Chuck was so kind as to
allow me to present my YAGO Project here, and I am more than
happy to do so. This is just a short intro, for more detail
and contact you should then go to YAGO’s website at: |
|
https://www.justmueller.com/boats/
YAGO is a 31 foot steel yawl, and quite unusual in several ways,
for its general concept, for the construction method and finally
for the way the plans will be distributed.
The Concept
I did not really want to build a boat again, I had been there
before and left a good part of my life and health building 4 steel
boats, plus several smaller stitch & glue ply projects, helped
on numerous other projects in WEST, Ferro, C-flex and you name
it, and anyway thought I was far too old and lazy to really get
drawn into this again.
It’s just that my wife kept pushing me to start the final
voyaging boat I had always promised her. Well, guys, there are
wives like that, don’t be jealous… ;-)
I had kept the plans for a 37 footer tucked away nice and warm
in a drawer, for many years, and always found excuses not to start.
Then by accident I came across the ORIGAMI building method (more
on that later), and right away understood that that was completely
different from everything I had done before. I was flabbergasted
(always wanted an opportunity to place that word somewhere…)
and simply did not believe what I read. By the time I understood
better it was to late, I absolutely had to try this out myself,
and started making first sketches.
As I had become a bit wiser but not any richer over the years,
I wanted to design a boat that would allow me to start right away,
from next to nothing, and to be able to finish it, so to say,
from the running pocket money budget, but at the same time be
well capable of taking me almost anywhere in enough comfort to
live aboard for many months. So the first thing was that I reduced
the size to about 9 m, and the second was that I switched from
a modern rig with fully battened main to a traditional gaff rig.
At the same time I did not want to give up on the modern hull
shape and wanted absolutely to keep the daggerboards. The result
after some weeks of doodling and then more serious CAD work looked
like this:
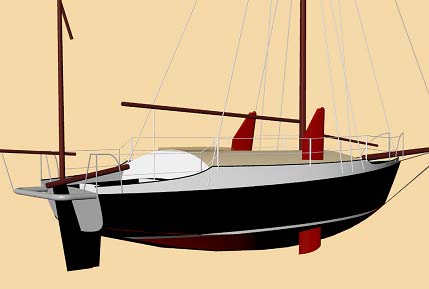
As you can see, YAGO has quite traditional topsides,
not really classic but let’s say what went for “modern”
in the forties and fifties. Together with the Rig this gives to
my eyes a pleasing look that does give no indication of what is
below the waterline. A more classic deck, with a coach roof could
also be designed of course.
The hull shape is a rounded chine hull (see below) where the
chines are under the waterline. There are 2 chines, plus a very
light central V. The hull has a very modern U section with nice
entry and fairly flat exit, all inside ballast and with the possibility
to lift both boards up when running a very low wetted area and
good speed potential.
The Daggerboards are a bit unusual today, but they have lots
of advantages. They are made from ply covered with glass-epoxy
and slide up through the deck. On longer tacks you would lift
the one to windward, but in confined areas you just leave them
both down. They can be lifted with simple block and tackle, they
can be removed easily for cleaning, they can even be switched
if one should be damaged, there are no axis or mechanisms to jam
or to maintain… and of course they let you beach your boat
and get into all the quiet moorings nobody else will get into.
YAGO is a gaff yawl. To be honest, the real reason is that I
just love the looks of it, although I have sailed smaller boats
with a similar rig and came to appreciate it. A cutter would fit
just as well and it would be no great thing to modify that. Otherwise
the obvious advantage of the gaff rig is that there is no expensive
hardware to buy, all can be made from raw material at low cost,
including the sails if need be.
With the steel construction and the home-made gaff rig and sail,
two major cost factors in a boat are taken care of. After that
it is very much a question of personal choices and preferences,
but YAGO can be a very low-budget blue-water sailor on the water
without ever looking cheap, and with a bit of love and patience
in fitting the insides and during the finishing stages should
be quite an eye catcher.
The full width cabin gives a lot of volume inside, and as the
steel hull will support itself without the need for structural
bulkheads, the layout can be freely designed as fits best for
your cruising program. I am still playing around with different
variations, here is just one simple example, pretty close to what
is today’s standard on this size of boat:
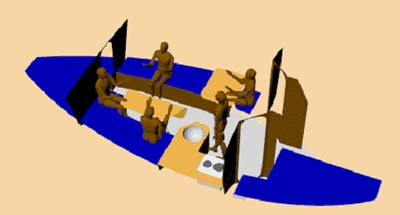
Origami
To make this clear right away, folded steel or “origami”
is not new and of course not mine. This particular type of folding
described here with darts from the center has been promoted notably
by BRENT SWAIN who has designed many boats that have made extensive
voyages over the past 2 decades. His book “Origami Boatbuilding
– a heretics guide”, plans for his boats from 26 to
40 feet, books and a bunch of very nice and helpful builders you
will find at:
https://groups.yahoo.com/group/origamiboats/
In conventional steel-boatbuilding you will first set up a heavy
solid jig, then build your frames and hang them, then put your
stringers on and so on and finally plate this structure with what
will be “the Hull”. Believe me, you will spend a lot
of time and cash just shopping and driving around and working
before you even touch the first piece of steel that will actually
remain in the hull.
In Origami the process is inverted, you will first build the
skin, and then simply insert the structure where necessary. To
do so you will cut a single shape per half-hull out of a flat
sheet of steel and then pull it together along the seams, a little
bit like in stitch & glue cosntruction, to produce a 3-dimensional
half-shell. These two halves are then joined along the centerline.
As a picture is worth more than…. Here is the shape for
YAGO:
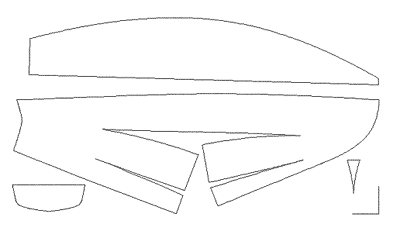
You can save the picture on your computer, scale
it up, print on paper and try it out yourself. The upper shape
is the theoretical , flat half deck, without camber, you need
this to define the sheerline.
Here is how to do it in steel:
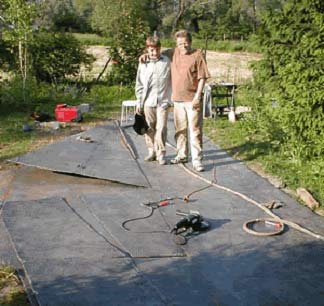
Cut the same shapes out of full size panels, flat
on the ground. Then start pulling them together:
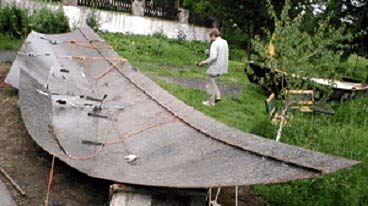
The pulling, although quite impressive, is very
easy, done with cheap $8 come-alongs.
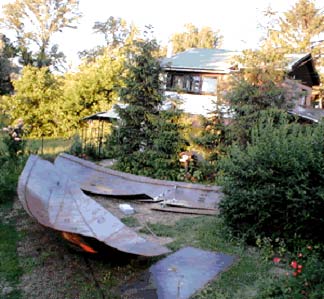
Here you can see the starboard half in front,
and in the background the port side coming together.
Once you have your 2 halves you simply join them
along the centerline and pull the hull together:
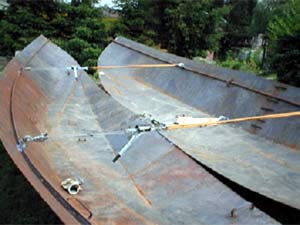
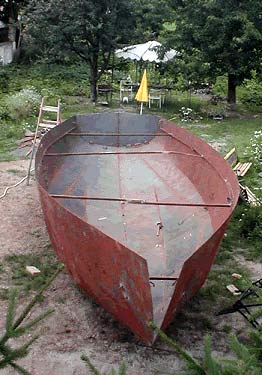
Compared to traditional construction this is incredibly
simple, cheap, surprisingly precise and most of all it is so FAST
the neighbours still haven’t noticed it yet ;-)
I have knocked the hull for Yago together in 8 working days over
a handful of weekends, under bad conditions and only with my 14
year old son, and I had to assemble the full size sheets first.
The total amount of money invested at this point is about 2000
US, half for steel and half for tools. If you can get single full
size sheets, the hull should come together in 3 days. If you have
ever built a steel boat, just think what you will NOT have to
do:
- No Scrap hunting for the jig
- No jig to build
- Frames fitted in later
- No turning of the hull
- Much less cutting, welding, grinding
- Not hard points during plating
- No lifting of plates as they are always
supported o the ground
And finally, you get a very sweet round shape that you simply
can not have with normal hard-chine construction.
The secret lies in the fact that the steel can take a “natural”
shape and tension, without being forced and welded to a rigid
structure. Because of the way the darts are cut, the hull will
produce rounded, compound sections for and aft, the chines will
only remain in the central part and under water. An Origami hull
in the water looks absolutely like a round-section hull.
In the picture below, you can easily see the foreward
end of the chine and the way the plating will bend into a compound
surface.
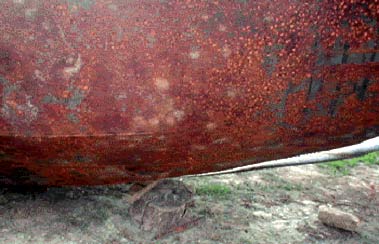
Once the hull is assembled, you add the deck,
which will define the sheerline.
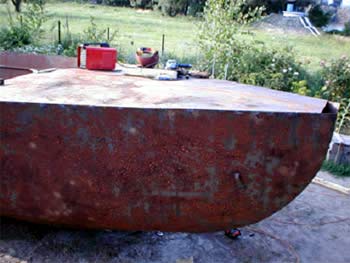
Only AFTER that you will go inside and add the structure
as required by the designer.
A note on “Frameless”: Origami is often described
as frameless steel construction. This is a bit misleading. What
it really means is that frames are not required for the assembly,
and you may freely place them afterwards for best efficiency,
and simply by cutting pieces of profile to size and fitting them
in. It does not mean that origami-boats automatically have no
frames, it just so happens that some designers like Brent Swain
design boats without frames, or with few frames, whereas YAGO
for example does have frames.
If you want to see more about the way you would design an origami
hull or to convert an existing hard-chine hull, the full CAD process
is described on my website:
https://www.justmueller.com/boats/
Distribution
There is not only the design process explained on
my site, there will be all the rest as well: YAGO 31 will be distributed
a bit like “open source” or “freeware”.
There will be all plans freely available. At this moment I am
working on a full building manual with pictures and drawings,
and the first part, for the hull, should be ready for download
September 2004.
Already now there are a few people gearing up to build their
own YAGOs, and I hope that over the winter 2004/5 this will begin
for real. There are requests for different layout, rigs, even
hulls.. I might not be able to do all that myself, but you know,
the more fools there are the funnier it gets.
For my own boat, I hope to be ready for sandblasting and painting
spring 2005, and in the water a year later, have quite a busy
professional life to attend to and working only over the weekends
and some odd hours in the evenings.
So, if it is so easy, fast and cheap to build such a nice boat,
and if even the plans are free for the taking, there is really
no excuse anymore NOT to start building your boat tomorrow –
so what are you waiting for?? ;-)
Gerd
https://www.justmueller.com/boats/

|