Cormorant
Over the weekend I was finally able to make a little
progress on Cormorant
(after about a month of being too busy with work-work to do boat-work).
Previously I had gotten
to the point where my bulkheads were all up, 3-D, attached to
the side panels, but my barn floor is dirt, not level, and quite
rolly. I was a bit stymied by the problem of how to get the whole
assemblage level, straight, and untwisted. I wished I had taken
the time to build a strongback.
Finally I hit upon an elegant solution -- sort of an internal
strongback: I took the two 16-foot 2x8s that eventually will be
my cabin beams, and screwed some 2x4s on their edges, to make
a T-beam, two of them.
These I screwed in at a uniform height along the inside of the
cabin openings, which are uniformly 24" wide. So in one fell
swoop I got all the bulkheads (or, all the main bulkheads, from
six feet aft of the bow to the beginning of the cockpit at 22')
lined up more or less straight, and a method to level them all
at once.
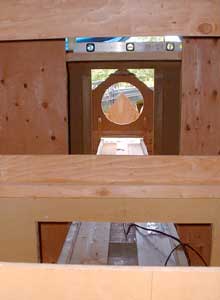
the T-beam in action (click to enlarge)
Similarly, I ran some temporary 2x2 stringers along the bulkheads
that form the aft 10 feet of the boat, to keep them all in alignment.
I leveled everything sideways and lengthwise, banging blocks
of wood under the bulkheads at various spots.
I had already pre-made the entire bottom, with a well marked
centerline, so once I got all the bulkheads lined up, I enlisted
the help of my wife to heave the entire 25'x 5.5' bottom piece
up on top of the (inverted) boat. Fun little project all couples
should try . . .
Aligning the centerlines of the bulkheads with the centerline
on the bottom piece corrected a few locations by an inch or two
(or actually aligned the bottoms of the bulkheads where the tops
had already been aligned by the T-beams), and I tapped in some
nails to hold it all in position. It's probably still a bit off
somehow, but close enough for me to proceed.
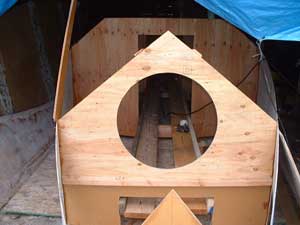
another view of the T-Beam (click to
enlarge)
So the sides are attached and the bottom is attached, and I can
stand inside the hull and poke my head out of the bilge panel
openings. Those will go on last. But anytime I forget to bring
a tool or a screw with me into the boat, it requires a lengthy
trip back to the few easy points of ingress and egress -- back
by the transom or up near the bow. Really makes you think ahead
-- whch is not my strong suit.
Then I epoxy-and-screwed on the cabin clamps and the first lamination
of the sheer strakes. Because the sides are too large to reach
around, I couldn't do this job single-handed, so it again required
the help of my wife, who is amazingly good-humored about it all.
She held the strakes on the outside, while I crawled around inside
the boat drilling in the screws and scraping and cutting myself
on little bits of debris and tools I left lying in there. As we
battled through one little problem after another in getting the
strake aligned properly, I used up my complete supply of bad words,
while she remained unflustered and somewhat amused.
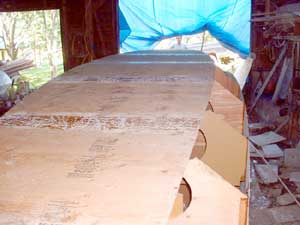
the whale . . . I mean boat so far (click to enlarge)
It all got done successfully before the epoxy cured, and now
the boat is sitting out there in the barn, looking much more formed
and substantial. If I can steal some work-time this week I'll
get the second layer of sheerstrake lamination on, and then I'll
be ready to attach the bilge panels and begin the stitch-and-gluing.
All best,
Garth
|