Plywood
At the end of a street in a coastal suburb there sits a modest
building. An observer glancing through a window would behold
a scene of cheerful industry, complete with the competing sounds
of power tools, recorded music, occasional laughter, and frustrated
cursing (usually directed at the telephone).
Closer inspection would reveal five small craft under construction,
along with a handful of repair jobs, spars, rudders and centerboards.
If the watcher were astute, he or she would notice that although
the boats are of differing design, there is a common thread
– timber, epoxy, modest size, and traditional design.
The owner of the workshop tends to talk too much, but that
is because he is passionate about small craft, and he is keen
to encourage amateur construction. He believes that the most
common impediment to successful amateur boatbuilding is not
lack of space, nor is it shortage of money. He thinks that lack
of confidence is the reason that the majority of projects remain
unfinished, or are never even commenced.
Wandering through the workshop, the visitor will discover that
many different forms of construction are compatible with the
most commonly used materials. For example, each of the boats
on the floor is being built differently – glued-lapstrake
(clinker), strip-planking overlaid with double-diagonal ply,
conventional stringer/frame, stitch-and-glue, and lapstrake
ply in the dory form.
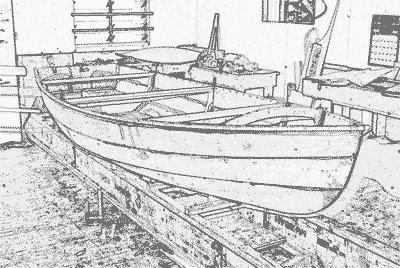
All of these building methods are suitable for the amateur
working with a minimum of equipment, and with limited windows
of working time. Admittedly, some of these methods are more
complex than others, but all are within the realm of anyone
who is willing to pay attention to detail, and to do the required
homework.
Today’s builder has access to enormous reserves of information,
and high-quality building materials are easy to obtain.
There is a commonly held belief that marine plywood is somehow
inferior to natural plank stock, and that plywood boats are
not the genuine article. A recent repair job demonstrated the
error in this line of thought.
The boat in question was a beautifully built lapstrake (clinker)
pulling boat of the Whitehall style. The planking was all of
high-quality marine plywood, the plank laps having been glued
with marine epoxy. As is normal with such construction, no bent
frames or ribs were required, but she did have two small half-bulkheads
fore and aft enclosing buoyancy tanks.
She had been hooked up on a pylon while slung in davits at
the stern of a very large motor-sailer. As a result, she had
suffered serious damage to her starboard side – the gunwale,
clamp (or inwale), two planks and a laminated knee were all
smashed, and absent from the boat. There was also damage to
the planking on the port side, where a pad-eye had torn out
a section of the sheer plank.
Amazingly, the remaining hull had retained its shape, and it
was possible to carry out an economic, and complete, repair.
Had this boat been built using natural timber planking, she
would have been framed with dozens of bent ribs, floor timbers,
and knees. The plank laps could not have been glued, and would
have needed copper rivets or clench-nails.
I doubt whether a boat in this traditional way could have survived
the same accident without loss of hull shape, and she would
probably suffered terminal damage.
Ironically, the only parts of the repaired boat which remained
doubtful were the fine copper clench-nails which had presumably
been used to hold the laps during construction while the epoxy
cured. Throughout the boat, there was evidence of paint cracking
around these fastenings, and a subsequent path for water entry
to the end grain of the planking. During examination of the
damaged planking prior to repair, I was able to determine that
the nails had added little or nothing to the damage resistance
of the glued lapstrake construction.
Don’t try to save money by using exterior or structural
plywood. The glue-line may be the same as that in marine ply,
but nothing else is equal. The relevant standards for marine
plywood (AS/NZ 2272 and BS 1088) specify allowable timber species,
veneer tolerances, allowable defects and finish levels. As a
result, the use of marine plywood will produce a stronger, longer-lasting
and fairer boat. The money saved by using inferior grades of
plywood amounts to a tiny fraction of the time and money invested
in the boat.
Not all marine plywood is created equal. Some imported BS 1088
marine ply is of inferior construction, and suffers from wide
variations in timber density. In my limited experience, I can
thoroughly recommend all of the Australian Hoop Pine marine
plywood (e.g.; Brims, Austral, Boral etc) made to AS/NZ 2272.
Of the imported Pacific Maple marine plywood, Wayang Brand is
of consistently high quality, and represents unbelievable value
for money. Other brands can be good, but shop with great care.