Skat Hardware: Blocks
by Tidmarsh Major
Though I haven't made a whole lot of visible progress
on the hull lately, I've been working on hardware in preparation
for rigging once I have the hull finished. First off, I've made
a number of blocks in anticipation of all the lines necessary
for a gaff rig. I used drawings in Edson I. Schock's How to
Build Small Boats, which contains plans for a catboat that Jim
Michalak used as a model when designing Skat.
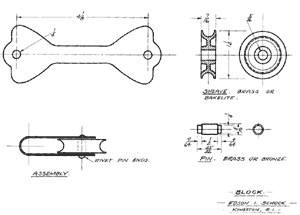
(click image to enlarge)
My first dilemma was determining what thickness
of brass to use for the body. The instructions called for "sign
brass" but didn't specify what that meant. After a discussion
on the Wooden
Boat forum, I decided to use .064 brass.
I'm fortunate enough to know someone who teaches
machine tool technology at a local community college, and he
used a CNC router to cut the bodies from my 12" x 12"
sheet of brass. He then bent them and drilled the holes for
the pins.
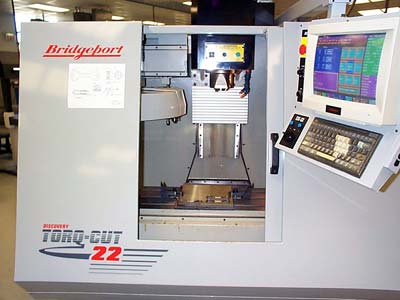
For sheaves, I bought a sheet of 1/2" UV-resistant
VHMW polyethylene. I used a 1 3/4" hole saw to cut sheaves
approximately 1 1/2" in diameter. I then chucked them into
a drill press and used a small half-round Microplane rasp to
cut grooves into them.
|
|
(click images above to
enlarge) |
Next,
I enlarged the holes to 5/16" and pressed in oil-impregnated
bronze bushings to fit a 1/4" shaft. Although to polyethylene
would have turned easily on a shaft by itself, I decided to
go with the extra durability of a self-lubricating bronze bushing
for this high-wear area.
Now came time to assemble the blocks. Rather than
turning pins as shown in the drawings and peening the ends,
I used partially threaded cap screws to allow for easier dissassembly
and repair.
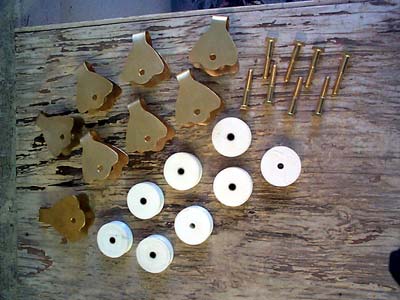
After assembly, I cut off the excess threads extending
beyond the two jam nuts (leaving one nut screwed onto the bolt
while cutting to clean the threads after cutting), and rounded
the ends with a file.
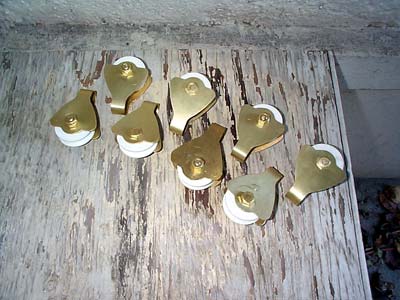
Though I was happy with my work, I realized that
while these blocks would be fine for the deck or the boom, I
didn't really want a pair of them tied to the masthead, swinging
around and banging up the finish on my mast. What I needed were
a couple of rope-stropped blocks. I searched on the web, and
found a few sources, including one article
here at Duckworks and one
from an old Mother Earth News.
Rather than use exotic woods, I used what I had
available: Douglas fir. For each shell, I cut two five-inch
long pieces of 1 x 2 . I then clamped them side by side and
used a handsaw and a chisel to carve a 2-inch long mortise in
the center of each half, 5/16" deep. Thus, when the halves
were assembled, I would have a mortised hole 2" long and
5/8" wide to fit the 1 1/2" diameter by 1/2"
thickness sheaves that I had previously turned. I then glued
and clamped clamped the two halves together using Titebond II
exterior wood glue. When the glue had dried, I then drilled
holes through the shells, 7/8" from the bottom of the sheave
mortise. The offset sheave leaves room for a 3/8" line
through the top of the shell.
I used a jig saw to round the ends of the blocks.
I had originally planned for a 2-inch mortise with 1 1/2"
inches glued area at the top and bottom, but the blocks looked
too long. I trimmed them down to a glued area of a 3/4"
radius at each end, for a total length of 3 1/2" rather
than 5", which looked better to my eye. I then used a Microplane
rasp to cut a groove around the shell for the rope grommet and
cut pieces of brass rod to fit the shells. I test assembled
with some 3/8" nylon line I've been practicing my splices
on, as I haven't ordered any polyester line yet.
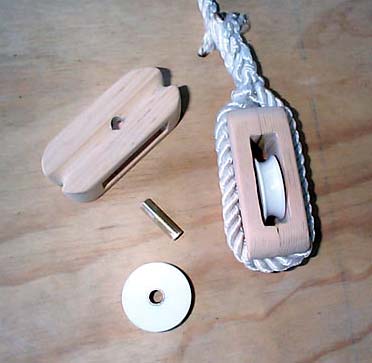
I'm now giving the shells a few coats of spar
urethane before final assembly. These wooden blocks weren't
hard to make, and I find shaping wood much more enjoyable than
metalwork. If I had it to do over, I'd probably make rope-stropped
blocks for all my rigging and skip the brass work. In particular,
if I didn't have access to a CNC router, I wouldn't make brass
blocks. For fun, I cut one brass shell freehand with a jigsaw
from the scraps left from the CNC router. Although it is functional,
it isn't anywhere near the level of finish achieved in the machine
shop. (See if you can spot the odd one out in the picture of
finished brass blocks.) I think my hand-carved wooden blocks
are far better looking than my hand-cut metal ones. As always,
though, your mileage may vary.
Tidmarsh Major
Tuscaloosa, Alabama
