A few of the Western
Oregon Messabout guys got together a couple
of weekends ago to build 2 little D-5's to donate to Jack
Brown's Depoe Bay (Oregon) "Killer Whales Rowing Club"
kids boating group. The "Boatbuilding Messabout"
took place at David Graybeal's Arbor Woodworks in Portland,
Oregon. |
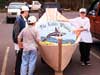 |
We start out drawing patterns
on plywood and cutting them out with jigsaws and circular saws...
Chris gets ready to make the first sawdust. |
 |
Veteran boatbuilder, Steve Miller, jumps right in |
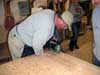 |
Joe Nelson's daughters watch for tips on how to help Joe
with his Core Sound 20. |
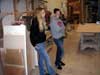 |
David Graybeal and Case "Dirtdude". |
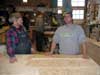 |
There is lots of shop envy amongst the coots. |
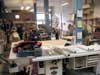 |
Jim Ballou gets ready to cut out twarts. |
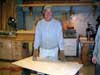 |
Chris and Jerry carefully NOT cutting the workbench. |
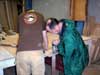 |
Dirtdude says we can cut side and bottom panels with a
circular saw, so we do. |
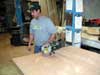 |
Joe Nelson, twarted again. |
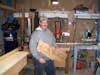 |
We drill holes along the front,
rear, and bottom edges of the sides. While the photographer
is getting coffee, we brace the thwarts, attach the sides, and
attach the sides to the the bow and transom. We also test fit
the bottom pieces.
The next step is pausing for
coffee, conversation, and admiring our work.
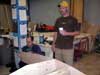 |
Jerry and Chris prepare the starboard side
for stitching to the transom. |
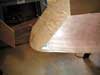 |
Wire ties used to stitch boat. Placed 1/2 inch from the
edge every six inches. |
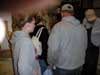 |
Everyone in the witness protection program avoids the
camera. This is really a picture of Frank. See finger covering
lens. |
Now, the boats are turned right
side up. We flex the hull until the diagonal measurements match,
then we begin putting masking taping around where the fillets
will go. Also, the center seam on the bottom is taped to prevent
the epoxy from running through the seam onto the shop floor.
After the masking tape is in place we mix epoxy and coat
where the fillets will go..... |
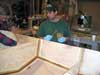 |
.....basically anywhere one piece of wood meets another
piece of wood. |
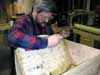 |
Pat Patteson mixes wood four into a batch of epoxy. |
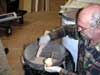 |
The thick epoxy mixture is used to form fillets at all
the seams. |
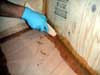 |
We found that having one person continuously mixing epoxy
(three pump batches) for each person installing fillets
kept both people busy. |
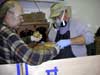 |
Pumps make dispensing epoxy and resin convenient. |
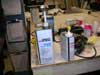 |
Brushes get gooed up, so have lots. |
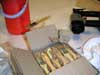 |
Lunch only tastes a little bit like epoxy. |
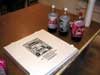 |
Once the fillets are in place,
the masking tape is removed and all the wood surfaces on
the inside of the boat are coated with epoxy. |
|
The inside of the boats are coated with epoxy..... |
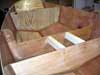 |
.....so it's time to clean up then head to the White Eagle. |
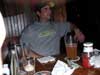 |
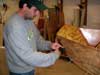 |
Cutting off the wire ties stitching the boat
together. |
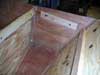 |
Cut seat frame pieces, drill holes, coat one side with
epoxy, and attach frame pieces to boat. |
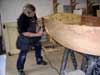 |
Grind off screws that attach seat frames. This step necessary
if too long screws used and installed from the inside. Oops! |
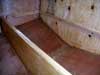 |
Cut seat tops from scrap plywood. Fit need not be precise
as gaps can be filled with thickened epoxy. |
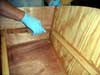 |
Mix up thickened epoxy (adding cabosil and wood flour)
and coat the surfaces where the seats will attach. |
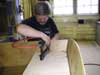 |
Attach seat tops. |
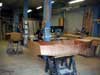 |
Two boat ready for trip to Bend. Next steps will be epoxy
of exterior and fiberglassing of seams. |