To
Part One
Last time I proposed a design with a flat bottom. While the sides
were flared for rowing, still it was a squared pram style boat.
Now let's look at lapstrake boats. Maybe we can find a way to
simplify the building process. This will be hard to do. As I said
before, these lapped boats must be attached along their sides
from stem to stern. That takes fine planning for the shape of
the plank. Unfortunately, to turn the hull from horizontal at
the keel to vertical at the bow means the planks will have to
change their exact shape.
The key to this shape is creating the sharpest turn of the bilge
above the waterline. That saves so much fric-tion. It also enables
the planks to draw the water back alongside the keel as the water
proceeds aft. Below is the Herreshoff H-28, with the waterline
in red:
Francis Herreshoff wanted to keep the water under the turn of
the bilge. The two waterlines inside the red line are parallel
waterlines, designed to encourage the waterflow back to the keel.
When the waterpressure is on the keel, just the slightest touch
of the tiller will turn the ship. Herreshoff designs are known
for their perfect balance.
The problem is this style requires a keel-based building process,
and that needs skill, tools, space, and time. The easiest boat
to build in this keel-based style is probably the Atkin Pixie,
at 14 feet.
In fact, you could put some curve into the stern and the frames
for a perfectly nice lapstrake hull. These pro-portions are just
right. It reminds me once again that shape, proportion and balance
are more valuable than the building style.
Stitch and glue requires plenty of glue, ties, and tools. Clenched
nails takes a ladder, lots of frames, being able to reach inside
while you hammer outside, and plenty of hand strength to clip
off the nail heads. Then the nails have to be completely covered
on the outside of the hull. Glued lap takes many clamps, fasteners
which have to be removed, their holes filled, and plenty of frames.
So you can see what you're up against. For a better boat, more
work; with less work you get less performance.
In this style, six panels is the least you can have and still
have the boat behave like it should. But making the bottom flat
means the bottom chine is in the water, creating all kinds of
eddys. The only way to obviate this is for the bottom side panel
to lay about 15 degrees above horizontal, softening the angle.
The Nutshell Pram does this, but it requires all kinds
of extra work to make the entire design work.
I haven't found a radical way to simplify the process of lapped
sides. But maybe we can find some small ways to create simpler
steps, at least in a few places.
The great advantage of a curved hull in a small boat is to create
more room without settling for a fat slow wa-terline. Having the
topsides hang over the waterline but not in the water gives us
room without ruining the performance of the craft. The best example
I've ever seen is the Warren Messer 9.5 Laura
Bay. Two of its' hull panels are beautifully
above the waterline.
However, Laura Bay needs eight panels and thousands
of ties. This can't be avoided without altering the shape of the
panels to the point of ruining the boat's performance.
Can we simplify construction any on a multi-panel boat of our
own? Not entirely, although there are a few things we can do.
First, the set up. Stitch and glue requires a flat surface, spacers,
and the ability to align the sides squarely. It's similar to the
old WAAM (see Least Boat Part 1), only you're wrapping the sides
vertical-ly before you glue them into the shape you've created.
Warren has done a great job of explaining stitch and glue in the
six part article on Laura
Bay. What he has to say cannot be improved upon.
Plank on frame build-ing needs a support structure, braces, many
frames, battens and a flat floor. The problem with plank on frame
is that it is a big boat technique brought down to a small boat.
Maybe we can make some adjustments to it, for small boats.
The first is the frame setup. Here you can see all the parts
needed to adapt shipbuilding to a small boat. Re-ally,
all of this may not be necessary--
You can see the frames have to be rigidly attached to the flat
floor because the rocker of the keel is so great. This is a style
which makes rowing and sailing possible. But in the past, round
bilged boats were put together with a straight keel. That made
it possible to build them right side up, putting less strain on
the men who built them--
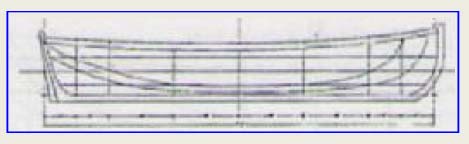
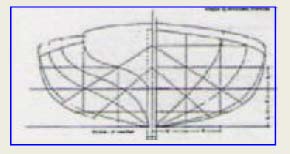
This is the 14 1/2 foot sterrnboat for the Revolutionary Baltimore
Clipper, Lynx. It was built heavy, for sur-vival on the high seas,
with a stout straight keel. I once saw a picture on the internet
of four men standing around a table four feet high upon which
they had built their skiff at 20 feet with a straight keel. The
photo was taken back in the days of 5/8" planks as standard.
You'll also notice very little sheer, probably to keep the ocean
waves out of the boat when at sea, but it also makes the sheer
panel strong.
The two other techniques for fastening frames is to nail them
to a floor, or hold the keel down from above. Dory builders have
been building their boats upside down, bracing their bottom panel
from above for years. It gives the same result without the nails
and without having to level the floor. You can make alterations
if a mistake is realized without tearing the whole structure apart.
Now we come to the bow. The big ship technique is a curved bow
in four parts, with two stopwaters. Plenty of work, and precision
work, too. Here is a copy of the typical big ship bow, with a
dory bow on the right--
I'll take the dory bow. Simpler with plenty of strength. The
bottom panel can be attached to bevel the lead-ing edge before
the outer stem is put on. Now with round-bilged hulls I like the
bow to be flat for at least the first frame before the deadrise
begins. I think this is quite compatible with a strong breasthook,
holding the planks right where they should be.
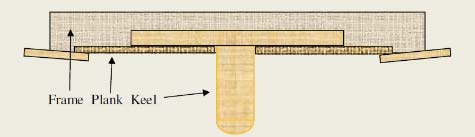
This is the simplest system I've seen. It is designed to perfection
in Warren Jordan's 10 foot lapstrake Dul-cibella,
A keel system with fewer pieces is below. It's not as strong
and requires either through bolts or glue. It was used on plenty
of deadrise sloops in the 1950s.
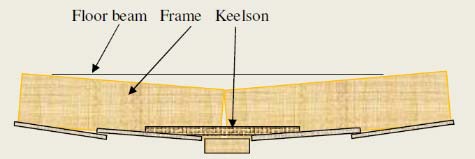
This style has plenty of advantages, one being it can be done
without power tools, just patience and sandpa-per or a little
plane. If your carpentry isn't just right, glue fills the bill.
You can use clamps except where the frame sits; there nails or
screws will do. The main thing to consider is the width of the
outer keel. If you plan on adding a centerboard slot, the outer
keel will need to be the width of that slot at least. I'd much
rather put a centerboard slot on top of horizontal solid wood
than angled plywood with epoxy. It's just the way I was raised.
With beveling the battens, I don't know of any better way than
the tried and true method of using a straight-edge with sandpaper.
Now with spiling, I don't do it the usual way. I go to the store
and buy up all the 2x4 sheets of construction paper-all colors--
and tape them together on both sides. I lay them across the frames,
tape them down at every frame and draw the lines along the battens
on the inside. This has worked for me, although I never did it
on a boat over 9 feet.
Here we can take a tip from the masters, the Herreshoff boat
yard craftsmen. Where the panels lap, the men didn't just take
off some of the edge at an angle, they took off a concave shape.
This way, when the screws clamped down the lap, the wood could
expand into the curved lap of the other plank. I've exaggerated
it here, the concave is slight.
One of the tasks of lapstrake is the gain at the bow. With 5/8"
cedar planks these gains were fairly easy to cut, and many a builder
has shaved them by hand and eye. They can be eliminated by using
a jagged edge at the stern--
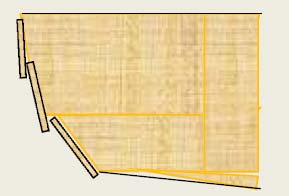
But now the bow is a different matter. With plywood, shaving
a gain would shred the plywood edge and weaken it. So what we
do is like a gain, only along its vertical edge. The plank comes
into the bow keel, which is fairly wide as I have shown.
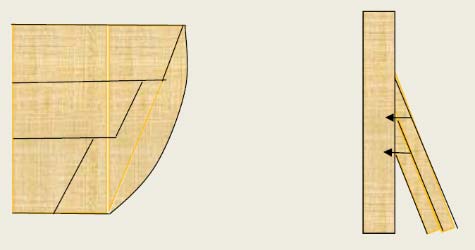
The arrows represent a tiny nail, a long staple might do. Its'
purpose is to hold the plank flush while the glue sets. Then I
drop glue inside the joint, using gravity to fill it, and then
I put a backing inside. I haven't shown the backing, but it is
solid wood, a small piece which can be put on first. I stick it
in firm enough for the pres-sure of the sides to keep it there
until the glue dries. If it isn't a perfect fit, I'm not concerned;
its' purpose is to take the pressure off the front of the panel.
The front of the panel is not a perfect point since beveling the
inside face will flake the point off somewhat, but that's all
right. It gives me the opportunity to pour glue upon the front
of the panel, protecting it from the bouncing of the water.
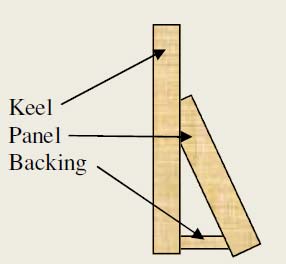
I have exaggerated the scale somewhat, to show it. It has taken
me more time to draw it up here than it does to make it. I use
sandpaper to hand sand the inside face of the plank, going back
and forth with the grain. I don't try to get a perfect fit, the
nail and glue will fill it in. If you have power tools you can
cut an accurate angle, but the forward point will still flake
off some. All of this doesn't take much time.
I fill the gap between the backing and the panel with sawdust
and glue, letting it drip down. I'm actually more concerned with
a flush bottom panel than this technique. With the overlapping
style at the bow, this works best with three or four panels per
side. The lowest panel should be the widest, the highest one the
most narrow.
Now as to cutting the bevel for the garboard. Cutting a rabbet
takes a machine or plenty of hand and eye la-bor. So this is what
I have done. I use heavy wood for the keel instead of a keelson,
but I don't rabbet it. I bevel the bottom surface.

The way I do this is to draw an arched line on the side of a
2 x 4 with a batten and then use a straight edge to bevel from
the line to a straight line 1 inch in from the edge, gradually
as the angle changes.

This is not to scale, I've enlarged to show you how I did it.
This can be done with 1 x 4, it's just that there's less space
in which to land a plank. If you use a metal fastener it will
have to be inserted vertically, regardless of the angle of the
plank, otherwise a tiny split might emerge from underneath the
plank. The one limitation of this technique is that it works best
with a double ender, in the Ian Oughtred manner. In some boats
the keel width will narrow, so that the straight line on the bottom
of the keel will curve in at the bow and stern, alt-hough not
very much, maybe less than an inch.
Keep in mind that what looks like a big mistake in the garage
isn't always noticeable when your great ship is in the water and
cruising out. Gaps disappear in the presence of glue or paint,
and if a plank isn't perfectly fair down to the last centimeter,
remember Francis Herreshoff accidentally bent a waterline in for
Araminta. And when your boat moves through the water, the ripples
will sound like applause.
Finally, I use plywood cut in the shape of a boomerang with the
angle inside to bevel. For instance, if the an-gle I want to bevel
into a stem is 25 degrees on each side of the stem, I cut from
3/8" plywood a shape I can hold to sand the bevel like this--
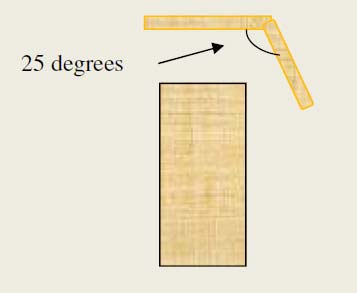
With sandpaper on the inside, I slide it back and forth until
I've got the right angle. I've used these boomer-angs on bows,
stern transoms, chines, and to round off the bottom of frames
to take a rocker. I stiffen the out-side with a 7/8 x 1 1/8 piece,
glued, which serves as a handle, too.
*****
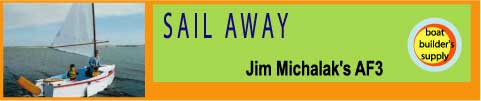
|