As part of some ongoing work
on some local housing projects, I happened to be in Orange Walk
Town in northern Belize in September 1999 when the first annual
New River canoe race was held. Seeing the first boats come around
the bend to the finish, I knew I'd have to build a boat and run
in the second annual New River canoe race.
A little inquiry revealed that
the race is 'about' 40 miles long and the rules were simple, 3
man boat 19' maximum length. The rules were a little more restrictive
than the Texas
Water Safari, for which I had designed and helped
build several competitive boats over the years (Safari rules,
human power only, period). On the other side of the coin, 40 really
flat-water miles is a lot easier than 260 miles of really varied
and rough river conditions.
My client and host, Mr. Joe Loskot,
owner of New River Enterprises, a local lumber mill and manufacturing
concern, readily agreed to furnish the lumber for the boat and
a space to work and I would provide the rest (design, glass/epoxy,
experience, etc.). Sergio Barraza, one of Mr. Loskot's employees,
agreed to help paddle the boat and would find a third man locally
to complete the team. Sergio suggested the boat be named "Miss
Lavi" after Mr. Loskot’s youngest daughter (and Sergio's
future fiancee). The only thing left was to break the news to
my wife that I was going to build 'another boat' and that it would
interfere with our planned working vacation trip to Belize.
Two days later, back in Houston,
Susie understood my compulsion to build another boat and
we would work our schedule around the boat building (thank
God for understanding and indulgent wives). The design was
done (see sidebar1).
Materials ordered. Twelve yards of 60" wide "s"
glass (ouch) and a gallon of Maas epoxy and a half gallon
of tropical hardener and appropriate hand pumps. The extra
expense of the "s" glass (3x) was rationalized
on the basis that the effort going into a project justified
the extra cost for such a relatively small increase in physical
properties. And the "s" glass really is easier
to work with and wet out. I hadn't used the Maas epoxy system
before, but it was the 2:1 ratio type that I much prefer
and the hardener was classified as non-corrosive, so shipping
would not be a problem.
Shipping was a problem, too
much stuff. Take 3 people (wife, mother-in-law and me),
travel gear for three weeks, including some snorkeling gear
and add the stuff to build a boat. A real load to get to
the airport. We made it, but I got stuck in the doorway
at Houston intercontinental with a five and a half foot
long piece of 4" PVC pipe strapped to my back, wheeling
two 48 quart igloo ice chests and other sundry stuff in
front of me. Nine pieces checked, plus 3 carry-ons. The
boat building stuff actually only took up 2 pieces of luggage
a 48 quart igloo ice chest and a five foot plus long piece
of PVC pipe (see sidebar2).
Dairy of a boat building:
Monday, 8 November, 1999
Flight to Belize, met at airport
by New River staff member, who was also picking up some large
crates of sawmill blades. We all fit in the vehicle, but I rode
the 60 miles to Orange Walk in a cross legged Yoga position since
the passengers floor boards was full of baggage. Got settled in
a bit, It rained all day.
Tuesday, 9 November 1999
It rained all day. Got started
with the set-up. I was given a spot to work in a new building
under construction that will be used for some of the products
in the new housing projects. 110 volt power available, but
no compressed air, oops. To work, New Rivers construction
grade plywood interesting in that it is much lighter than
what is available in the U.S. and has virtually no knots
or voids in any of the veneers and the veneers are equal
thickness. One sheet of ¾” ripped into 5-7”
x 8’ strips for the strong back plus the remainder
in 1½” strips for frame bracing. One sheet
of ¼” crosscut into 8-4’ x 1’ panels
for strong back web. 2 sheets ¼” cut into 16”
wide strips. All this plywood was cut in the mill and I
carried it out to the new ‘boat shop’. In a
hurry to get started, I took a shortcut across the yard
carrying the ice (tool) chest and promptly stepped in a
thigh deep rut full of water and muck. At least it entertained
a few workers.
Back on more or less dry
ground, cut up and butt block the ¾” ply into
a 7” x 18’ & 7”x 16’ piece with
5- 7” x 10½” spacers. Assemble ladder
style on side and then straighten along the 18’ side
to a string line. Nail & glue the ¼” web
pieces on that side. Roll over and clamp a few (3) pieces
of ¾” x 1½” x 24” strips
along the 18’ side and check for twist. Shim as required
so that the top relatively planar (no twist), nail and glue
¼” web pieces in place. While glue is drying,
cut out frames.
Glue ½ pattern print
on piece of poster board. Cut out around outline of largest
frame. Trace around pattern with pencil, being sure to mark
the centerline and the sheer. Flip pattern over; trace the
other half, once again marking the sheer location and the
pattern number. Cut out around the next station with scissors
and repeat. I usually mark one section of plywood and then
cut out the patterns with a jigsaw. Repeat until all frames
are cut out. Fasten frames to 1½” wide plywood
strips cut 2” or so shorter than the frame width,
be sure to fasten on the side opposite the centerline and
sheer marks.
Mark centerline on strong back
with stretch string and spray paint. Mark frame stations and square
across top of strong back. Put some legs under strong back to
get to a convenient working height. Finally, some 3 dimensionality,
start at the midsection and fasten frames to strong back, one
screw @ the center of the ¾” plywood strip and then
nail at one edge of strong back top to square.
Got the front frames set up; enough
for one day, go get cleaned up.
That evening, Sergio proposed to
Miss Lavi, will have to work fast before the boat name has to
be changed to Mrs. Barraza.
Wednesday, 10 November
1999
It rained all day. Worked in office
all morning. Had lunch with Mr. Loskot. In the afternoon,
met Edwin, who was to be my assistant in building the boat.
We finished setting up the rear frames. The first Spanish
cedar strips were cut and machined for bead and cove with
the MLCS bits that had been sent down earlier with some
drawings. The strips look really good; kiln dried material,
tight even grain, light and strong, I could have used ‘e’
glass. I had Edwin cut up the 4” PVC pipe in 1¼”
wide rings and then slit them for clamps. Holes drilled
about 3” apart and 3” in from the edge of the
frames for rubber band cleats. Cover edges of frames with
clear packing tape.
Thursday, 11 November 1999
It rained all day, not quite
so hard. Begin stripping. The longest strips are about 14’
long, so Edwin and I are cutting 3:1 scarfs by hand, holding
2 strips together on a scrap piece of plywood. The first
strips are strapped on, radius side up, against the small
nails tacked in the forms at the pencil marks on forms.
The ends are bevel cut and glued together. The second strip
is installed, glue run down the groove and then strapped
down. Stop for a minute and make sure everything is fair
and square, take a picture it’s the first time in
3 days the rain has let up enough to take a picture. Things
go pretty well and we are able to get the hull stripped
up to the turn of the bilge, so things can dry overnight
and we’ll tackle the tough part in the morning.
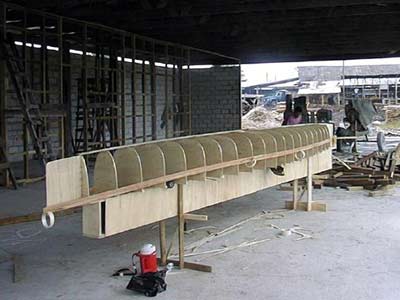
Friday, 12 November 1999
No rain today! Keep on stripping,
the sweep up at the bow really helped fit in the strips
at the ‘chin’ of the bow. Small wedges cut from
scrap plywood help hold the strips in tight where they twist
from horizontal in the middle of the boat to vertical at
the ends. Once stripping gets into the bottom of the boat,
we start doing a zigzag cut down the centerline of the boat.
Edwin starts filling gaps and holes with putty while I fit
the last stealer pieces in the bottom.
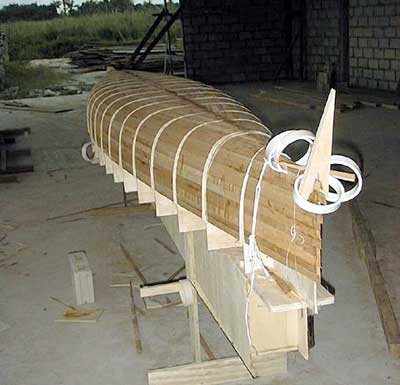
Saturday, 13 November 1999
No more rain. There is still
no compressed air available, so I borrow a belt sander with
a 60 grit and 100 grit belts and get to work. Cut loose
the rubber bands at the gunnel and pull out the bands, over
a thousand but it goes quick. Start sanding in the middle
of the boat to let the ends have more time to dry. Sanding
takes all day and I’m pleasantly surprised that I
can still move my arms without pain, since I hadn’t
used a really heavy belt sander in a long time.
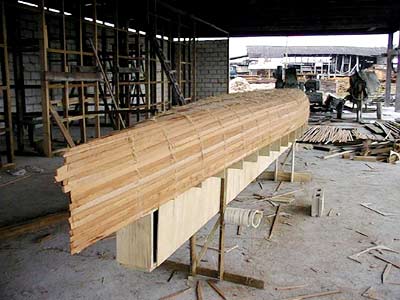
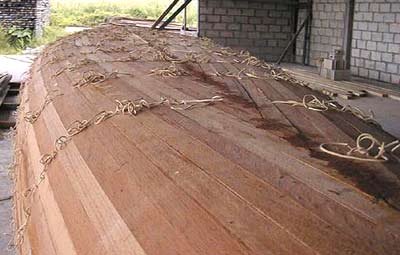
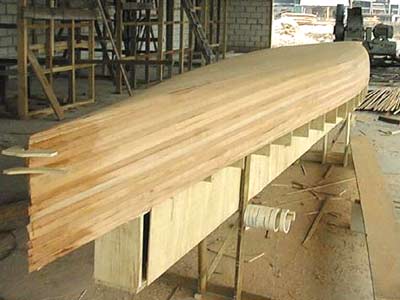
Sunday, 14 November 1999
Glassing day, Sergio has
offered to help after he takes care of some other things,
so we plan on starting about 1:00 PM. I get to the mill
a little earlier and get set up. When Sergio gets there,
we roll the glass out over the boat and cut to length and
trim around the edges. I had made iron-on stickers for the
boat name and little circular vignette portrait of Miss
Lavi to
put on the bow. In my haste to get on with the glassing
I tacked all the stickers in place, then ironed them on.
Oops! Iron ons should be done one at a time, removing the
backing while everything is still hot. Lost the portraits,
but salvaged the boat names. Start mixing epoxy, 6-oz resin,
and 3-oz hardener to start, so Sergio can get a feel for
wetting out the cloth and the process of working out from
the middle always working towards the ends. Start to use
larger batches, 9-oz resin, 4-½ oz hardener, battery
gives out on cordless drill, we start mixing batches by
hand. I really should have taken Susie up on her offer to
help mix, it’s a three ring circus with only two performers.
In any case, we get the glass wet out and the ends trimmed,
glass lapped etc, its starting to get dark, we don’t
have any lights and I haven’t even got the peel-ply
out. Usually I cut the peel-ply in 8 to 12 inch wide strips
and lay them across the hull starting in the middle. In
the interest of time, we put the peel-ply on in one piece
draping it over the hull and then starting to smooth it
out starting in the middle and working out to the ends.
In the haste to get everything wet out, there isn’t
quite enough resin on the glass to soak up into the peel-ply
so we mix more epoxy and squeegee it down through the peel-ply
to smooth out the finish of the glass. It is dark and we
are done.
Monday, 15 November 1999
I stop by the mill just long
enough to peel the peel-ply off the boat. Since we had squeegeed
the epoxy through the peel-ply, it is stuck harder than
usual, so I end up peeling it back in about 3” strips.
Off on real vacation far from the beaten path with Susie
and her Mom.
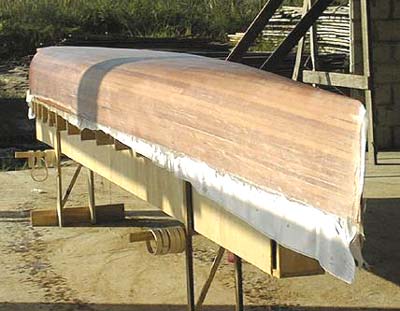
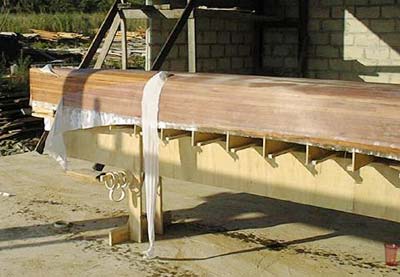
Tuesday, 16 November 1999
Backcountry
Wednesday, 17 November
1999
Backcountry
Thursday, 18 November 1999
Back
at mill, disaster of my own making. I had coated the hull
with a thin coat of epoxy to fill the texture left by the
peelply and was in a hurry for it to kick off so I could
take the hull off the forms. It was subtropical but not
that hot so I started moving the form out into the sun so
the epoxy would cure quicker. In the process of see sawing
the form out into the sun, one of the legs broke and the
whole thing fell over upside down on the concrete. I was
sick and really ticked off at myself for getting in a hurry
and not getting any help to move the boat. Some of the mill
workers came over immediately and helped get the boat back
upright and the legs re-braced. Then I squeegeed off most
of the fresh epoxy and most of the bits of concrete, dirt,
dust and other junk stuck to the bottom of the hull. Also
set back up the hardener container I kicked over while running
in tight circles. After I cooled off and the epoxy that
was left on the hull cured a bit, I took the boat off the
form. Enough for one day.
Friday, 19 November 1999
National Holiday, went to Key Caulker.
Left Susie and her Mom for a couple of days
Saturday,
20 November 1999
Back batchin' it a couple
of days, work fast. Move the boat over to the main mill
work area to be close to compressed air that oops, doesn’t
work. Start sanding out bottom with belt sander and mill
foreman goes off to junk yard and finds a piece of scrap
pipe than can be brazed into line to fix compressor. Now
I can use the D/A sander. Sand. Sand. Sand. Quit.
Sunday, 21 November 1999
Glass inside of boat, do I always
glass on Sunday? Don’t think so, don’t really
know. A little more relaxed, start earlier and do the glass
in 5 foot long sections with fiberglass running across boat.
Also scarf the 5/8” x 1¼” mahogany gunnels.
Good clean 6/1 scarfs this time because we don’t want
hard spots in the sheer.
Monday, 22 November 1999
Install bulkheads fore and aft,
cut out of local ¼” construction (exterior)
plywood. Use epoxy wood flour fillets using the last of
epoxy and wood dust (flour) from the mill shop sander. Glue
on the gunnel strips using the absolutely very last drops
of epoxy (had kicked over the hardener jug back when I dropped
the boat and lost about 20% of hardener). Cut open the jug
and disassemble the pump last bit of hardener, had plenty
of resin left. The picture shows the gunnels clamped on
with the pvc clamps cut from carrying tube. ‘Fishscales’
in picture (thought my digital camera was broke and only
saved one picture of bunch) were due to electrical noise
from the diesel generator that runs when the sawmill is
operating. Local power grid can’t reliably supply
power.
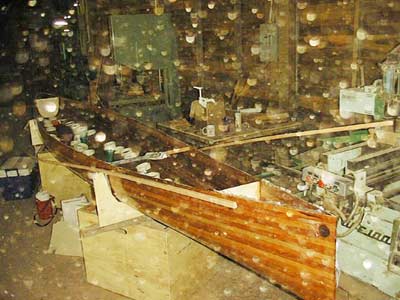
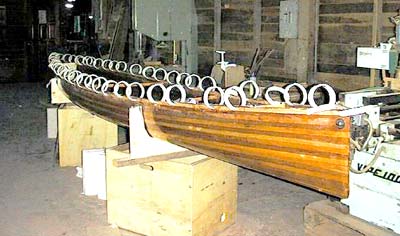
Tuesday, 23 November 1999
Returned to Cay Caulker and rescued
Susie and her Mom, though they didn’t seem to appreciate
being rescued.
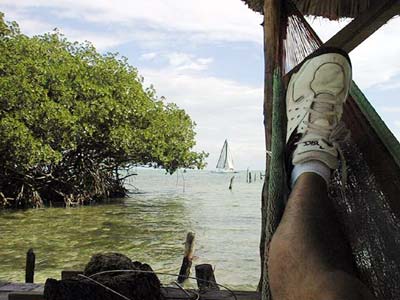
Wednesday, 24 November
1999
Generally clean up mess and get
ready to fly back to Houston. Lots of little odds and ends to
take care of plus packing. Took a few pictures of boat with Edwin
who had helped with building boat. Edwin didn’t have any
experience with boat building but really knew how to work with
wood and was a willing and able assistant.
Thursday, 25 November 1999
Fly back to Houston today, but
can’t stand not trying boat out. We go down to the
cut to the river that they used to float logs down many
years ago and put the boat in. The paddle is a piece of
scrap with construction plywood blades nailed to it, which
is enough. The boat handles well with one paddler, accelerating
and turning much better than I expected primarily because
the ends are just out of the water.
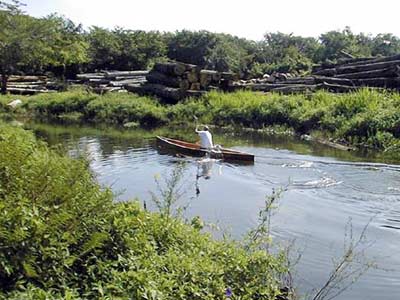
Fast Forward
Wednesday, 13 September
2000
Back to Belize. This time solo,
with 3 take-a-part paddles, 3 water jugs, lifejacket, my custom
fitted seat cushion , some extra foam and misc. stuff. Plenty
of epoxy now, had sent 2 gals resin and gallon hardener (Fiberglass
Coatings) along with a shipment of parts and supplies for New
river Enterprises.
Thursday, 14 September
2000
Cut and fit in decks, cut
and fit in three seat platforms from ½” construction
plywood. Seat platforms ‘U’ shaped with foot
braces bolted across legs of ‘U’. Quick and
simple. Glue in thwarts. (picture) Mill finishing guru stains
decks to match mahogany gunnels.

Friday, 15 September 2000
We are generally picking up the
last little details and getting ready for some practice paddling
and the race organizer drops by mill. Effusive and heartfelt compliments
“ thought I was too old, but I’m in love again”.
Then, “Oh no, it is a canoe race, you can not use kayak
paddles”. Arrgghh!! I don’t even own a canoe paddle.
We spend some time fitting quick and dirty handles to the two
wood take-a-part paddles I’d brought so we would have something
to paddle with.
Saturday, 16 September
2000
We carry the boat down to the river
and practice a bit. About 6 miles upstream to the sugar mill and
then back. Boat handles good, but I feel pretty inadequate trying
to instruct Sergio and his friend in any of the finer points of
single blade paddling because I just don’t have the experience
or expertise. My kingdom for a double blade.
Sunday, 17 September 2000
Race day. All the boat meet at
the fire station and we caravan to Lamanai, Mayan ruins
on a large lagoon near the headwaters of New River. The
boat is strapped to the top of Mr. Loskot’s Land Cruiser
and there’s an oval trail of drool marks around the
vehicle as everybody checks out the new boat. Unfortunately
some of that drool comes from some pretty fit looking fellows.
We caravan to Lamanai (sunken crocodile) 19 boats no two
alike, but the majority are aluminum or fiberglass standard
doubles style boats. A line is stretched from a floating
dock out across the opening of the lagoon and we are all
lined up along it for the start. The gun sounds and we are
off. Most of the boats are off in an explosion of spray
and wakes, but it is 40 miles to the finish and we stay
toward the back of the pack.
About a third the way through
the race and a few boats have dropped out and we’ve
passed a few but there are more ahead of us and beyond the
next bend so we have to set our own pace and paddle, paddle.
Beautiful, tropical country, no spectators at all except
at Shipyard, a Mennonite community just before halfway and
then at Orange Walk Town. Water is still and clear no current
to speak of. No hazards at all except the heat, broken by
showers two-thirds through the race, and the few occasions
when the race committee boat came upon us around a blind
bend. In any event we do the best we can and come in 6th
of the 14 boats that finish, 6 hrs 45 minutes, almost 45
minutes behind the lead boat. We wouldn’t have caught
them even with double blades, but would have done better.
Finish
Having arrived at the finish tired
but functional, I stopped to talk to the lead paddlers about some
of the finer points of boat racing and design. The lead paddlers
were three Creoles from the Gales Bank area and really knowledgeable
as well as capable paddlers. Also all over six feet tall with
long corded muscles and maybe two percent body fat. One fellow
looked at me finally and said the words I’ll always cherish
and remember. “Mon, you got a lot of heart, but you’re
too f*****g old and heavy to do this s**t”. True, but what
an adventure.
Postscript
What would I have done differently?
Not much. The design I think is fine. Building technicalities
aside, I should have verified that double bladed paddles were
ok back when building the boat. I should have come back earlier
in September so we would have been able to practice more. Also
should have taken more pics at race time and given camera to someone
to take more pics. Ah well, there are only so many hours in a
day and so many days in a week. And only so much time to spend
on a hobby-obsession. And the Creole was right, I already knew
that no boat ever won a race, that honor belongs to the paddlers.
Still, it was a great and worthwhile adventure.
Normally my obsession with boats
and boat building is a solo event and I try to keep from letting
it dominate my life. Susie is probably in a better position to
judge my success than any one else and someday maybe I’ll
ask her.
Building Miss Lavi however,
intersected and affected a number of lives that I should
acknowledge. Susie and her Mom for affecting a vacation
we had already planned. Mr. Joe Loskot for providing the
help, material and space to build the boat. Miss Lavi (Miraslova
Loskot) for the gracious use of her name. Sergio Barraza,
for his help and friendship. Edwin and others at the mill
for their assistance. I thank them all.
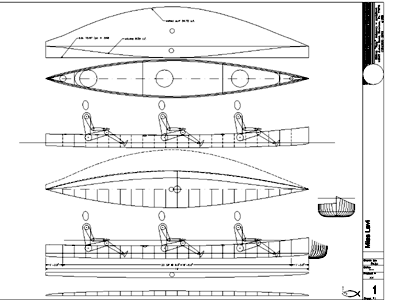
click to enlarge
|