In building and outfitting Skat,
I used brass and bronze hardware for rigging, mostly for a traditional
look, but also for ease of machining parts that I chose to build
rather than buy. The plans call for a one inch thick rudder
head, and bronze pintles and gudgeons in that size are more
expensive than what I believed appropriate for a relatively
cheap boat, so as with the blocks,
I decided to build my own rudder hardware.
For pintles and gudgeons, I based my design on an illustation
in H.H. Payson's Build the New Instant Boats. Payson
shows two L-shaped pintles on the rudder and transom connected
by a brass rod. I simplified the design some by making a single
C-shaped pintle for the rudder and for the transom. I used 1/8"
flat brass and 1/4" brass rod.
First, I cut two 1-inch wide strips of brass 12 inches long,
and drew a semicircle at each end.
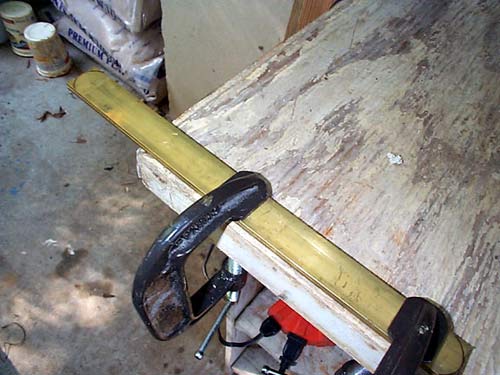
Then I cut both blanks at the same time using a jigsaw, a metal
cutting blade, and lots of cutting oil. I smoothed the cut ends
with a file and more cutting oil
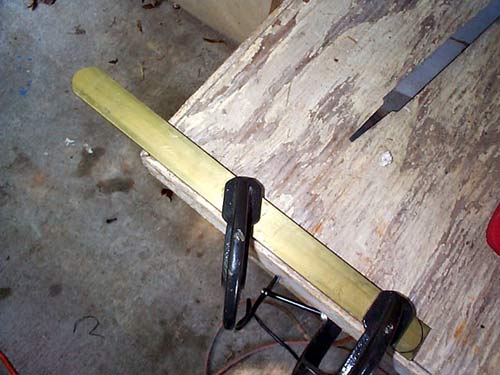
Then I took the blanks, drilled holes for the pintle at top
and bottom and 4 through-bolts to mount on the transom and 4
countersunk woodscrews for the rudder, and bent them side-by
side in a vise so that they would align when mounted on transom
and rudder. I wanted the rudder gudgeon to sit on top of the
transom gudgeon so that the weight of the rudder would be supported
by both ends of the gudgeon. I considered bending the rudder
gudgeon to fit inside the transom gudgeon so that it would not
bounce up and down, but I thought that such an arrangement would
be harder to mount.
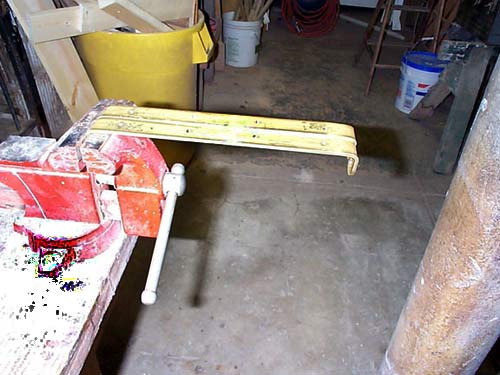
Next, I cut a pintle and pivot pins for the centerboard, tiller,
and kick-up rudder from 1/4" brass rod. I cut threads on the
pivot pins for 1/4" jam nuts. I drilled a small hole at the
bottom of the pintle for a hitch pin to keep the pintle from
coming loose while sailing (and sinking, leaving me rudderless)
and also to keep the rudder from bouncing up and down.
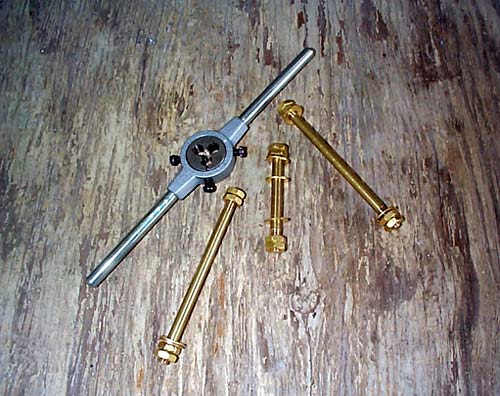
Next, I assembled the pintles and gudgeons (you can see the
hitch pin installed).
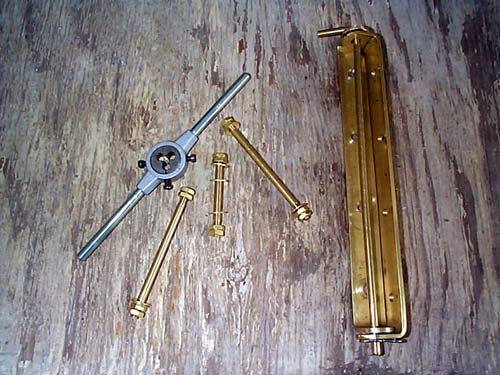
Finally, I mounted the gudgeons to the transom using 1/4" bolts
and to the centerborad using #12 wood screws. You can just see
in the photograph the edge of a small disk of PTFE I sandwiched
between the kick-up rudder and rudder head to allow for smoother
raising and lowering of the rudder.
I also had to come up with a system for raising lowering the
centerboard. My first idea was to set a sheave in the aft edge
of the centerboard case cover and mount another on the foreward
starboard corner of the cover. I could then run a line up from
the centerboards, over the aft sheave, around the forward sheave,
and back to a cleat on the aft starboard edge of the centerboard
case.
I decided that such a system was overly complicated, and instead
I just drilled a couple of holes through the centerboard for
a pin to hold it completely up and halfway down. I attached
a lanyard with a monkey's fist at the end to the aft edge of
the centerboard for raising and lowering. I bent a loop in a
piece of 1/4" brass rod for the holding pin, and I attached
it to the centerboard case cover at the sheave for the original
sheave.
If you look closely, you can also see that I have a lining of
3/16" HDPE inside the centerboard case. The idea was to lower
firction on the board when raising and lowering the board as
with the rudder and to minimize wear on the inside of the centoerboard
case (the centerboard is much easier to paint than the inside
of the case). I cut two pieces to fit inside the case and drilled
a hole through them for the centerboard pin, which also holds
the linings in place.
And last, I have added a garboard drain just aft of the centerboard
case to keep water from collecting in the boat while on the
trailer and to allow hosing out and cleaning the cockpit. Although
it is not exactly either centerboard or rudder hardware, it
is in the general vicinity of the centerboard case, so I;ve
included it here. I used a 2" Forstner bit to countersink the
flange on the plug, and then drilled the rest of the wat through
the hull with a 1" paddle bit. I painted the inside of the hole,
and then mounted the drain with #8 screws and lots of adhesive
caulk for bedding compound.
Tidmarsh Major
Tuscaloosa, Ala.
