Delta is a 12x2 foot double ender made from one sheet of plywood
using the reversed triangle (hence the name Delta) technique first seen on
David Beede's "Summer
Breeze", winner of the 2001 Duckworks
design contest.
To build one of these boats the 1 foot side panels are cut off, then
laid on top of, and temporarily clamped or nailed to, the 2 foot wide
bottom panel, while 6 inch by 2 foot triangles are cut off the corners.
The triangles are measured in from the ends of the sheet instead of out
from the middle because the plywood will not likely be exactly 8 feet
long. While the panels are still held together, and as per David's
instructions, the "bumps" are rounded off. I rounded off 6 inches by
marking the edges 3 inches on each side of the bump, springing a small
metal batten through the marks, and sanding off the excess. The radius of
the arc is just over 18 inches, a number used in saw kerf bending of the
chine battens and bottom skids as described later.
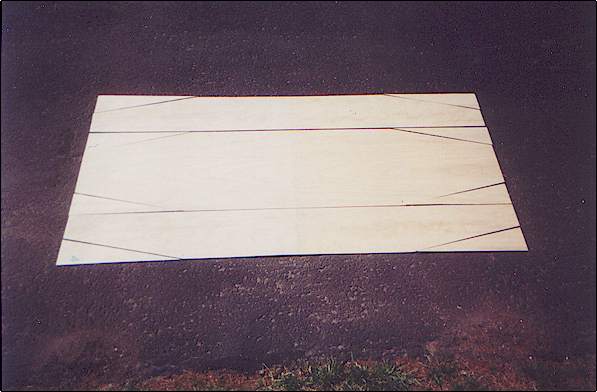
I calculated the relationship between the draft (d) in feet and the
immersed volume (V) in cubic feet to be V = 8d + 3.46 d^2 - 2.31 d^3 where
d^2, d^3 are d squared and cubed. The freshwater displacement in pounds is
62.5 times V. The wetted surface (WS) in square feet is 8 + 24d. The
waterline length (LWL) is 4 feet plus 8 inches per inch of draft.
Displacement speed in miles per hour is 1.54 times the square root of LWL.
The following table shows results for selected drafts. Its interesting how
all the numbers except speed are linear with draft.
draft |
volume |
disp. |
WS |
LWL |
speed |
(inches) |
(cu ft) |
(lb) |
(sq ft) |
(ft) |
(mph) |
|
|
|
|
|
|
3" |
2.2 |
136 |
14 |
4.66 |
3.3 |
4" |
3.0 |
185 |
16 |
6.66 |
3.9 |
5" |
3.8 |
235 |
18 |
7.33 |
4.2 |
6" |
4.6 |
286 |
20 |
8.00 |
4.4 |
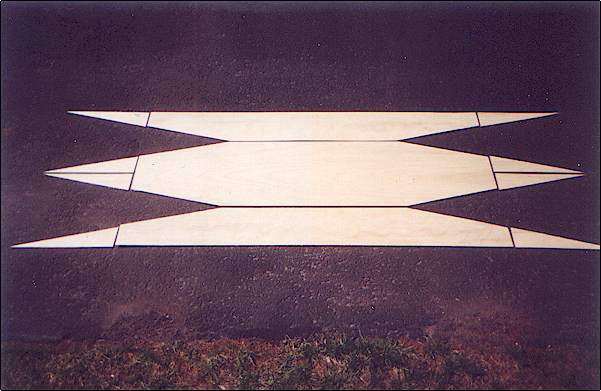
Rearranging the pieces shows the sides and bottom of the boat. The
plywood used was virola underlayment. This is new in our area. I wanted to
try it out for another project due to start in a few days. Virola is from
Brazil. It is not rot resistant. The inner ply feels hard but the two thin
outer plys are soft, porous sapwood. There were some sheets with no edge
voids. The face plys on some sheets were both smooth and free from defects
apart from a couple filled splits near the ends.
When I got a selected sheet home and checked with a lamp there were
no interior voids. The soft face plys had fuzzy areas. Where the plywood
was covered with resin the fuzz could be ignored. Where the plywood was
painted the fuzz could be sanded down after the first coat dried. A sheet
of this virola underlayment weighs only 8.5 pounds, half the weight of
lauan underlayment or 5.22 mm okume marine plywood.
I did some tests on this plywood. A coat of automobile engine
antifreeze was brushed on to retard rot, and idea inspired by David
Carnell. One end of the plywood was treated and the other left untreated
for comparison. Polyester resin was also tested on the plywood, reinforced
with polyester or with fibreglass. The cheap polyester fibre is sold as
drapery header tape at fabric stores. Barend Migchelsen mentioned using it
with polyurethane construction mastic (PL Premium) to tape seams. It does
not unravel and create a mess like fibreglass. Unfortunately I was rushed
an did not wait for the antifreeze treatment to dry thoroughly before
taping the butt joins. I was able to pull the tape off some of the cured
joints.
Another problem was the polyester cloth is stiff and would not
conform unless the surfaces to be butted were very level across the seam.
After curing there were air pockets under the cloth. I assume this is
because polyester resin is not as viscous as polyurethane mastic. I
rebutted one face with a triangle of doorskin plywood bedded in
polyurethane because it will cure on a moist surface. That saved time and
kept the project moving along. Later, when the wood was dry the other side
of the same butt was taped with fibreglass without problem.
As it happens all butts on this boat are above the waterline so
their condition is not crucial. A third of the boat's bottom was coated
with polyester resin. Because the wood is porous one coat was spread
without any catalyst and allowed to soak in. Then another coat mixed with
catalyst was put on so the resin would cure right into the wood. It made
for a very slow cure, about 18 hours. (Don't try this with epoxy. Epoxy
has to be well mixed with its catalyst in order to cure.) For comparison
another third of the bottom was treated with two coats of linseed oil and
the last third was left untreated. Consequently the hull is quite a
chequerboard of surface treatments.
The entire outside of the hull was given three coats of some
exterior oil house paint I wanted to use up. The inside of the hull got
two coats of linseed oil. In the course of building this boat I discovered
the way to identify an amateur boatbuilder. He's the one with the sawdust
and paint on his pajamas.
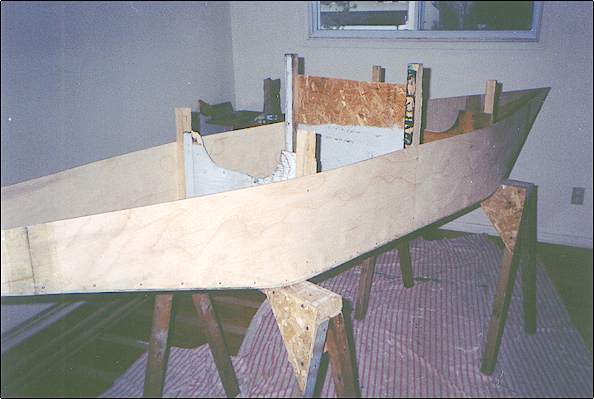
After the plywood was cut up the nice spring weather turned bad
forcing construction indoors where there was no room to swing a camera. I
doubt anyone would be interested in photos of the designer/builder on his
knees under the hull sawing knots and nail holes out of recycled lumber.
People should look instead at
David Beede's Summer Breeze photos and at those of the
Duckworks editorial board.
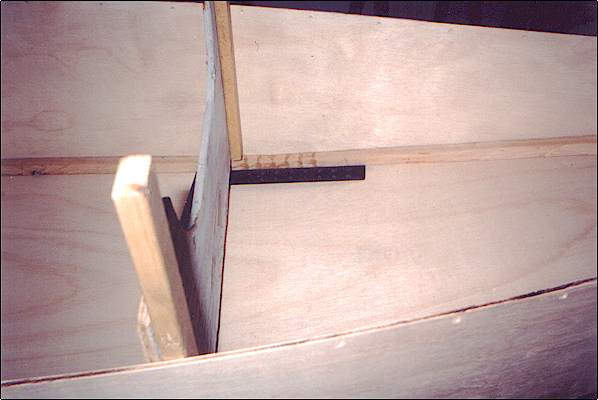
This photo shows a chine batten bent in two directions using saw
cuts. The dark lines are the glue impregnated saw cuts. A temporary mould
and a 12 inch carpenter's square appear in the photo. So does a knot hole
in the chine batten on the extreme left. The damp wood from the antifreeze
treatment forced a change of plan from trying polyester taped seams to
chine battens glued with PL Premium and fastened with wood screws. After
ripping 3/4 inch by 3/4 inch battens out of red cedar 2x4's it was
discovered they would not bend to the shape of the hull.
Discarding the options of setting up steam bending equipment in the
bedroom, or ripping thinner chine battens and running out to buy shorter
screws, I recalled something about wood bending with saw kerfs from Fred
Bingham's "Boat Joinery". I decided to give it a try. You clamp a piece of
scrap wood the same dimension as the wood to be bent and a bit longer than
the radius of the bend to a flat surface, saw almost through the scrap,
raise the far end until the saw kerf closes, and at a distance out from
the kerf equal to the radius of the bend, measure the height of the scrap
above the flat surface. That height is the spacing between the saw kerfs
in the piece to be bent. Imagine trying to saw 6 closely spaced kerfs in
12 foot battens in two places 4 feet apart without breaking the battens.
Fortunately chine battens do not have to bend in a continuous curve
on boats with straight sections. They can be put on as shorter pieces with
the cuts falling on the straight sections. The chine battens were cut into
shorter pieces to make cutting the kerfs easier and to relocate the knots,
nail holes, and rot takeouts in the recycled lumber. Alternating the
direction of the kerfs enabled the battens to bend in two directions. I
don't know if that's been tried before. It took a while to get a feel for
how deep to saw the kerfs but by the last of the four bends I had it down
pretty good. Only two of the four broke. I used them all anyway with no
problems to date.
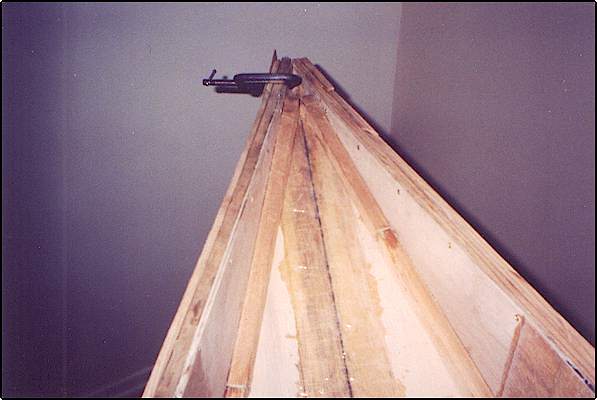
The ends of the boat were wonderfully sharp before the gunwales went
on. I wondered if I would be arrested for paddling a dangerous weapon. The
seam in the photo is one of the good polyester butts. I do not have any
data on how strong this tape is. The ends were prettied up with chisel,
saw, and sander. I am still undecided about putting on small decks,
wrapping the ends in fibreglass, leaving them as is, or what.
Some builders will have noticed the boat has Bolger bows. That is to
say the plumb sides come together to meet the rising flat bottom all at
the same angle (a gradient of 1-in-4 on this boat). Phil Bolger, a popular
designer of plywood boats for amateur builders, claims this provides good
performance through the water. The Bolger ends were unintentional. I
didn't notice the Bolgerness until the finish was going on.
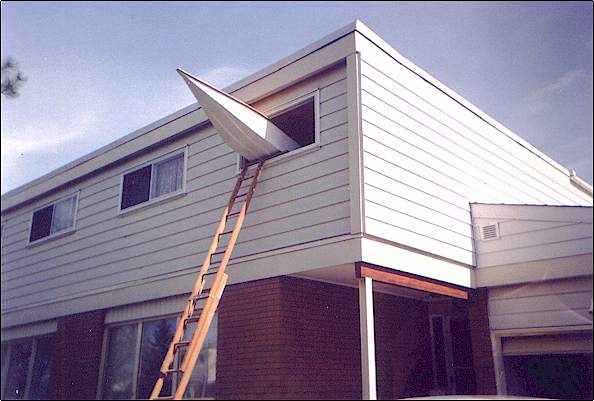
I haven't seen one of these photos on Duckworks of a boat coming out
a second story window so thought I'd include one. I prefer the bottom
skids to a keel. A thin plywood bottom needs something to support it over
the two foot span. If you don't want to sit on an inside keelson then the
stiffening has to go on the outside. If its a keel, when the boat is
ragged ashore it drags on the keel and one chine which tends to chew up
the chines. When a boat with skids is dragged ashore it drags on the skids
so the chines don't get chewed up. I guess that's why they're called
skids.
I figured 1/2 inch thick skids would bend to the shape of the hull
because the gunwales had been made out of two thicknesses of 1/2 inch
thick by 3/4 inch red cedar and these had bent to the shape of the hull.
The 1.5 inch wide skids were ripped off an 8 foot spruce 2x4. They would
not bend to the shape of the hull. I used the saw kerf technique again.
This time it went much better. Only one broke and then only on the final
glue up.
Alas, the skids took the unfinished weight of the hull from a lovely
light 22 pounds up to a disappointing 28 pounds. That's what you get for
rushing ahead without careful thought. Smaller, lighter, shorter skids
would have been fine. The skids were glued to the hull with polyurethane
and held in place with screws through from inside until the glue cured.
Then the screws were removed and the holes filled with drops of polyester
resin from the end of a tooth pick. I did not have screws on hand short
enough to leave in. The final weight of the boat is 29 pounds. It could
have been built to 25 pounds or maybe less.
The edges of the plywood and all glue lines exposed to water were
protected with two coats of polyester resin applied with a putty knife and
a tooth pick. No fooling around with brushes or sponges on a stick. When
the job is done just wipe the resin off the spreader with a rag and go
make a pot of tea. I wear kitchen latex gloves and toss them out when the
buildup of hardened goop starts flaking off and falling on the work.
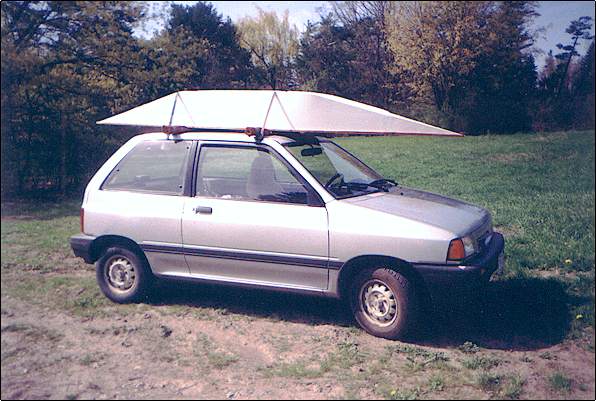
A very small car gets a stylish spring hat. I think it looks regency
period.
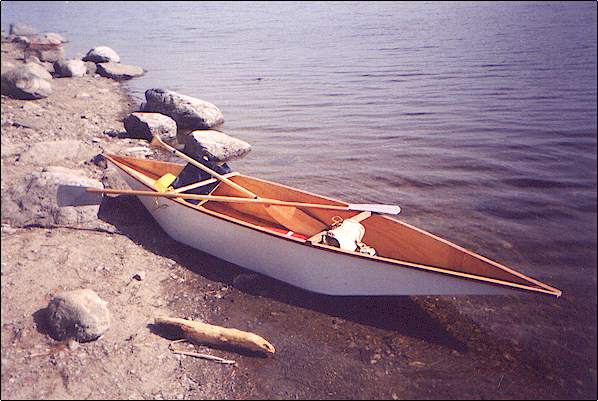
After some practice the Delta boat, with its flat entrance and exit,
paddles straight. Using a canoe paddle I heel the boat over until the
knuckles of my lower paddling hand dip in the water, and push the upper
paddling hand out so the blade is a bit under the side of the boat. When
heeled over the boat has a longer waterline and goes faster and
straighter. To glide in a straight line the tip of the paddle is left in
the water.
The double bladed paddle in the photo was made from a paint roller
extension handle and a discarded aluminum snow shovel. (I learned recently
a local junk yard sells discarded aluminum traffic signs for $5.)
Attaching the blades off centre puts them deeper in the water while not
lifting the opposite arm as high. The boat goes straight with this paddle
if the blades enter the water forward, about where the boat itself enters
the water. The action is like a swimmer pulling himself along.
In smooth water I've tried rocking the boat a bit on each stroke,
getting the chines to dig in. Directional stability is not as good with
double blades as with a single blade. A skeg or kayak rudder would help.
I'm looking forward to rigging the Delta boat for sail, the one from the
one sheet Loonie which appeared in Duckworks in 2001.
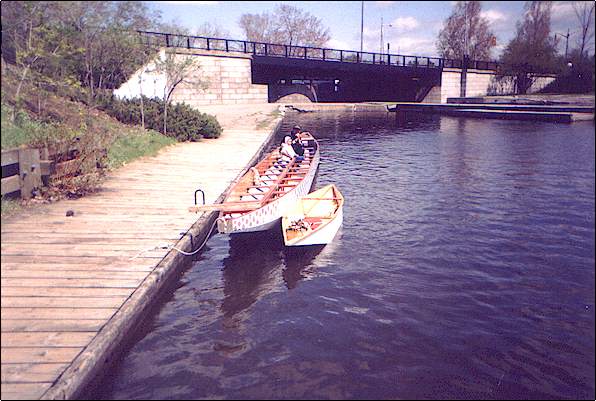
The Delta boat nuzzles up to a dragon boat, looking like mother and
calf. In the background is a cantilevered swing bridge at the entrance to
a lock on the Rideau Canal. The dragon boat was donated by Nortel Networks
back in the days when everyone imagined the company was making money. It
is paddled by a tribe of wild Amazons who build up momentum but have
difficulty deciding which way to turn. I keep a wary eye out for them when
paddling in the vicinity.
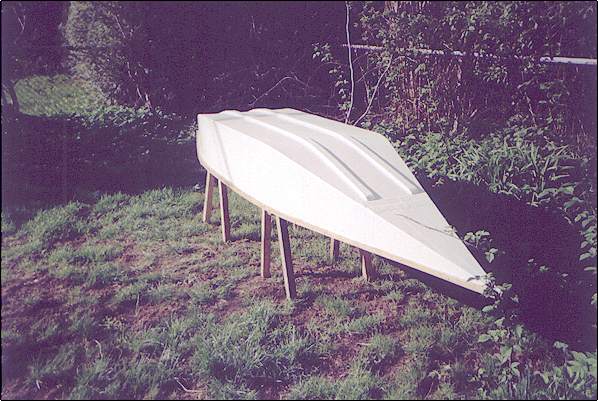
When not on the water the Delta boat rests on custom made wobbly saw
horses at the bottom of my garden. The saw horses go inside the hull for
good support. It takes 8 legs to make a pair of sawhorses as I discovered
after carefully cutting out 4 and trying to make this pair of sawhorses
with them. Its a nice boat. This six foot adult can recline comfortably in
it. I built it for an inner grandchild to keep us out of trouble. He seems
to like it. I certainly do.
- END -
|