Reply to Jeff Gilbert
Hello Chuck
Was just reading the “how cheaply can I build a…. “ from Mr. Gilbert.
Every designer has his own ideas how to design a boat, no comments here.
However, I fully agree with his statement that plywood/glass/epoxy composite is the most cost efficient way to build multihulls. I speak here from an experience over a period of 26 years.
However, there is more to it.
I send you as attachment the study plans from our PELICAN. A live on board go anywhere catamaran with a length of 11.5 m and a beam of 6.5 m.
We built this boat between 1989 and 1990 for Dutch Guilders 34.680, - *, in Euro 16.000, - , in US $ 19.520.
*The cost for the boat as shown is including new mast, sails, anchors (20x 20 kg + chain and 150m anchor rope) Yamaha 9.9 four cycle outboard engine, wind generator, water maker, GEL batteries, log, wind speed indicator and direction indicator, echo sounder etc.
I was searching around a bit and was coming to the conclusion that you can build the boat today for about 90 % more , which would mean US $ 37.088,-
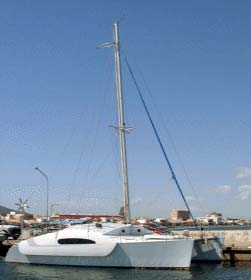
The picture above shows the boat as it is now. Changes we made:
Wheel steering instead of tiller steering (hydraulic system US $ 750,-)
Vertical reefing Wishbone gaff rig instead of full battened main, sail cost US $ 2150,-
Specifications |
|
Length over all |
- |
11.50 m |
Length on water line |
- |
11.30 m |
Beam |
- |
6.50m |
Beam cl/cl |
- |
5.20m |
Draught at 4600 kilograms |
- |
0.65m |
Draught rudder |
- |
0.75m |
Weight empty |
- |
2200 kilograms |
Weight load to cwl |
- |
4600 kilograms |
Mainsail |
- |
38 m2 |
wishbone main |
- |
36 m2 |
Jib |
- |
17.6m2 |
Reacher |
- |
48 m2 |
Storm jib |
- |
7.2 m2 |
|
|
|
L/B ratio cl/cl |
- |
46% |
L/B ratio hulls |
- |
1: 16 |
Maximum righting moment |
- |
12500 kg/m |
Auxiliary power |
- |
9.9 HP |
The hulls have a high aspect ratio and are trapezoid shaped. This hull shape is easy to build.
They can be rounded of in the bow area for soft entrance into waves. The chine should have sharp corners after about 1/3 from the bow to lessen the running resistance. In fact, these hulls are aircraft wings standing vertical in the water. As leeway preventers, we use anti-vortex wings (comparable to winglets on aircraft wings). The are more efficient as low aspect ratio keels than and as efficient as dagger boards. Anti-vortex wings cost almost nothing and are very easy to build. With this arrangement, the boat sails to windward as a very good monohull with the same water line length. Pelican sails about 10 % faster as a mono hull. When you free the boat for about 5 degree, she is about 20 % faster. We never encountered any multi hull, which could match the height to windward. If you like to understand how they work, go to our web page and load the anti-vortex article down.
Our medium speed over all our sailing time is 9.2 knots. Depending on sea state, we slow here down between 11 and 12 knots, because it gets very noisy above this speed. To windward, we slow here down above 9 knots depending on the waves.
Maximum speed with the new wishbone sail was 17.5 knots. This sail is so power full, that if there is only a zephyr, we do not motor any more.
Every effort was made for a hydro dynamical and aero dynamical clean boat. This means also no high superstructure like a deckhouse or a propeller permanent under water.
When you work with Epoxy, it is advisable for best result to work not in the open. When you have to rent a workshop, this will cost you money; heating and lighting are other cost factors. A short construction time is a way to save you money. I made for all my designs also a time calculation. Of course, the building time will be different for each person. However, if you design for short construction time any builder will be faster as compared to a complicated design.
To make this more understandable here a very short construction description.
The hulls are built on seven bulkheads, five stringers and very important a backbone former piece.
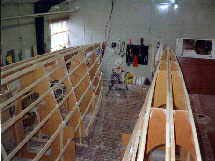 |
The hulls are built on seven bulkheads, five stringers and very important a backbone former piece. |
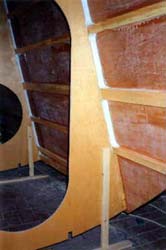 |
As can be observed on the picture, we use no stiffeners around the bulkheads. Instead, we apply fillets and glass fiber tape after planking. These safes time and give a very smooth hull. |
We built both hulls standing parallel to each other in 500 hours (ready painted). Turning over was a non-event because the are very light. We di’t it in rope slings with five persons.
After prefabrication of the mast beam, cabin entrance beam and aft beam the hulls where moved to there correct distance from each other. We used alignment holes for the correct place of the beams and glued them to its corresponding bulkheads. Next steps, and there are a lot, are to build the inside.
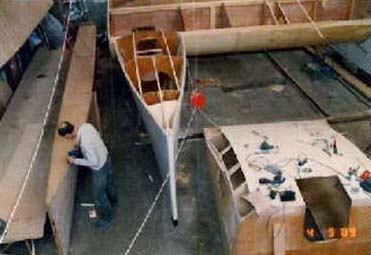
Pelican and a DUO 800 under construction
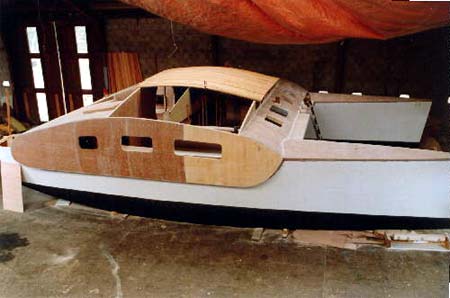
To speed up construction, the cabin roof is strip planked with red cedar strips and tree layers of glass fiber.
The boat was ready to sail after 13 months.
The next boat was built by one person in precisely one year. He was working 8 hours per day on the boat. He worked never on Sunday and had 3 weeks holiday. Working hours to finish the boat 2340 hours. It was his first boat-building project, by the way.
Now why is this design and by the way all of my plywood/glass/epoxy designs so light?
I use, as far as possible, any part of the boat as structure. Example, the saloon seats. These are used to strengthen the mast beam. The mast can push down with 16.000 kilograms!
The whole cabin is designed like a big beam. When a boat is light, it means there is also less material used, which accounts for lower costs. An open beam catamaran of the same dimensions will be heavier. To support the mast load the beams have to be very massive. To spread the load from the beams to each hull additional material will be necessary, which makes the construction more difficult, time consuming and will cost more.
When you compare the weight of a mono hull with the same waterline length to the weight of a catamaran the weight difference is even more obvious. Again, this will cost you more.
I send you as attachment a part of an article from the French Multihull Magazine from January of this year. This article describes the construction, of a plywood/glass/epoxy catamaran with a length of 13.65 m. This boat was built for Euro 45.000,- or US $ 54.000,-.
So, Mr. Gilbert is not wrong believing that dream boats when careful chosen can be built for a reasonable price if build with plywood.
I am sorry for my bad English, I am from the Netherlands, living in France, so I get sometimes a bit mixed up.
Cheers
Bernd Kohler
www.ikarus342000.com/
|