Unhappy is the amateur boat
builder that completes the hull, orders the sails and then
discovers the price of blocks. Even single blocks, with simple
sheave bearing cost $5 - $15, and more complex bearings will
empty your wallet.
But for light rigs, blocks
are simple to make, and look 100 times better than stainless
steel and plastic. You need, appropriate size acetyl sheaves,
hardwood, (elm, oak, maple) either stainless steel bolts or
rod as sheave shaft.
In the illustrations below,
the sheaves are 32 mm (1¼ inch) diameter, bored to
6.4 mm (¼ inch). For strength and proportion the long
axis of the block should be about 1.5 times the maximum width
(sheave diameter) , so in this case a block length of 50 mm
(2 inch) is about right.
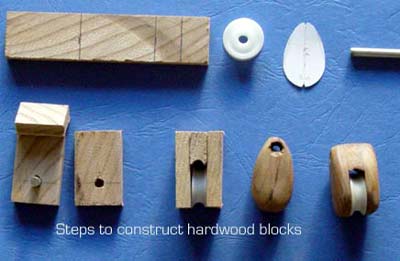
1. Choose quarter sawn wood
if feasible; the grain should run parallel with the cheek
faces.
2. Cut a 130 x 32 mm (2½
x 1¼ inch) strip of hardwood about 1 mm thicker than
the sheave (10 mm; 3/8 inch) ensuring the sides are parallel
and square.
3. Cut into three pieces –
two cheeks 50 mm longer, and a spacer piece 20 x 32 mm. The
smallest piece acts as a spacer. The spacer grain should run
at right angles to the cheek pieces.
4. File a groove with a round
file in the long axis of the spacer piece
5. Measure and mark centre
lines and ½ sheave diameter (16 mm) up from bottom
of the two long pieces.
6. Centre punch, and then
drill pilot holes, then 6.5 mm holes to 6 mm depth (¼
inch) holes or to fit the shaft. Use masking tape to indicate
the depth on the drill. Don’t guess.
7. Cut the shaft (from bolt
or rod) 10 mm over size (5 mm into each cheek).
8. Mark the glue line on both
inside surfaces of the cheeks and dry assemble to check the
cheeks lie parallel, and the sheave rotates easily when clamped.
9. I spray the sheave with
silicon to ensure it won’t stick to excess glue. Candle
wax will also do the job.
10. Make up about one ml of
epoxy resin; before you add the glue fiber, put a drop of
resin into each shaft hole. This will seal the wood fibers
and glue the shaft. Add the fiber, spread the glue on mating
surfaces and clamp overnight.
11. Make a template from light
card. Tip: Measure out a rectangle (32 x 50 mm) mark the centre
line, shaft position (+16 mm from the bottom) and the spacer
position (- 20 mm from the top); cut two notches top and bottom,
draw a smooth curve on one side to produce a pear shape, fold
in half and cut both sides together. That way you end up with
a symmetrical shape that can be centered on the long axis
of the blanks.
12. Drill a 6 mm hole through
the top of the blank. Tip. Centre punch, then drill pilot
holes from both sides before committing to the full size bit.
13. Mark the shape on the
blank, cut, file and sand to shape. I use a fine Japanese
saw followed by a belt sander with 60 grit to get to rough
shape, working up through the grades to 240 and sand smooth.
14. Finish as you will: I
soak the blocks in 50% Danish oil ( or linseed) : mineral
turpentine for a couple of hours followed by two or three
coats of neat Danish or Teak oil to finish
The blocks cost about NZD $4.00 or what ever the sheaves
cost in your currency and with a mass production set up I
make four in an hour. The blocks look better than stainless
steel, and are quite strong enough for standard use. If you
wish to make larger or stronger blocks you can reinforce the
cheeks by using hidden pins or through bolting through the
spacer.
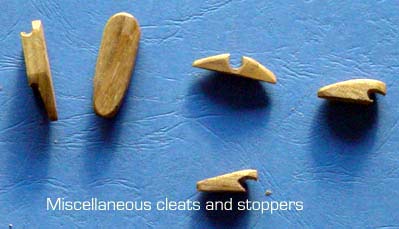