Jonsboat
by Dale Beachy
My brother-in-law is an avid fisherman, so when
I drew his name for Christmas I decided to build a boat for
him. My initial plan was to build a small one-man boat that
he could tote around in the back of his pickup truck. However,
a phone call to my sister nixed that idea. “If you are
going to build a boat, build a big boat.” So it was decided
that a larger boat should be built, one that could carry several
of his fishing buddies. Since this would require a larger budget,
the boat would be gift from my sister, my parents and me.
We decided on the Jonsboat
designed by Jim
Michalak. I purchased his book Boatbuilding
for beginners (and beyond). The plans were easy
to read and understand, and the book provided many tips and
useful pieces of boatbuilding information. In addition, it contains
building plans for several other boats.
I did make some minor modifications to the plans.
I placed the chine logs on the inside, rather than the outside.
I did this purely for aesthetic reasons. I also extended the
front deck by about 12 inches to make a larger platform for
fishing. The front bulkhead is sealed and I installed deckplates
to access the dry storage space created under the fishing platform.
After reading a Jonsboat article at Duckworks
website, I decided to use ½ mdo plywood for the entire
hull. This is my first boating project using mdo, so I am anxious
to see how well it will work. I used ¾ inch exterior
plywood for the seats rather than the ½ plywood indicated
by the plans.
The bulkhead framing was glued with Gorrilla
glue. The hull bottom and frames were glued with PL Premium
adhesive. I chose PL after reading that it hardens and is not
flexible.
I have enclosed several photographs of the building
process.
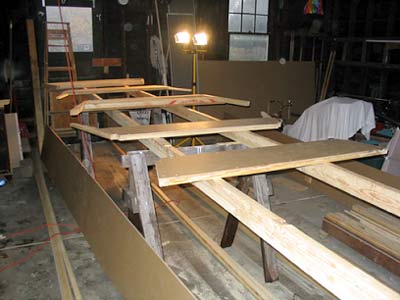
I built the boat upside down
using two 18 foot 2x4s as a frame to hold everything straight
and in place.
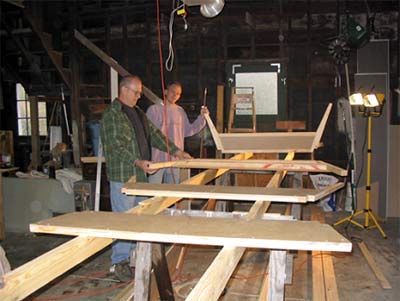
My dad came down and helped
my assemble the parts. It took most of the day, working steadily,
but it was rewarding to see the boat go 3 dimensional.
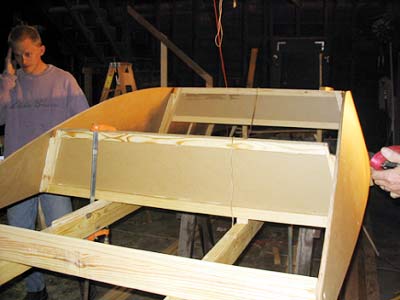
In this photo, you can see the
notches we cut in the bulkheads for the internal chines. You
can also see the 2 x 4 that makes up the bow of the boat, I
had to cut this piece three times as I kept making mistakes….it
had been a long day.
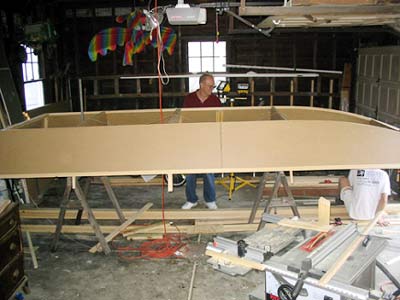
The next day, we installed the
gunnels.
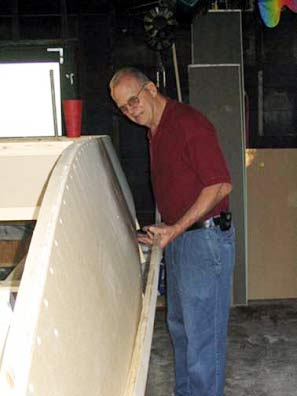
We glued and screwed these in
place using Gorilla Glue and galvanized wood screws.
After I finished assembling
the boat, I trailered it to my father’s garage so we could
fiberglass the bottom. I purchased the epoxy supplies from RAKA,
and I was very pleased with their epoxy and service.
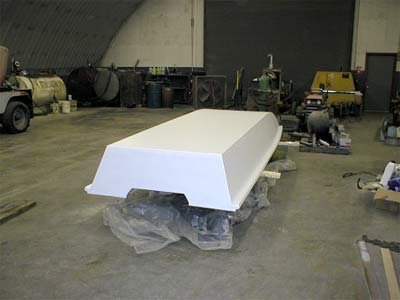
I did not round the chines enough
and since we were pushed for time we had to abandon our plans
to epoxy 2 inch tape on the chines. The tape kept popping up,
so we just epoxying the hull with 6 oz cloth.
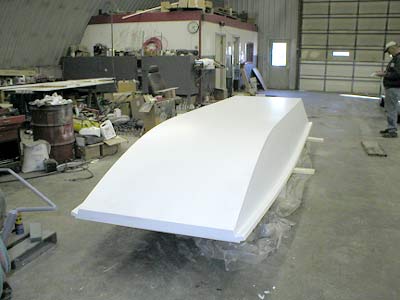
The hull fiberglassed with 6
ounce cloth and painted with one coat of primer.
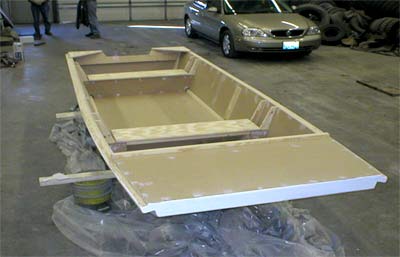
The inside of the hull with
screw holes filled, sanded, and ready for paint. Since the boat
was a gift from my parents as well, they graciously agreed to
sand, fair, and paint the boat.
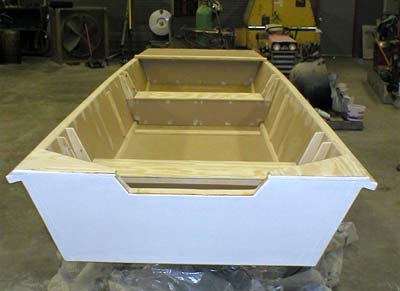
I also used ¾ inch plywood
for the triangular gussets. I plan on installing cleats on these
gussets and I thought this area would need some extra strength.
I cut down the transom for a
short shaft outboard motor.
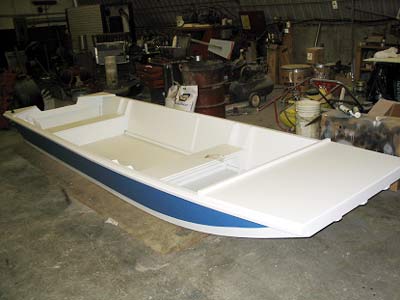
Ready for rigging. The boat
is covered with three coats of paint, four if you count the
primer. We painted the waterline at the 640 lb displacement
line as indicated on the plans.
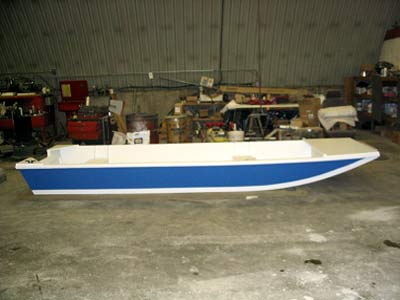
I really enjoyed working on
this project. During the building process, my brother pointed
out that I could have purchased a used aluminum johnboat with
a trailer and motor for only several hundred dollars more. I
responded, “Yes, but it is metal, not wood.” He
just shook his head. Until one builds a boat, I don’t
think some people fully understand that it is as much the process
as the completed product. Thinking back, I wouldn’t trade
the weekend I spent with my father working side-by-side on the
boat for the best-equipped factory-made boat
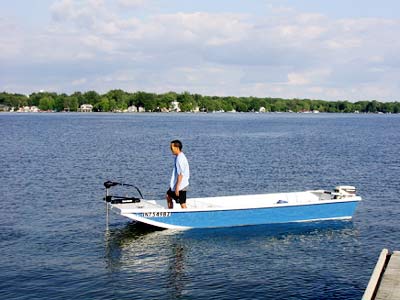
On the water at last…..
My brother-in-law
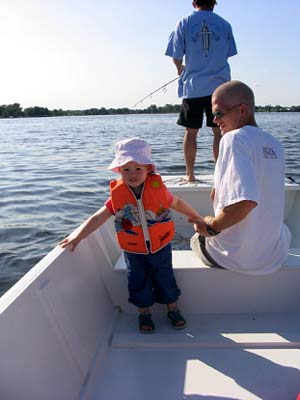
My daughter and I enjoying the
boat. Lots of room.