A new Technique for Epoxy-Glass
by John
Blazy
Most people do not enjoy
(after the first half-hour) the constant sanding, filling, then
fairing . . . then sanding, filling, then fairing . . . then etc.
on a hull or surface that they want done in "The Look"
that they saw in the brightwork of the last 100K yacht they saw,
so if you want this effect a little easier - follow this process:
Lay 4 or 6 oz cloth in
epoxy of choice as normal. Add a good amount to fill the weave.
At this point, most people are stuck with this:
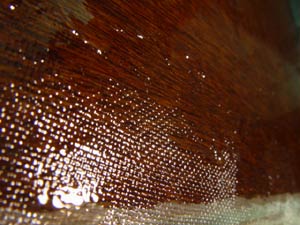
But if you want this:
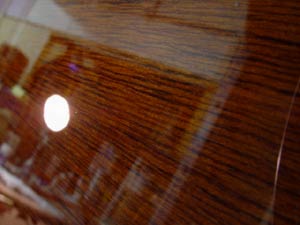
then you must lay in a
pre-sized sheet
of .030" polyester film into the wet epoxy...
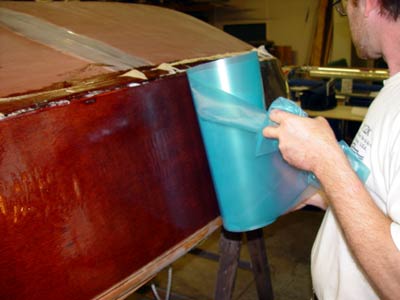
...and roll out the bubbles
with a roller of some sort...
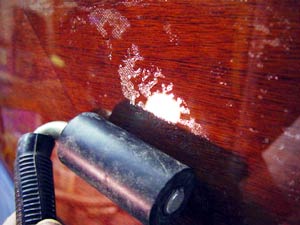
...and then let it cure.
Looks awesome just with the film - it gives you a preview of the
surface you might get with a good varnish job.
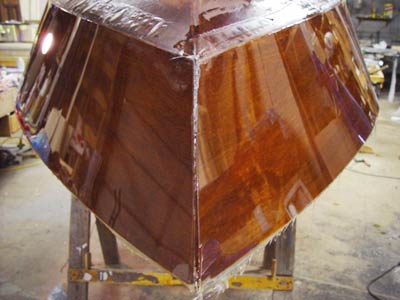
The film simply peels off just before you plan to scuff sand,
then varnish. The surface is flatter than you could ever fair
it.
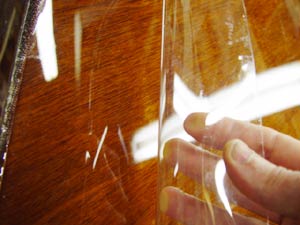
I suspect that if more people
saw this film procedure, it would become standard practice. It
actually is standard practice to lay in a release fabric that
is pulled off after cure, leaving a rough surface for subsequent
coats of epoxy, but this film is superior to that in that it "pre-fairs"
the surface due to the thick film's flat memory, leaving no wrinkles
or waves, having the ability to even 'feather out' high and low
spots.
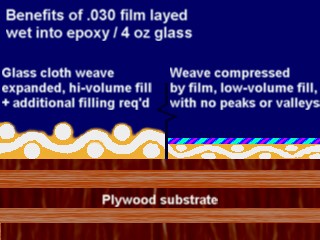
Here is a computor graphic
I did to illustrate the benefits of laying film into wet epoxy
and glass cloth, showing how the film compresses the weave of
the cloth and allows for much less epoxy to be used in this method
of layup. It also shows how the peaks of conventional weave filling
would likely be sanded off, compromising the integrity of the
reinforcement.
Now that the bottom is glassed,
I can cut out the openings for this glass-bottomed (Lexan, actually)
boat I designed called "Calypsee". Here is a recent
pic of the mahogony coaming and interior:

See progress pics at www.pbase.com/dr_dichro
and click on 'elecric boat construction'.
John Blazy
|