Along with thanking Paul and Marya Butler for
their great article
on using scrapers, I wish to offer a tip to further
exploit the advantages of these extremely useful and
often overlooked tools. For using scrapers to put
a mirror smooth surface on soft woods and on harder
woods, one must continue the sharpening process outlined
by the Butlers to the next level. However, continuing
the process, as described below, will result in a
very sharp scraper, though one with an edge that may
not hold up as well for doing the rougher scraping
of epoxy with its various fillers and for removing
hardened paint. The coarser edge produced following
the process as described by the Butlers would be more
suitable for that application and would be easier
to refresh.
1. Squaring the edge of a regular or a radius cabinet
scraper is easily accomplished without a vise by mounting
your sharp mill file in a slot cut into a block of
wood. Filing of the scraper edge is then done parallel
to the edge. The wood block serves as a fence like
that on a jointer, to hold the scraper square to the
cutting edge of the file.
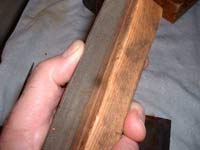 |
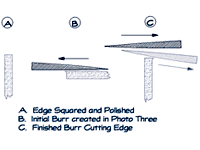
|
2. A continuation of Step 1 is polishing the surfaces
and the square edge of the scraper with a sharpening
stone. Photos ONE and TWO show polishing the flat
surfaces of the scraper and polishing the square edge
of the scraper using the sharpening stone box edge
to help maintain a square edge while polishing. To
keep my hands and the camera clean I have demonstrated
the polishing here without the couple of drops of
mineral oil I would normally have applied to the medium-hard
natural Arkansas stone. To prepare the scraper for
softwoods such as pine and cedar, I would further
polish the scraper to a mirror finish on a “surgical,”
black hard Arkansas stone. Softwood scraping requires
a sharper scraper than hardwoods does as the grain
will more easily tear out instead of being cleanly
sliced.
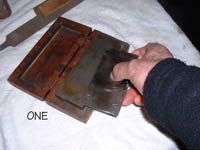 |
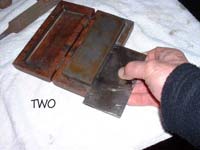
|
3. A polished, hard steel burnisher is the tool in
my hand in photo THREE. The burnisher is drawn almost
flat across the scraper surface and edge simultaneously
in the directions shown. The purpose is to draw out
a burr edge of metal with the friction and pressure
of the burnisher in the same plane as the surface
of the scraper. If I was not taking this photo, my
right hand would be holding the scraper flat to the
board or to a work bench edge. Practice will help
you achieve a firm smooth stroke with the burnisher.
With the malleability of the steel scraper, you are
microscopically deforming the formerly square edge
you have just filed and polished.
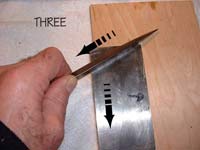 |
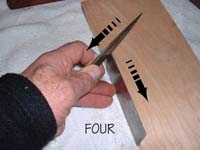
|
4. Please imagine that the scraper in photo FOUR
is being held in a vise. Drawing the burnisher firmly
across the burr edge I just created in step 3 (which
is now pointing up), I burnish that burr out at 90
degrees to the face of the scraper, and, with a second
pull of the burnisher I draw and roll that burr edge
down about 10-15 degrees. That second pull with the
burnisher is basically the final step to creating
the cutting edge. Again as I was taking these photos,
if the scraper actually being held in a vise, I would
also have had my right hand fingers applying pressure
to the tip of the burnisher as I was pulling and simultaneously
sliding it along the length of the burr edge. Please
refer to the above diagram of a, "magnified,"
scraper edge.
The more highly polished the initial squared edge
of the scraper is, the sharper the edge you will finally
be able to create with the burnishing process. There
are a couple more tricks to refreshing this cutting
edge as it dulls with use, but basically begin again
with the file to remove the old burr edge, then proceed
with the polishing and burnishing. Some scraping applications
benefit from initially filing the scraper edge at
a slight angle, instead of squaring it, and then pulling
the cutting burr from the acute angle edge with the
burnisher as described above. Triangular and oval
shaped burnishers are available wherever cabinet scrapers
are sold. Excellent scrapers can be made by cutting
up old steel handsaw blades to the shapes and sizes
that you want. That pile of ancient, dull Henry Disstons
in your shop are just waiting for a useful reincarnation.
Wear some gloves and with some practice, you will
be amazed at the results you will be able to produce.
Donald Freix
Fish Creek

|