The Banca Builders of Malapascua
by Perry
Gamsby
I first came to Malapascua Island
two years ago with my soon to be wife. I was there to dive Monad
Shoal and swim with the awesome Thresher Sharks. Often over twelve
feet long with scimitar like tails two thirds their length, they
are breathtaking to watch. These pelagic creatures come up to
the summit of the undersea mount of Monad and look for cleaning
stations run by greedy Cleaner Wrasse. Once I was priviledged
to see one breach and flip high into the air before swimming back
down to the depths.
I had been there several times
before I wandered away from the tourist beach and discovered the
Banca builders over on Logon Bay. A banca is a native outrigger
boat, usually powered by a small, air-cooled gasoline engine up
to 16hp. Larger boats with more beam are locally referred to as
"Pumpboats" and can be as long as 100 feet. They carry
passengers and cargo between islands on the runs too shallow or
commercially unprofitable for the large ferry companies.
Small banca’s up to 15 feet
can be paddle or sail propelled and they are a distinct style.
They have very tall, pointy stem and stern pieces, are very narrow
and the boatman perches on a thwart to paddle. They use a crab
claw sail made from patched together cement or pig feed sacks.
I have seen kids as young as six paddle these canoe like vessels
with amazing skill.
Motorised banca’s start
about 15 feet long and are of a different style. The stem and
stern are pointed forward, rather than straight up like a spire.
Just aft of amidships the engine is mounted on a block of wood,
with the propellor shaft attached by uni-joint or a round pad
connected by bolts. The pad is made of wood and felt like material,
the felt providing the "give" needed to transfer the
drive from engine to prop shaft as the boat moves in the water.
(click to enlarge) |
THIS PADDLE
BANCA IS FROM DAANBANTAYAN AND IS A HYBRID, SOMEWHERE BETWEEN
THE PADDLE STYLE AND THE MOTOR STYLE.
A TRADITIONAL PADDLE OR SAIL BANCA. NOTE THE POINTY ENDS,
PURELY FOR DECORATION. |
Smaller banca’s have maybe
a 5hp or 6hp engine and small two bladed prop. They scream around
at 15 to 20 knots with the helmsman perched atop the hull. Steering
for all motorised banca’s under 40 feet is by bamboo tiller
rod. This rod is attached to a bar, welded to the rudder shaft.
The shaft is bored through the rear deck and keel and is a small,
rectangular piece of steel. The biggest I have seen on tiller
steered banca’s is only 8x10 inches. Most are half that!
Yes, turning gets to be a leisurely process when you combine the
small rudder area with the drag of the outriggers.
MY BANCA AT BOGO
(click pictures to enlarge)
|
|
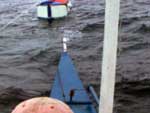 |
DETAIL OF TILLER AND
STEERING ARM JOINED TO RUDDER SHAFT, JUST ABOVE THE RED
CAP. |
Steering is simply a matter of
pushing to turn one way, and pulling the rod to turn the other.
My banca has the rod to the left side, so it’s a push to
turn right and a pull to turn left. Because of the prop rotation,
she turns left better than right, but not much better! Straight
ahead requires some decent back pressure pushing to keep her straight.
The rudders are small because most boats spend half their life
drying out in the shallow inner reef areas at low tide. They tie
a small log under the rear keel to keep the prop and rudder from
being damaged as the boat settles in the sand or mud. Smaller
banca’s are pulled up above the high tide mark while larger
boats 25 feet and longer are often left anchored off the beach.
ME, STANDING AND STEERING BY TILLER POLE
(click pictures to enlarge)
|
|
|
AVERAGE SIZED MOTOR
BANCAS ON THE BEACH AT LOGON BAY |
Anchoring is always with an anchor
off the stern and a line led to the beach from the bow and tied
to anything handy. If the boat is too far off the beach due to
really shallow water, then a bow anchor is used as well as the
stern one. Timing when to drop the stern anchor as you run into
the beach becomes a mark of the experienced banca sailor, here.
Too soon and you are pulled short. Too late and you ram the beach
with a jolt that is guaranteed to draw looks from the locals.
When you get into the pump boat
class, say 30 feet and more, the engines are often old diesel
truck engines, still fitted with their automotive gearboxes with
maybe just third and reverse left inside. Starting is by rope,
the cry of "Uno! Dos!" followed by hopefully the roar
of the engine is a feature of every trip.
Steering then becomes very flash.
An old truck or car steering wheel with the ropes joining it to
the rudder run around a wooden chock. The rope is often a patched
and knotted collection of whatever was on board the last time
it snapped.
The throttle is usually just a
piece of nylon line tied to the carby and held between the toes.
On the big boats they might wrap it around a wood wheel, winding
in or out as required to change speed. Changing speed is essential
in rough seas as you don’t want to get ahead of a following
sea.
With the wide outriggers these boats are pretty stable, but they
can be broached quite easily in the short, choppy seas that storms
throw up. As the wave hits the stern, the bows tend to dip and
the stern lift. Once fully on the forward slope of the wave the
leeward outrigger will dig in and turn you to weather, usually
right behind you, or just off one quarter.
You then have to steer to correct, otherwise you will very quickly
find yourself broadside to the wave. Banca’s don’t
like beam seas. Poorly helmed, they dig in the leeward outrigger
and then flip over if not corrected by steering or weight shifting.
On a boat filled to overflowing with non-swimming Filipinos, the
panic usually guarantees another sad headline in the papers.
For a nation of 7001 islands it
is remarkable how few Filipinos can swim. Add to this the scarcity
of lifejackets and you have a recipe for disaster. The lifejackets
they do fit are locally made, styrofoam filled buoyancy vests
that are always too small for me. I bring my own or put one over
each arm pit!
The boats are made in a traditional fashion and order. They use
no power tools as the island only has electricity from 6pm to
midnight. There are no plans, dimensions or even tape measures
used, just experience, inherited knowledge and an inherent sense
of proportion. They do have a ruler and a small square, just for
the detail work. Everything is made to fit by working from the
"KASKO", or Kilya, the keel.
The keel is made from a single
piece of Lauan. It is several inches thick and solid enough to
shrug off being hammered onto one of the numerous corral reefs
that abound in these waters. Its length and width determine the
final size of the boat. Everything is in proportion to the keel.
THE SOLID LAUAN KEEL
PIECE |
|
The stem and stern pieces are
made from Tugas wood. Like the keel, these important parts are
imported from nearby Samar, a large and heavily wooded island
in the Eastern Visayas, about 30 nautical miles from Malapascua.
They are shaped by eye using a bolo, or machete to give the basic
shape, then finished off with a smaller bolo and sanded.
|
STEM DETAIL. NOTCH IS
USED TO SECURE ANCHOR LINE WITH A CLOVE HITCH |
Sand paper is made using beach
sand and homemade glue, my Visayan was not sufficient to understand
how the glue is made but it is a smelly process, so I believe.
The "paper" is made from coconut husks and the sand
adhered to that. Coconut husks are also used by themselves to
sand back the painted hulls, as well as being great for polished
floors!
With the stem and stern nailed
into place, the ribs and stringers can be sized, cut and fixed.
Bronze nails are the fixing medium of choice. The bevels on the
frame pieces are all hand sawn and chiselled to fit each piece
to the next. This is not mass production type assembly of prefabricated
parts but good old fashioned craftsmanship at work.
The upright ribs go in first all
along each side of the boat. Then they fit the middle stringer,
then the inwhale. The ribs and stringers are made from Lauan and
are easy to work, each piece planed to size and smoothness with
home made planes. The blades are often off cuts from any flat
piece of metal, jammed in place with a wedge in the box shaped
plane.
YOU CAN SEE THE DECORATIVE
CUTWATER ON THE BOW NEAR THE FOREDECK, AS WELL AS THE RIBS
AND STRINGERS. HE IS MAKING THE HELM STATION |
|
Once the frame is in place, the
plywood sides are cut to size and shape. They use the saw in a
reverse, ripping style, cutting towards themselves. The ply is
marked and then placed on a frame made of two lengths of bamboo.
The saw is turned so the teeth are facing the sawer, with the
handle below the work. He then saws while moving back from the
starting edge, pulling the blade toward himself in a rythymic
dance of "pull down, step back, push up; pull down, step
back, push up". They cut straight and true and there is very
little in the way of offcuts. Thrift is essential in a country
where every centavo counts.
The sides are tacked in place
with the bronze nails, leaving half the nail proud. It will be
hammered home later once the whole boat is together and there
is no need to remove panels for re-sizing or adjusting. Once the
sides and the bow and stern deck pieces are in place, they will
hammer home the nails and then epoxy the seams.
Before the introduction of plywood
they used thin strips of lauan, caulked with the husks of coconuts.
The husk pieces would swell when soaked and keep the boat watertight.
Plywood offers the benefit of a considerable amount of time and
effort saved so absolutely nobody uses the old method anymore.
Haven’t done so since plywood became available after the
Second World War from discarded packing crates left behind by
the US Army.
The epoxy comes in two cans, marked
A for the adhesive and B for the hardener. Currently on Malapascua
they use an epoxy that sets kind of coffee coloured. Last time
I was there it was a salmon like shade. They use whatever is available
at the hardware store on the mainland where virtually every manmade
item on the island has had to be shipped in from.
The tropical heat means the epoxy stays malleable for a decent
length of time. They use coconut shells as mixing bowls and epoxy
every seam from stern to stem. Or stem to stern, there is no specific
order or ritual so long as there are no seams left unsealed.
With the seams sealed, they make
the helmsman’s position and the cutwater for the foredeck.
Here they add the individual flourishes of the boatbuilder. Each
piece is hand drawn with the decorative curves that will set this
banca apart as a Malapascua boat. In other areas the helm, or
bridge deck will be subtley different, but only if you are looking
for it.
Another indicator of the boat’s origins is the stem and
stern pieces themselves. Different angles and carved edges let
you know this is a boat from Malapascua. My banca comes from Asturias
on the central west coast of Cebu and the men on Malapascua knew
it the first time they saw it land there. They asked me where
had I come from and I replied "Bogo". They shook their
heads and said Bogo is on the northern east coast, only 16 miles
away. My boat is a west coast boat. I then told them I had bought
it in Balambas, near Asturia and they nodded in a way that told
me they were too canny to be fooled by foreigners!
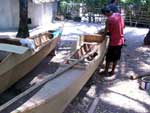 |
VIEW FROM STERN TO HELM
STATION |
Once the helm station, cutwater
(a simple device that deflects the water coming over the bow quite
effectively) and stem and stern pieces are finished, the rudder
and prop shafts are bored. They use an awl like borer and run
it down through the rear deck and out through the keel. Then they
mark the position of the prop shaft hole and bore that. The prop
shaft then has a metal pipe fitted and epoxied in place. The prop
shaft is fitted and run up to the engine mount area. The rudder
also has a pipe epoxied in place and the rudder shaft is fed through
that from the bottom, up.
The angle of the prop shaft dictates
the making and positioning of the engine mounting block. Two support
beams sit athwart the hollowed out keel piece forming the bottom
of the hull. Then a block of Lauan is fixed to the beams with
four bolts driven through from underneath on which to mount the
engine. Both Briggs and Stratton and Kohler, the two more popular
brands, apparently have the same footprint for each corresponding
engine size. Robin and Honda are two other brands gaining acceptance
and I think they share a similar footprint. Otherwise the moutning
block is drilled to suit the final engine choice.
IN THE BACKGROUND IS
THE RUDDER SHAFT AND PROP SHAFT. IN THE FOREGROUND IS THE
AWL AND CHISEL USED TO BORE THE HOLES FOR THESE. THE BOAT
IS ON ITS SIDE SHOWING THE KEEL AND THE SIDES |
|
To make sure the drive shaft from
the engine fits the prop shaft, they will shim the block as required
to line it all up, then epoxy everything in place. All that remains
is to paint, something often left to the eventual buyer of the
boat as he might have some old paint lying around and that will
save him some peso’s.
Meanwhile, the outriggers are being
made. Again, the length of the keel determines the size of the
finished boat and thus the size of the outriggers. Bamboo poles
are heated over a coconut husk fire and then bent to shape around
the stump of an old coconut tree. They are then propped over another
stump and the bent ends weighed down with heavy logs and concrete
hollow blocks for several days.
|
MY BANCA. NOTE THE ANCHOR
ROPE IS TURNED AROUND THE STEM THEN TIED OFF TO THE FORE
OUTRIGGER. YOU CAN ALSO SEE THE CUTWATER AHEAD OF THE FORE
OUTRIGGER |
When ready, they are fitted into
place and tied together using nylon monofilament line. It might
not seem all that traditional, but it is cheap and readily available
and easy to work with. In the old days they made ropes from, yous
guessed it, coconut husks and manila hemp plants. Too time consuming
for this modern age, they now use copious quantities of nylon
line. You can still buy hemp rope and string and I use it for
the halyards and sheets on my own homebuilt sail boat.
With the outriggers bound on,
the engine fitted and the boat painted, she is ready to launch.
Grab a dozen of your village friends and carry her between the
nipa huts to the waters edge, then launch! You then add an anchor
made from steel reinforcing bar bent and welded to form a Fisherman
type. There is just the one style available, Ploughs, CQR’s
and Bruce’s are unheard of here. You also need a paddle
carved from coconut lumber or a bamboo pole to punt her out with.
Total cost for a 20 foot banca
fitted with a 5hp engine, painted and ready to earn a living catching
fish? About US$300. If you are wider than a telephone book like
me, spend the extra few bucks and go up to 25 or 30 feet. My banca
is 30 feet long and the hull is over three feet wide. It has carried
a kilometre long Pamo fishing net and the catch that goes with
it, sacks of cement, crates of beer, live pigs, a mates household
contents, you name it!
For ease of maintenance and repair
by local boatwrights with locally available parts and materials,
the banca can’t be beaten. For operating in waters that
often get very thin and are studded with corral heads and uncharted
reefs, she is superb. Not the best in heavy seas unless you really
know your business but then this is the Philippines. Time means
little and you can always pick another day to go when the weather
fines up and the turquoise sea is like glass.
The banca builders of Malapascua
are a joy to watch as they ply their time honoured craft. Forget
what you see on TV or read in the news. There is no SARS here,
no Abu Sayyaf, no danger except the natural risks of living closer
to nature in a tropical paradise.
Get on a plane and come
to Cebu. Then come and stay on Malapascua for a week or two and
work with these men. Build a boat that will feed a family for
life. Do it with your two hands and enjoy the pride you earn as
you work. When it gets too hot, go for a swim or have a cold beer.
If you want to you can disassemble your banca, stick it in a crate
and ship it home, it might be cheaper than buying the materials
locally and making one in your garage! If you leave it on the
island, you will take away skills you will keep and treasure your
whole life.
If anyone has any queries
about the Banca Builders of Malapascua, or coming to Cebu to learn
the craft, drop me an email (perrygamsby@yahoo.com)
and I would be happy to answer any questions. You can do this
for less than US$2000 from virtually anywhere in the world, fares,
accomodation, meals and a donation to the Boatwright for his teaching.
Salamat Po!
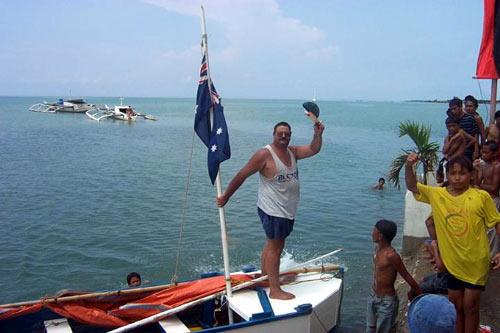
THE
AUTHOR ATOP HIS LATEEN RIGGED, FIRST SELF-BUILT BOAT, "THE
KARL HEINZ OF HEMSENDORF" AFTER HER MAIDEN VOYAGE ON
BOGO BAY, MAY 2003. NOTE THE PUMPBOATS IN THE BACKGROUND.
|