When Things Go Right By Steven
Lewis This is the story
of an amateur designer, building a prototype boat, using techniques
that he has never used before, and getting the darned thing right
the first time around!
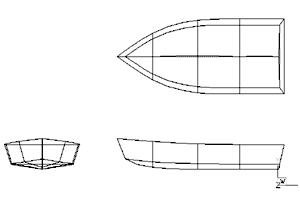
The design is Fisher10, a 10-ft
motor boat designed for fishing. The boat is a relatively simple
Stitch and glue skiff, with a mild Vee in the bottom. This is
the first Skiff that I had designed that I had attempted to build,
and also the first attempt at a Vee bottom. This is back in April
of 2002.
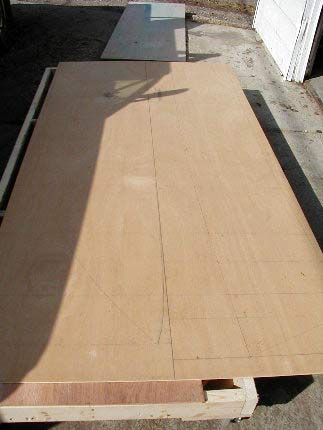
I started by marking and cutting
the panels for the bottom and sides butt joining the pieces to
the correct length. I then stitched the bottom panels together
and opened them up. Much to my surprise, I got the shape I was
looking for right off the bat. Encouraged by this initial success,
I started attaching the side panels and transom to the bottom.
After some precarious balancing, I was able to single handedly
stitch the sides to the bottom and the bows together and screw
the sides and bottom to the transom.
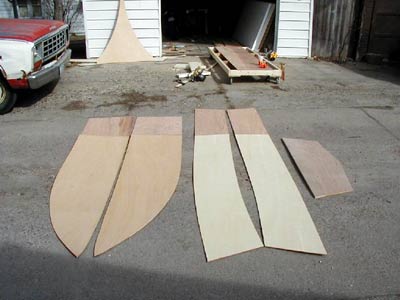
Filleting, taping and smoothing
went right by the numbers, with minimal problems. What surprised
me the most was how the boat, when the sides were spread to the
correct dimensions, looked exactly like it was supposed to. The
bows had the short, little hook upward that exactly matched the
design drawings. Things like this don’t usually happen to
me, at least not this easily!
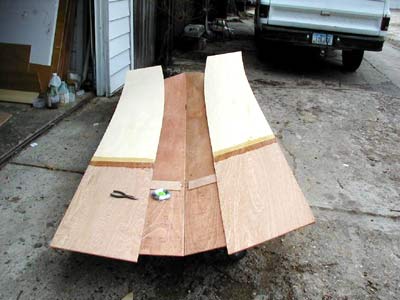
Using cut to fit methods, I installed
the seating, filleting and taping as I went. Round about this
time I had to do my 2 weeks Guard Summer Camp, so I took it with
me to work on as time allowed. I was able to complete the installation
of the seats, install the gunnels and seal interior. I launched
the boat in Lake Mitchell the Friday before the end of AT, using
a trolling motor to move it around.
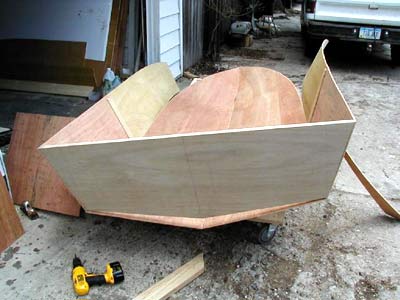
The boat languished in my building
garage for the next 12 months, until the 1st annual Iowa Messabout
at Spirit Lake, in northwestern Iowa. On the way up, the sturdiness
of the construction was severely tested, as the boat became airborne
and landed on the highway doing about 65. The result was some
minor scraping on the keel line and bottom of the transom as the
boat skidded along the pavement. A quick check of the boat, a
better system of attachment and we made it to the Messabout without
further incident.
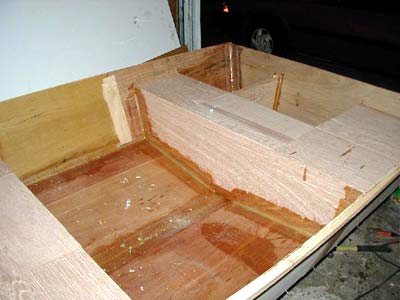
At the lake, the performance of
the boat was mostly as expected. With a 9.5 horsepower Johnson,
the boat comes up on plane with as much as 500 lbs. gross weight
although it takes a bit of time to get there. It is stable enough
to stand in and lean over the edge a bit, without feeling like
you are going to turn turtle. It pounds somewhat in chop, due
to the shallowness of the Vee, but weight in the front helps to
soften the ride. And no leaks as a result of it’s flying
lesson.
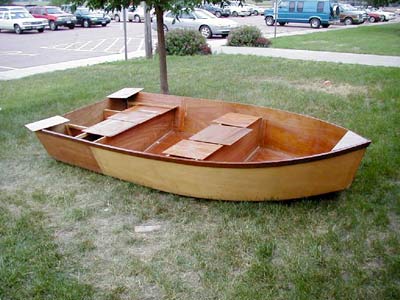
On the way back from the lake
however, things didn’t go quite as expected. The boat went
airborne again, but this time landed squarely on the transom-bottom
joint, abrading through the fiberglass and into the wood and landed
on the bottom, adding more scrapes and scratches. This was relatively
easy to patch up, with the repairs almost invisible. This was
all the damage done to the boat from two episodes that would have
turned most FRP boats into splinters, and loosened the rivets
or ripped the skin on the Aluminum ones! This, more than anything
else, has convinced me of the soundness of building by Stitch
and Glue. I may use other techniques in the future, but if I want
a truly bulletproof boat, S&G is the way I’ll go….
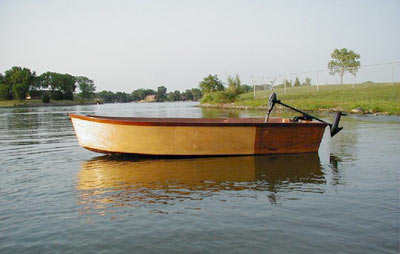
I’m sure this little boat
and I will be seeing a lot more water together, and have a many
more stories to tell in the future.

For anyone interested
in building Fisher10, plans and a fairly detailed pictorial
build sequence are on my web
page: and here
at Duckworks Magazine. The plans are free for anyone to use
and are in the form of offsets for the panel dimensions. With
the offsets and using the pictures as a visual guide, a person
could build the boat in about 2-3 weeks working 1-2 hours per
day.
|