I’ve enjoyed the benefits of a weighted
rudder on my boat for a few years now. Since my Weekender
plans did not include this feature, I based my modification
on Jim
Michalak’s instructions.
Melting and pouring the lead was a time-consuming
and potentially dangerous operation. But a bigger
problem was that over time the rudder’s wood
receded from the lead leaving a gap that allowed water
to infiltrate and form rot. Even after treating the
rot with antifreeze and filling the gaps with epoxy,
the gaps reappeared.
My sailing buddy and all-round mechanical guru, Dave
Richards, found a better way to add lead to his rudder,
and eliminated both problems mentioned above.
The secret is to use flat strips of lead that you
don’t have to melt, and epoxy them into a cavity
in the rudder.
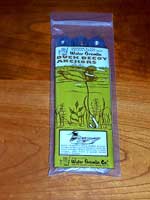 |
Six duck decoy
anchors totaling two pounds |
Duck decoy anchors are perfect. At a big-box sportsman’s
store I purchased two packets of decoy anchors, each
packet containing 6 anchors. Each anchor weighs 4
ounces, so each packet has 2 pounds of lead. Two packets
give me the four pounds of rudder weight JM calls
for in his Frolic2
design. (This is, of course, what we euphemistically
call The Next Boat.)
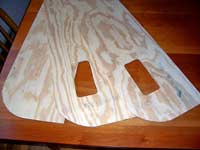 |
Three pieces
of 1/4" plywood are laminated to form the
rudder. Note that holes have been cut in only
two pieces. |
The next step is to create the cavity in the rudder.
The Frolic2 rudder is made by laminating three sheets
of ¼” ply. (Here’s where it REALLY
gets good!) If you stack the decoy anchors three high,
they are just shy of ½”. That means you
can create the cavity by cutting holes in just two
of the three plywood sheets. Once the holes are cut,
and the lamination is complete, all that’s left
to do is epoxy the decoy weights into the cavity.
Use thickened epoxy for the final pour, and when it
hardens, sand it level with the face of the rudder.
Prime it, paint it, and go sailing.
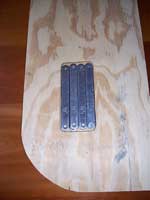 |
The plys have been laminated together, and the
twelve decoy weights all fit neatly into the
cavity created by the holes cut in two of the
three plys.
|
Dave’s rudder was made from solid stock, so
he used his router to create the needed cavity. After
two seasons of using his weighted rudder, Dave hasn’t
seen any water-seeping, rot-cultivating gaps. In fact,
if you have to look very closely to see where the
lead was added.
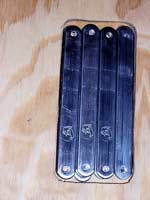 |
Close-up of
the lead in the cavity. |

Other Articles by Bill Paxton
|