As a child I started my sailing career in Sabots. We sailed from a yacht club situated on Cleveland Point – an idyllic location on Moreton Bay, not far south of Brisbane.
In those days I was very small (six years old, I think) and the Sabot struck me as being plenty big enough – even a crew of two. We raced on Sundays and once a year the club arranged a ‘Cruise’ to Horse Shoe Bay on Peel Island. Our faithful old pick-up Boat, Alert, followed the fleet over and back, keeping a particular eye on the Sabots, which were the smallest boats in the fleet. The total distance covered was not much more than ten miles, I guess, but it was always the highlight of my sailing year.
The adults in the club sailed bigger boats, like Flying Dutchmen, an Yvonne, a Quick Cat, Moths, a Graduate, a Trainee Dinghy. Later in my time there, I saw many Jack Holt designs such as the Lazy E, Mirror Dinghy, Mirror 16, Heron, and 125 along with boats from other designers – OK Dinghy, Arafura Cadet, Arrow. What made these boats different from what we see nowadays is that they were almost always home-made.
One day I went for a sail onboard a de Havilland Corsair, which was made from molded fibreglass. I was in awe of this shiny craft, but little did I realise how much that style of production boat would change the club scene.
What I am talking about happened in the sixties and early seventies and seemed to mark the end of the great period of racing in home-made boats. I know that is a sweeping generalisation, and that boats have continued to be built by their owners. But, the majority of club dinghy and catamaran racing is conducted in commercially-built production boats.
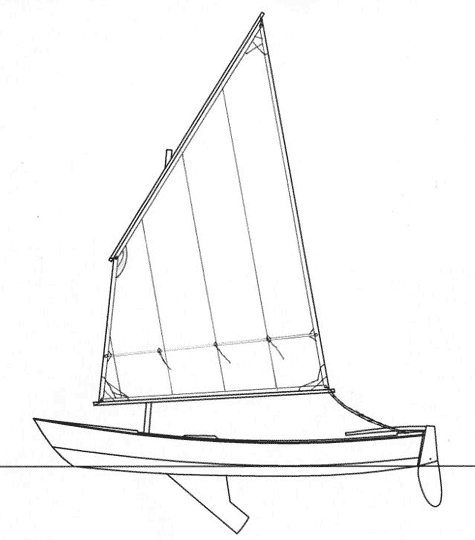
There has been a resurgence in home-building over the last decade, thanks to the availability if high-quality epoxy, and encouragement from a multitude of fine publications. Most of the building seems to me to be directed towards cruising boats with only a limited number of racing classes continuing the tradition. Many excellent plans are available these days - if you want to build a boat, the range of plans has never been better. But you must be very careful when choosing, because some designers are very good, but there are a lot who are not up to standard. Do your homework, and don’t take things on face value.
Stitch-and-Glue (or Taped-Seam, or Tack-and-Tape – whatever you like to call it) is a method of construction which is particularly well suited to the amateur builder with limited experience. The first boat I remember seeing that was built using this system was a Mirror Dinghy back in the late sixties. Many people had been experimenting with the construction method, but Jack Holt really popularised it with his Mirror. The early boats were built using polyester resin and suffered from delamination. But these days everybody uses epoxy and the adhesion problems cease to be a concern.
What is the major difference between a Stitch-and-Glue boat and one built using another popular method – Glued-Lapstrake (Clinker) for example? The real difference is that a Stitch-and-Glue boat can be built without a building mold and strongback, resulting in an enormous saving in cost and labour for someone building a one-off boat. Yes, I know that some of you will tell me that there are other construction methods which can allow the building of a boat without a building mold, but in those specialised cases the principles employed are the same as those in a Stitch-and-Glue design.
The critical factor in making it possible to build a boat without a building mold is having accurate shapes for all of the hull panels, so that they can be cut out from flat sheets of plywood. If you imagine peeling a banana, discarding the bit you eat and then putting the skin back together you will understand what I mean. If the pieces of banana skin are put back together with all of the edges lined up, the result will be something with the exact shape of the original banana.
Now, the shapes of the panels or planks of a boat are very different when laid out on the flat, from the shape our eyes see on the curved, tapered and twisted side of the completed hull. The geometry involved can be extremely complex, and the design of a hull built from flat panels (of plywood, aluminium, steel, etc) must ensure that none of the panels are forced to take up a compound curve – by that I mean that the surface of the hull must always take the form of part of a cylinder or a cone – nothing else will work.
In the past, designers of Stitch-and-Glue boats would design a hull using known methods for producing a ‘developable’ (i.e. no compound curves) hull shape. The boat would then be built over a conventional strongback and mold, and would be planked up normally. A pattern would be taken of the resulting panel shapes, allowing subsequent hulls to be constructed without a mold. This is a very good system, but today we have available a wide range of computer programs which allow the determination of developable panel shapes directly from the initial design. Not only is this a huge saver of time, but it allows the design of much more complex shapes due to the massive number-crunching capabilities of the computer gear.
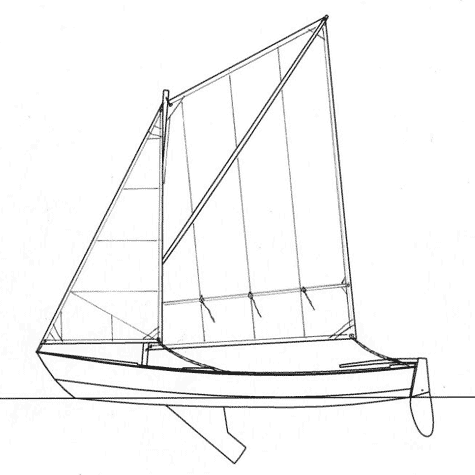
A friend of mine was very taken by my 15ft Phoenix III design. Phoenix III is definitely not a Stitch-and-Glue boat! She is built over a substantial strongback and building mold, and is planked using the Glued-Lapstrake (Clinker) method. By most comparisons she is not a difficult boat to build, and people say she has an elegant and shapely hull. However, my mate reckoned that the construction method was beyond his capacity, but he still wanted the boat and he was confident of his ability to build a Stitch-and-Glue boat. In fact, he had previously built a Stitch-and-Glue Phil Bolger-designed Cartopper which turned out to be light, strong, beautiful and durable.
I set about designing a boat which would be the functional equivalent of Phoenix III but be built as a Stitch-and-Glue hull. The result is called First Mate – she uses the same mast, centreboard, rudder, sails, and internal layout as Phoenix III, but the hull is a multi-chine Stitch-and-Glue structure which can be sewn together from predetermined plywood panels shapes and sealed up with epoxy and glass tape. I estimate that the entire hull could be built in half the time required for Phoenix III.
Although the design is finished, full building plans for First Mate are still under development, as is the instruction manual. I’m expecting to have the final product available in about a months time. She will then join my existing range of published designs which include Phoenix III (a 15’ clinker sailing dinghy), Flint (a 14’7” recreational rowing boat for oars and small outboard), and Alby (a 7’7” pram dinghy for sail, oars, and outboard). For those who are interested in building a simple Stitch-and-Glue boat, I recommend that you read Instant Boatbuilding and Build the New Instant Boats both written by Harold “Dynamite” Payson, Boatbuilding for Beginners and beyond by Jim Michalak, and Devlin’s Boatbuilding by Sam Devlin. |