Are We Still Inventing the Wheel?
by Jim Betts
Oakum, tar and the caulking iron are about gone,
but for use in a few replications of historic ships. The square-rigger
gave way to the fore-and-aft sail rigs. The heavy "ice-breaker"
boat has been refined by new materials and methods and has
become today's lighter, stronger, faster and easier and cheaper
to build.
In the amateur-buildable area, some things came
and went. Some things - notably plywood - came and stayed.
There was the "sock boat," which was a kit of corrugated
board used as a building form. These were put up on a jig
and stringers were installed. Then you had a "sock"
of stretchy fabric that you pulled over this. Then you fiberglassed
it. Sounded good, but the sock was not rigid enough and so
you got boat with a "starved-dog" look. (Where the
ribs show.) Then there was the balloon boat. You blew it up
and fiberglassed it. (A letter to them came back "Deceased."
I wonder how.)
Do It Yourself - Because We've Done it
Then there was the kit boat guaranteed to go
together because it has been together. The company built the
boat and then took it apart and shipped the parts to you.
Hell, why not just send the boat?
Then there was the paper boat. The idea was
to use old newspapers and glue to laminate the boat. But it
takes 48 sheets of newspaper to make a hull 1/4 in. thick.
That's a lot of copies of the New York Times Sunday edition!
There is current experimentation using ordinary
cloth (like bedsheets) to build a boat rather than more expensive
fiberglass. (We'll report on this fairly soon.)
Blow Up Your Own Boat - Wear Ear Plugs!
An outfit in Germany proposed an "exploded
boat." They would build a strong steel mold, line it
with sheet aluminum and set off a few sticks of dynamite.
The heat and pressure would blow the boat together. (Wait
until OSHA hears about this one!)
A recent National Geographic story showed how
- in some parts of the world - they makes boats of reeds bundled
together. But reeds do absorb water in time, so you have to
build a new boat about every month.
And there is rotomolding. You put plastic material
into a heated metal mold and spin it around. The plastic melts
and forms a boat. Actually, this works well and is a growing
area, but for obvious reasons, such as mold costs, is limited
to small boats.
Stitch-and-glue (sew-and-go, etc.) is a bit
old now, but some improved techniques are being tried here
and there. One interesting trend is the increasing number
of designs to use the method, especially with fewer stitches.
And there is more work being done on how this can apply to
larger boats. More on this in future issues.
New Technology is Making Boat Building Easier
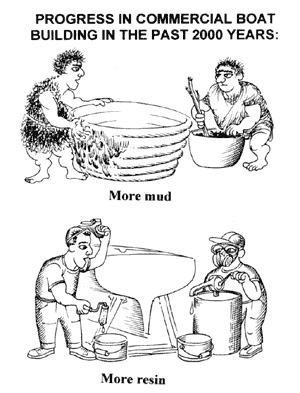
Old-style boats (call them "traditional")
now benefit from new technology, lain Oughtred, a member and
designer living in Scotland, does very nice lapstrake (clinker)
boats, but he uses epoxy rather than the metal fasteners as
in the past. (See story) Using this modern method, the amateur
builder can have the best of both worlds, the beauty of traditional
boats and the benefit of modern methods. Building is faster,
cheaper, easier and overall better.
R&D is Needed at Pro and Amateur Levels
I have played with the idea of a houseboat built
on plastic dock floats. Too expensive. And concrete sewer
pipes. Too heavy. And PVC pipes. Too flexible. How about aluminum
boats stuck together with Sikaflex or similar "super
glues" rather than welded or riveted? (I'm working on
this and if you don't hear from me you'll know it didn't work.)
What next? I'm sure there are better materials,
better designs and better methods out there. We (and you)
need to explore the possibilities. I am certain the members
of IABBS can do it. The membership already includes experienced
boat builders, engineers, scientists and new-product-development
people. Think new and different! And do let me hear from you.
You may not have the answer, but you may be able to better
state the problem.
Jim Betts
