Kick-up Rudders:
Problem and a Solution
by John
O'Neill
Problem:
Bolger Cartopper and many, many other "kick-up" type
rudders are held in the down position by rudder cheek friction
achieved via a sufficiently tight pivot bolt. The bolt needs a
fair amount of tension to prevent the rudder from creeping up
under sail (most rudders float!), resulting in a rudder that:
- Slowly creeps up and becomes hard to operate if there isn't
enough tension
- Won't kick-up easily at any time
Problem number one has caused me near capsizes downwind in stiff
breezes several times, and hard steering on any number of occasions.
It's also caused the loss of a good wrench, dropped in the drink
while trying to tighten the bolt.
Problem two has twice caused me to fully capsize in the mud-bottom
waters I sail. As those are the only two times I've fully capsized
my Cartopper, that's not a good record.
Each instance was downwind in a stiff breeze at low tide when
the rudder grabbed a (hidden) mudbank, stopping or slowing the
boat, causing the light boat to instantly and dramatically
slew sideways and careen wildly over. Sickening quantities of
muddy water then pour over the gunwale no matter what extreme
contortions I undertake to prevent it, causing angst, dismay,
wet drawers and loud, unconscious emanations from my vocal chords
- and that's the easy part.
Cartopper is an open boat; capsize is never a wholly fun situation
- even at the best of times. At the worst of times it can be downright
dangerous.
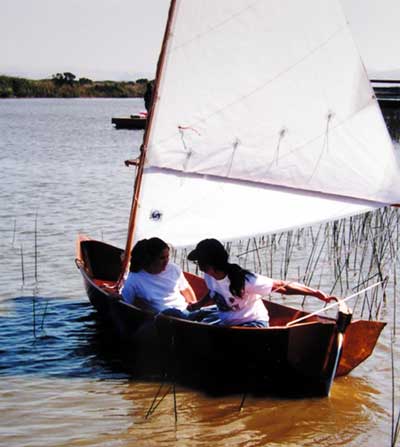
This Cartopper sailer is making lots of
leeway in the mud using a pre-modified, kick-up rudder - one that
ain't doing any kicking up . . .
Solution:
A spring-loaded ball-detent device that keeps the rudder down
until the spring pressure is overcome, allowing the rudder to
fully kick-up. (Ball detents can be had commercially, I have since
learned, but they are easy enough to scavenge together).
Basically my device is a short piece of threaded pipe capped
at both ends. The ‘inside' cap has a hole drilled through
it just slightly smaller than the diameter of a ball bearing.
The ball bearing (I used 9/16") is placed inside the pipe
and sticks through the cap hole, with a spring holding it firmly
in place. A second, closed cap is then screwed on the other end,
compressing the spring (and allowing for pressure adjustment by
varying how far it's screwed on).
A hole big enough to accept the inside cap is drilled through
one rudder cheek, in way of the edge of the rudder fin (for maximum
leverage). The ball detent assembly is mounted on that cheek,
with the inside cap (and thus the ball bearing) facing the pivoting
rudder.
On the rudder fin itself is mounted a metal plate with a hole
(large enough to accept the ball bearing) drilled through it,
and positioned so that the ball bearing fits in the hole when
the rudder is fully down.
The assembly holds the rudder down, firmly and positively, but
when sufficient force is applied to overcome the spring pressure,
up pops the rudder. (Tighten the pivot bolt just enough to keep
everything in place; no more is needed.)
To make it work there needs to be either enough space between
the rudder cheeks to allow for rudder, metal plate and ball, or,
lacking clearance, the plate is let into the rudder flush and
a groove is routed in the rudder to allow clearance for the ball
as the rudder is raised and lowered.
In practice I've found that when the rudder does kick-up, it
doesn't kick up enough to allow loss of all steerage. Instead
it bobs up and down floating high on the water but with enough
remaining submerged to allow directional control.
While I was at it (and thinking that it might come in handy during
the "sea trials" of my new ball detent device) I rigged
up a loop of line to raise and lower my rudder from inside the
boat. The line is rigged with a mechanical advantage purchase
on the "raise" side to more easily overcome the spring
pressure. I was concerned that I might have to rig the same on
the "lower" line, but in practice the momentum of a
quickly lowering rudder easily overcomes the spring pressure.
When the ball engages there is a loud, satisfying "clunk,"
letting you know that yes, the ball is engaged!
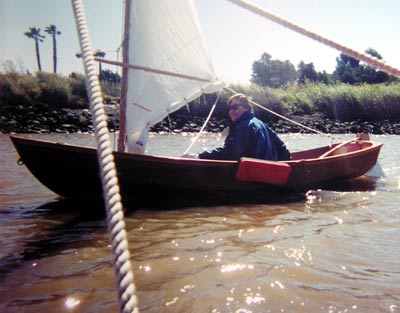
Reefed for a blustery day with a pre-modified,
kick-up rudder that's already kicking up - when it's not supposed
to! Later that same day, between a big gust, an unexpected jibe,
a helmsman inexperienced with the boat (my brother) and a rudder
not as responsive as it should have been, this brother and that
boat took a not-so-nice, unscheduled dunking. (Picture taken by
me, from my other Cartopper.) Personally I blame the entire incident
on his stubborn insistence on not bringing in that red fender,
"because it gets in the way." Well bro', you went and
spoiled the picture, and aren't paybacks a b----?
|