Alisa, a Bolger AS-29
A Refit Report
by Frank San Miguel
Chines: 94 hours Alisa is very
solidly constructed, the builder did a first rate job and she
is in great condition overall after 8 seasons of continuous use.
When I bought her, I knew there would be work to do on the mast,
bow well and chines. For much of her life, the sheathing along
the chines has allowed water into the boat. After I removed the
old stuff from the chines, I counted 15 dark spots on starboard
and 20 on port, and numerous spots around the fasteners. There
were air bubbles around many of the fasteners on the port side
- it looks like they were introduced over time due to expansion/contraction
maybe from the freezes they get up there on the St. Lawrence.
I ground all of these out with a grinder / sanding pad and filled
with thickened epoxy before re-sheathing with 3 layers of 10 oz.
The screws are stainless and the picture you see is the worst
area of the whole boat.
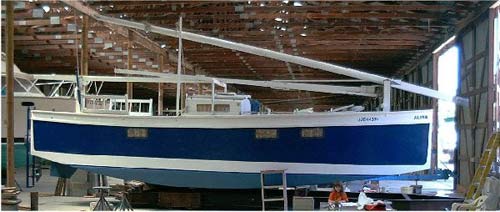
The bottom of the boat is
slighlty convex (which puzzled me until Bruce Hector mentioned
on the yahoo forum that his Micro is that way from the way he
assembled the hull upside down). Also, Alisa's chines were only
1/2" radius. These two factors combined to cause problems
both in blocking the boat for winter and launching the boat in
the sling. I've worked out a gentler blocking scheme and radiused
the chines (using my drawknife and a plane and a grinder) to 1"
and added 3 layers of 10oz cloth cut at 45 degrees, which should
give me an increased strength in this area of 4 to 10 times. None
of the black spots penetrated very far and I only found one or
two areas where I could easily chops stuff with my chisel. I filled
these areas. I'll have to take a look next spring to see if problems
are getting worse. If so, I'll have to chop out portions of the
bottom and scarf in replacements (like I did with the mast).
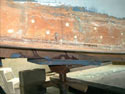
Chine repairs. Pre-grinder
(click images to enlarge) |
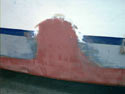
More chine repairs. after filling, before smoothing |
I am very happy with the
way the 10oz, 45 degree strips works on the chines. I used 8",
6" and 4" widths, cut with scissors. The width gets
narrower when applying because of the 45 degree cut. I did the
two 8" layers first (overlapping 2") and then the 4"
last. Then I gloped loads of stuff thickened with 50/50 microballoons
and fused silica. I used Raka epoxy, which cures soft. Much of
the work was done in 90-98 degree F temperatures, which the Raka
very slow hardener handles very well! I experimented with biaxial
cloth and 9 oz tape and the 10oz 45 degree stuff was the best
by far in quality of application. Robb White used 16 layers of
4 oz cloth on the bottom of his Rescue Minor boat. I think that
technique might be even better, thought it would involve more
cutting.
Bilgeboard Trunks: After
launching I still had leaks into the boat. These are almost certainly
coming from bilgeboard wells. Figure 1 shows how the boat is now
and what I intend to do to fix it. The plans seem a little ambiguous
on the subject, but John Dalziel's boat, Zoella, is built like
"AFTER." The current construction in Alisa prevented
the builder from taping the seam between the bottom and the trunk
sides ("tape here" in the illustration)
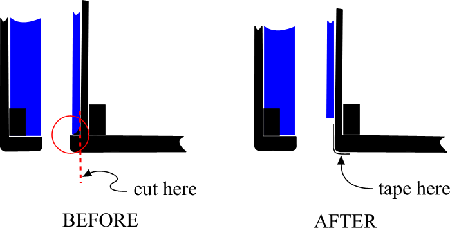
Figure 1. Bilgeboard leaks
As a result, water gets in right
along the dotted red line. I think I may be getting a little bit
of water from underneath the exterior chine as well.
Blocking: A lot of damage was done
to the chines while Alisa was in the slings and on blocks because
of the aforementioned convex bottom and sharp corners. I devised
a pretty simple but effective way to minimize stresses during
blocking (Figure 2). After one launching and one haulout, I can
claim success! With the combination of armor plating on the chines
plus the new blocking system I have seen no damage, dents or cracks.
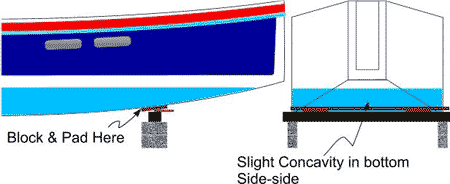
Figure 2 Blocking Arrangement
The key was supporting the 2"x10"
bunks a few inches *inboard* of the chine, allowing the bunk to
bend to the concavity of the bottom. A bunch of old carpet didn't
hurt either :-)
Bow well: 20 hours I bought
Alisa knowing I would be repairing some leaks, the most pronounced
of which is in the bow well. The failure was in the bond between
the fillets and the epoxy coated plywood on the floor of the bow
well. Every piece of wood in the boat was epoxy coated before
assembly. The wood is in great condition (built in 1994). I can
think of two explanations for the failure:
-
Insufficient surface prep before applying
the fillets. I certainly can understand how this might happen
after spending 4 hours in that little space. It is a very
hard area to get into.
-
The fillets were too
small. I think 1/4" radius isn't sufficient. Also there
was no stitch-n-glue style sheathing over the joints. I am
sure more strength is required based on the stresses imposed
by the mast/tabernacle.
Repairs to the
bow well. (CTE) |
I chopped out all of the old epoxy
fillets, sanded the whole bottom down to the wood (epoxy primer
and polyurethane rust paint - whew!), laid down 1" + radius
fillets and laid a layer of 7oz tape plus another layer of 7 oz
sheathing over the whole floor. Looks pretty nice. Talk about
a difficult space to work in though! 10" x 4' x 3'. My bones
were creaky from all of that contortion work :-)!
Replace rot in mast foot. (click to
enlarge) |
Mast Rot: 18 hours Rot had
set in to the foot of the mast where the lead weight is attached
using screws and SS plates. I suspect it happened during the winter,
when the mast was horizontal and water and snow could collect
on the horizontal surface, since the rot was worst on the "top/forward"
side of the mast!
I had to scarf two 1 1/2 x 4 1/2
boards into two sides. I also had to make a wedge 13 x 1 1/2 x
9" ("stop for mast kevel"). That's four 4 1/2"
x 15" scarf cuts plus a big 13" cut. I've made scarf
joints once before (for a mast) using a saw, hammer, chisel and
a hand plane, but I was looking for a more efficient way. I first
tried by grandfather's 6" jointer (Big Power Tool) for the
13" wedge. It was loud and dangerous and made a lot of dust,
but it worked. My mast was still on its tabernacle - the piece
to be repaired was suspended 15' in the air, so I couldn't bring
big power tools. Instead, I marked the cut and made depth cuts
every 2" with my Japanese saw.
Then I sharpened up the drawknife
and chopped away.
It is amazing how much stock you
can cut away in a short time with a sharp drawknife. wow! I finished
up with a Baily #4 plane and a bull-nosed rabbeting plane (total
of $80 worth of tools from various antique shops in Pennsylvania).
Filling the weave: When
I built my AF3,
I figured fairing the hull was for sissies. After all, I wanted
workboat finish and who would care if there were some rough spots.
I sheathed bottom but not the sides. Filling the weave with a
third or fourth coat of epoxy seemed purely optional. All those
articles and chapters in the books and magazines about fairing
are merely the result of some misplaced 19th century yachting
aesthetic that places a disproportionate value on form over function
- right? I'm not so sure. After spending a weekend upside down
sanding off poisonous bottom paint from an un-filled, un-faired
bottom in order to effect some repairs to the sheathing, I've
realized there is a very practical reason for fairing and filling
- repairs!
|