Fiberglass Resin
I’ve been considering building another boat
for quite a while now. I get out all my plans, and then I go
and research the Duckworks
Index to see what new ideas I come up with. I go
through a big analysis, and I always come back to one of three
designs:
Pocket Cruiser is light and small, easy to tow and store. That
would be nice. Bellhaven takes the qualities of Pocket Cruiser,
and adds a longer hull with an innovative centerboard/bilge
keel design to permit sailing right off the trailer, as long
as there is enough water that she’ll float. Allegra is
an awesome boat, but a big project while still holding down
a Real Job.
What always stops me in my tracks, though, is the cost/benefit
analysis. I enjoy building a boat, but the cost of marine plywood,
shipping to Colorado and epoxy leads to a big investment. The
fun is diminished by the fear that I’ll only be able to
get a small percentage of my money back when it comes time to
move to the coast and buy or build a big boat. It comes down
to a choice – do I do it right, and spend way too much
money, do I buy a used Catalina with its good resale, or do
I just bang some ACX together, slap some house paint on it,
and get on the water?
That last idea sounds good, until I walk out and look at the
Sharpie I built a few years ago. It sails great, and it is lots
of fun. Unfortunately, it looks like hell – the plywood
has “checking”. I don’t know if it would sell,
but I know I wouldn’t buy a boat that was split. I sometimes
wonder if I need to apologize to the world for inflicting an
ugly boat upon it.
I’ve plowed this ground several times, as I mentioned.
This time I noticed something different – Stevenson is
saying to laminate the plywood with FIBERGLASS RESIN. They are
crazy – don’t they know you can’t do that?
It won’t stick! Didn’t they see those catamarans
in the marinas back in the 70’s – the ones with
big sheets of fiberglass falling off of them? Then I read a
little more of the small print on their website – they
have sold 1/3 million sets of plans. I don’t know how
many sets of plans were sold for those ugly cement boats back
in the 60’s and 70’s – but it was a lot less
than 1/3 million before the word got out. If people are building
the way they suggest, and are happy with the result …
maybe this bears more investigation.
In my digging, I found a post by George Buehler on the subject.
You may not know George, but George builds and designs BIG,
STRONG boats. Like a seaplane hit one of his masts – the
plane didn’t fare too well, but the boat was fine. He
is a proponent of building something now, with what you can
get your hands on, and getting on the water. On his site (georgebuehler.com),
he quotes a man who worked on a project in 1958 where they fiberglassed
(epoxy not available yet) a 40-foot wooden hull. That’s
certainly a good-sized sample for a test. He saw the boat again
in 1975, and it was holding up fine.
So, I was going to do some testing. Put some glass/epoxy and
glass/resin samples together, maybe boil them. But, I don’t
sail in boiling water very often – like never. I got to
thinking – it has to be flexing that makes it come un-bonded.
I should make long thin samples, so that I can test them in
a flex mode, and see for myself how fiberglass bonds to wood.
Well, I was just getting ready to do that when I realized that
it has already been done. Did I mention that I live in Colorado?
I was describing skis! So I consulted the experts - K2. They
make skis, as do a whole bunch of other people. They are long,
thin strips of WOOD (for flexibility and shock absorption) wrapped
in FIBERGLASS. If you’ve skied much, you know what a beating
those things take. Every garage sale I go to has at least one
pair of old skis. Beat up, banged around, broken – never
seen a delaminated one. There it is on the K2 web site, as you
see below.
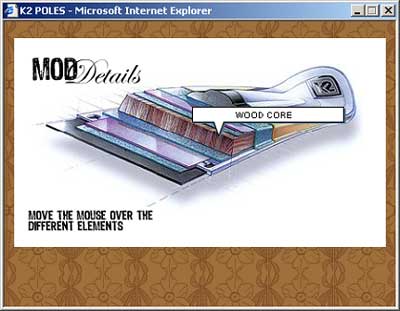
So, I read some of Stevenson’s FAQ’s. There it
is, the very question. They say it works. So I decided to write
them, and asked “are you still getting good feedback from
builders?” They replied that they are, and add that is
important to thoroughly wet out the plywood before adding the
glass, or absorption will make for a dry lay-up, and may not
bond.
And I think that clue may be what brings us full circle –
back to the marinas of the 60’s and 70’s. Back to
where we saw big old catamarans built of plywood, with fiberglass
falling off in sheets. What lesson could we draw from that –
don’t use plywood in a lay-up with fiberglass resin? Or,
could it be that poor craftsmanship, combined with a “build
it cheap” project mentality (resin costs money) popular
at that time doesn’t work with most materials, including
fiberglass and ferro-cement?
Then there is the whole question of plywood-cored decks. There
are a jillion of them out there, and they are still being built
today. Some have delaminated, but most haven’t. The difference?
What I read suggests that the ones that haven’t delaminated
have been maintained – which means keeping the penetrations
sealed so that water doesn’t get into the core. But, that
is a whole different article.
My conclusion: I think it might be worthwhile to give it a
try. I welcome the input of anyone who has EXPERIENCE with resin/fiberglass
on plywood, good or bad.
Thanks, BP <bill.prater@lpl.com>