be a double-ended, flat-bottomed, solo boat for river fishing.
The construction was the same frame and stringer method used in
building the canoe. However, the flat bottom allowed me to simply
cut the stems, frames, and floors with a miter saw and screw and
glue them together. No shaping of the frames was required. This
reduced building time even further.
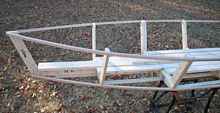 |
An even simpler design. |
A few more boats were built to this plan, including one skinned
with cedar paneling, built entirely with materials bought at a
local home improvement center. In the course of these projects,
I began to formulate ideas for a packable form of this boat.
In 2003 and 2004, I made models to test design concepts, and
continued to develop the idea of a packable boat. In the spring
of 2006, I began work on two of these boats. The boats were 10
feet long and nearly identical. However, one would be built in
three sections, and the other would be made to disassemble into
pieces no longer than 42 inches. Both would have removable fabric
skins. I had theorized that by doubling some framing members and
staggering or reinforcing weight-bearing keelson and floorboard
joints, I could make a wood framework that could be taken apart,
but would support substantial weight. The frames were flat bottomed
and made of spruce. Floorboards were western cedar, and the keelson
and bottom braces were spruce. Stringers were Douglas fir. The
skin of the packable boat was originally made of vinyl upholstery
fabric. The sectional boat had a skin fashioned from a blue tarp.
The skin was laced to the frame at each station with tarp clamps
and ropes or bungee cords. These two boats were built in one weekend
for about 60 dollars each.
This is a description of the construction of the sectional boat.
Identical pairs of frames were built at stations two and four.
Floorboards and bottom bracing were cut to butt together over
these paired frames. After the framework was screwed and glued
together, I drilled holes through each set of paired frames for
4 carriage bolts and bolted the paired frames together. A bridge
brace was bolted over the gap in the central floorboard for added
strength. The skin was a blue tarp fitted with tarp clamps and
laced to the framework.
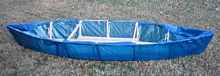 |
Sectional boat |
With the skin removed, the 10 bolts and their wing nuts can be
removed and the boat broken down into 3 sections of 3 to 3.5 feet
in length. Assembling the framework and replacing the skin takes
about 15 to 30 minutes.
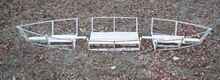 |
The sectional boat apart |
The packable boat was built to be screwed together. No glue was
used. Floors at stations 2 and 4 were identical pairs. Thwarts
were added at stations two and four. These added strength and
made a surface for attaching stringers. Joints in the floorboards
and bottom bracing were staggered so they did not "break"
over the same frame. This produced a framework of about 60 pieces.
Each piece was marked to facilitate reassembly and a skin of vinyl
upholstery fabric was laced to the framework.
In the summer of 2006, I disassembled the packable boat in preparation
for my vacation. I packed the boat, along with extra fasteners,
ropes, and bungee cords into a flight cover for a golf bag. This
was checked as baggage on a flight I took to Bermuda to visit
friends. The bag and all its contents weighed about 40 pounds.
On my arrival in Bermuda, I was asked what was in the bag, as
it was obviously not a set of golf clubs. I told the customs agent,
"It's a boat." To this he replied, "Oh, I've got
to see this." The boat was reassembled at Nine Beaches Resort.
This caused a small stir as word got around that a guest at the
hotel was building a boat.
Boat in a bag |
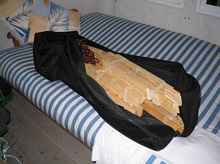 |
Nine Beaches |
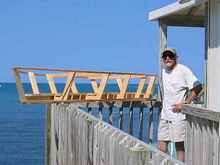 |
I used the boat on that vacation and, when I returned home, it
was left disassembled in a closet in the apartment of my friend,
Carolann Terceira. I cannot express what a tremendous kick it
was to see the culmination of this effort.
I have since returned with an improved skin of Odyssey III cloth.
This came about at the suggestion of my good friend Chuck Beatty
of ABC Marine in Phoenix. The boat now resides upstairs at Carolann's.
I have used it every summer since 2006. I reassemble it at Carolann's
and carry it to the water in her car.
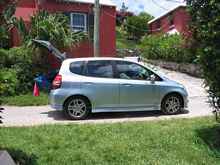 |
Boat sticking out the back of the car. |
I have continued to experiment with and to make improvements
and modifications to these boats. An elegant method of mounting
gunwales was suggested by Tommy Underwood. The use of Odyssey
III is a great improvement. It looks better, is lighter and lasts
longer than vinyl fabric. It comes in many colors as well. A sailing
rig of bamboo has been developed for these boats. I have recently
built a transom-sterned, two person version of this boat as well
as a replica of an 1890 racing canoe, and a seven foot boat for
my great nephew. With some added time and care on the part of
the builder, these boats can be beautiful as well as cheap and
functional. They are also considerably more rugged than they appear.
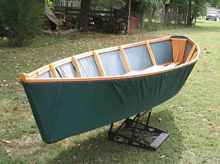 |
Fully skinned. |
While I am proud of this building plan, there are compromises
in these boats, as there are in any boats. None of these is an
insurmountable challenge. The skin, while very tough, can be punctured.
This is part of the bargain with any removable skin. Patches can
be affected with duct tape, and I carry a spare skin with me in
rough conditions. The skin can be replaced in about an hour. The
weakest structural parts of the boat are the stringers. They can
easily be repaired or replaced if broken. Boats of this type are
limited to those designs which have a flat run to their bottoms.
These compromises are offset by a number of assets. Their ease
of construction and low cost make these ideal boats for experimenting
in design. The packable boat and the sectional boat present the
builder with portability at a reasonable price. They can be transported
by car, in flight baggage, and on four-wheeler to places which
would be inaccessible otherwise. The sectional boat can be used
as a tender for small sailboats and can be stored out of the way
in a garage or storage building when not in use. It can even be
stored in an apartment, and can be carried in a pick-up truck
with the tailgate closed. The packable boat offers even more options
in transport and storage. It can be stored in a closet if necessary.
Not to be overlooked is the fact that these boats are fun to build.
The boats are, essentially, life size erector sets. They are fun
to assemble and use, and their assembly offers the opportunity
to educate children and non-builders in the pleasures of building
a boat.
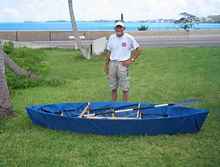 |
Blue version |
*****

|