CHAPTER 3
CONSTRUCTION OF THE PRAM
BUILD A TO-SCALE MODEL FIRST
Building a model to scale from 2-mm
cardboard is a sure, fast, and inexpensive way to check if the
calculations of the measurements were done correctly.
At the least, it saves you the trouble of having to buy wood
twice!
The stiff cardboard is sold in art stores under different names.
One of these names is mounting board.
In Canada the manufacturers’ name is Eska.
A number is added for the thickness.
Ask for Eska #092, or #120.
The panels measure approximately 30"x40".
For easy handling, ask the store attendant to cut it into two
panels of 30"x20".
The price is approximately C$7 inclusive the cutting, and
inclusive the 15.56 % sales tax. You
will be surprised how much experience, and insight, making a model gives
you for constructing the full-sized project.
Unless you want to make it
a conversation piece to be exhibited on the chimney mantle of your
living room, it is not necessary the complete the model all the way.
The photographs on page17 illustrate clearly what is minimal to
be completed to verify the main dimensions of the parts layout.
In this project, the side panels on the bow and transom boards
with the mast thwart, the thwart amidships, the deck fore and the
transom bench aft, all set on the cross frames, are sufficient to check
and verify the correctness of measurements for the material layout.
Little strips of masking tape hold the parts together.
Making a model has another advantage in the northern states of
the USA and Canada: You
don’t have to wait until spring.
Making a model is done comfortably at the kitchen table no matter
how bad the weather is outside. And
its greatest merit: It can
be taught in a classroom!
Scale Ruler
In Canada, a triangular Staedtler-Mars scale 987
18-34 Engineer costs just over $10.
The 12" ruler has 6 scales numbered from #10
to #60 inclusive. The
#60 scale is 1/6 of the #10 standard inch scale.
One advantage is that no measurement conversions are necessary.
No, conversion calculations, no chance of making mistakes!
The second advantage is that the decimal subdivisions of 1/10"
(0.1") of the #10 scale correlate with the decimal 1/10"
subdivisions of one-inch-grid school graph paper. The combination
of the ruler with the graph paper is ideal for accurate drawings of the
set of plans! In full size,
with a sharp pencil, the lines can be drawn to 1/100 (0.01) of an
inch accurate!
BUILDING
SEQUENCE FOR THE FULL-SIZED HULL
Preliminary
Cuttings
1.
Rip the two 8' – 2x4s as shown in the top drawing on page 11.
2.
Rip the chines and the inwales as shown in the lower drawing on
page 11. Tape the pair of slats of the chines together. Store the slats
in a safe place. Do the
same with the slats for the inwales.
3.
Rip the 1"-wide guardrail batten from the second 10'
– 1x12. See page 10.
Rip this ¾"x1" batten
into the two guardrail slats. Tape
the slats together and store with the other slats.
Preparing the
Jig Setup
1.
Cut the four temporary cross frames from the cheapest available
quality of ¼" plywood as shown on page 15.
From the same kind of plywood, cut the brackets for the cross
frames as shown in the drawing at the bottom of page 15 for the cross
frames fore and aft. Cut
the other four brackets for the amidships frames. See page13.
2.
Assemble the jig ladder as shown on page 13.
Place the ladder perfectly level on three sawhorses.
Make a small sharp V-notch into the middle of the front edge of
the first rung fore, and in the aft edge of the last rung aft.
Span a piece of twine in the notches over the rungs as
centerline. Tie a weight at each end to keep the twine tautly straight.
3.
Draw the station locations of the cross frames on the ladder
beams. Place the brackets
on the rungs. Secure them
with screws into the beams.
4.
Place the cross frames on the ladder as shown in the Profile view
on page 13. Line up the
“dead center lines”– )O( in the drawings on pages 14 and 15– of
the cross frames with the centerline/twine on the ladder.
Secure the cross frames with thin finishing nail onto the
brackets. Leave the heads
of the nails stick out for easy removal. Check that the cross frames are perfectly plumb on the
ladder, and exactly fore, or aft, against their station line location as
shown in the Profile view on page 13.
Be
finicky about this lining-up process!
Side
Panels
1.
Cut the four, 15.7"-wide side panel strips
from a ¼" - 4'x8' board of plywood as shown on page 12.
Do not cut off the transom knees shown in that drawing, but
leave the side panel strips rectangular!
2.
Side panel joints: With
eight ½"screws, temporary butt each 48"strip
against a 66" strip on the inside with the butt strips of ¼"
- 4"x11.9" plywood that were cut from the second
4'x8' plywood board. See
the drawing at the bottom of page 12. (The good side is the outside.
The butt strip on the inside leaves the edges free).
Place the screws on the butt strip on the inside.
Put a piece of cling wrap between the butt and the panels.
Tape the joint on the outside with a 4"-wide strip of
either fiberglass with epoxy, or Buckram with plastic resin glue (Urea
formaldehyde). When the
glue has dried, turn over the panel.
Remove the butt strip and the cling wrap, tape and glue the
inside of the joint. While
the epoxy or glue is still wet, put back the butt strip.
Don’t tighten the screws too much.
It will press the gluing substance out.
Let the glue dry overnight.
Remove the screws; fill the holes with plastic wood.
Note: In my experience, taping the joints in two separate steps is
easier, less messy, and less risky than doing this joining of both sides
at the same time in one step. It
only takes a little bit longer.
3.
Place the side panels on the setup on the protruding “third”
hands of the cross frames as is shown in the photographs of the model on
page 17.
4.
Line up the lower corners of the side panels at station #2
+2". (1½" fore of the outside of the bow board).
Secure the side panels in that position with 2" metal
binder clips (Staples, Cat. #43456, 12 per pack, C$4.57 +
sales tax).
Note that the side panels
go free fore of the first cross frame, and aft of the last frame.
Cross Frames’ Adjustment, Chine Installation
1.
Mark the height of the side panels and the rocker line bevel on
the cross frames.
2.
Take off the side panels (carefully), and the cross frames.
3.
Cut off the excess of the cross frames flush with the bottom
rocker line of the side panels. See
pages 14, and 15.
4.
Cut the notches for the chines in the cross frames.
5.
Place the cross frames back on the ladder.
Double-check their perfect alignments and that they are
absolutely vertical on the ladder.
6.
Cover the edges of the cross frames with a strip of cling wrap
over the sides and the top. Give
special attention that the notches are really covered with the cling
wrap that no glue can get onto the cross frames.
7.
Place the chine battens in the notches.
Cover the topside of the battens with masking tape to prevent
that any sticky substance can attach to this side.
With an ⅛" drill carefully drill vertical holes
into the chines just in the middle where they rest upon the cross
frames. With a nail pusher,
carefully, push a thin 1¼" finishing nail through the
predrilled holes into the cross frame.
Leave the head stick out. The
nails only have to hold the chines in place until the gluing of the side
panels has dried.
8.
Cover the sides of the chines with epoxy or plastic resin.
9.
Replace the side panels in their original positions.
Secure their positions with the binder clips.
Clamp them at the chines. Let
the glue dry overnight.
10.
Remove the nails and the masking tape.
Bow and
Transom Boards
1.
Hold a ruler against the side panel under the sheers as shown in
the photograph on page 17. Mark
a horizontal line on the longitudinal brackets.
Measure the distance of this mark to the top edge fore of the
cross-frame. It should be
(or close to) 19.7", which is the actual length of the bow
board without the crown.
2.
Measure the width of the bow board between the inside of the side
panels at the sheer.
3.
Measure the width between the side panels at the chines.
4.
From a sheet of Bristol board (C$0.79 at any drugstore), make a
template of an isosceles trapezoid with these measurements.
Check that the template fits exactly between the side panels over
the longitudinal brackets. Cut the notches in the corners at the chine for the chine
slats. Mark the sloping
line of the bow board on the chine slats.
Remove the Bristol board template. Carefully cut off the little
excess pieces of the chines along the marked bow board line. Do it with the Japanese flush cutting saw.
Do it without cutting into the side panels.
Pry the ends loose from the side panels, remove the excess.
5.
Take the exact size of the bevel angle between the side panels
and the Bristol board template with an adjustable bevel.
6.
Use this template to cut the first beveled bow board planks from
the first 10' – 1x12. Fit
the planks between the panels for a “dry run” before the planks are
glued together over their common, ¾" edge.
Note that the notches for the chines in the template are NOT
cut into the boards. The
boards cover the ends of the chine slats.
7.
Screw the board temporarily between the side panels.
Mark the bevel of the crown between the sheers, and the bevel of
the bottom between the chines.
8.
Draw the crown on the bow board as in shown on the last two pages
of the Appendix.
9.
Cut both bevels. Reattach
the bow board (temporarily) between the side panels.
10.
Repeat point 1 to 9 inclusive for the cutting and placing of the
Transom board.
11.
With a Japanese flush-cutting saw, cut of the excess of
the side panels at the bow and transom boards.
Cut the plywood on the pull stroke only!
12.
Place the boards between the side panels for a “dry run”.
If you are satisfied with a perfect fit, cover the beveled side
edges with epoxy or glue, and clamp the boards between the side panels
with the original screws until the glue has dried.
Remove the screws that did the clamping.
Fill the holes with wood filler.
13.
With a 3" circular hole saw, make the cut
for a sculling oar in the edge halfway between the middle line and the
sheer line in the edge of the transom board on the starboard side if you
are right handed. If you
are an outspoken “southpaw”, cut the hole in the port side.
Cut the slot for the tiller.
Bottom
1.
Cut the rectangular bottom panel.
See the lower drawing on page 12.
2.
Draw the longitudinal middle line on the good side of the bottom
panel.
3.
Place the panel onto the setup. Line up the middle line of the bottom with the
centerline/twine of the jig. Secure
the bottom with small finishing nails making movement impossible. Leave the head of the nails sticking out for easy removal.
4.
With the Japanese flush-cutting saw, remove the excess outside of
the side panels. To prevent
tearing of the saw into the plywood bottom panel, cut only on the pull
stroke of the saw. Start
at Beam! Work toward fore
and aft.
GO
SLOW!
5. Take off the bottom
panel. Put epoxy or glue on
the chines and the bottom edges of the bow and transom boards.
Put the panel back on. Until
the glue has dried, secure the bottom onto the setup.
Use the original finishing nails, and/or rope held with elastic
binders. Make the pressure
just enough to clamp the bottom, but not too much to squeeze out the
glue, or distort the hull form! If
you use ropes with elastic binders, place them as close as possible to
the cross frames.
Mast Thwart
Double-check the
measurements of the width between the side panels at station #5,
and station #5 + 10½".
Cut the mast thwart to these measurements.
Temporarily install the thwart aft and against cross frame #5
with four screws flush with the sheer line
Guardrails
Never use glue to attach parts that are often
and easily damaged. It
makes it difficult to take them off!
Instead use (stainless steel) screws.
Later,
the guardrails are attached to the sheers with these stainless steel
screws through the sheers into the spacer blocks, or directly into the
inwales.
At
this stage, the only purpose of the guardrails is to help to keep the
hull in its form. Therefore,
before lifting off the hull from the jig, attach the guardrails temporarily
with screws flush with the sheers.
The rule is:
Always screw thin onto thick.
In
this case, it would mean that the guardrail would have to be attached to
the hull with screws from the inside.
Since this is only a temporary attachment, sin against
this rule.
Hull
Spreader
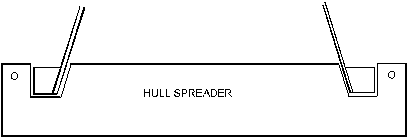
Measure
the width at station #8 (Beam).
Make the hull spreader from the same plywood as the temporary
cross frames as shown in the drawing.
Place the spreader just in front of cross frame #8.
Tie the spreader around the bottom with rope and an elastic
binder cord to keep the spreader in position.
The hull is now ready for “lift off”.
Sealing
the Hull Seams
Sealing
the seams is done now, or it can be left until the inside hull carpentry
is finished. It is done
with 4"-wide tape, either fiberglass with epoxy, or Buckram
tape with plastic resin. Sand
all the sharp edges round by hand!
Start to cover the (horizontal) joint seams of the bow and
transom boards. Buckram
tape is thin enough that the vertical strips on the side panel joints do
not have to be feathered. They
will disappear in the in-between sanding of the painting.
For a neat job, use 2" masking tape ¼" outside
the tape that covers the seams all around.
This is not necessary if you plan to seal the whole hull outside
either with epoxy or plastic resin.
To prevent sagging ripples of the glue, remember that two thin
coats with a light sanding by hand in between, work better than one
thick layer.
Hull
Carpentry
Dagger
Board Case
1. Make up the dagger
board case. The trunk fore is l5" long. The lumber is anchored in the aft edge of the mast thwart as
is shown in the lower drawing of the set of plans on page 7.
Before the second panel closes up the case. Put in the open box.
Make sure the (half) case stands perfectly vertical on the
bottom. With a sharp pencil, mark the location for the bottom slot
and cut out the slot in the bottom.
Close the box temporarily with four screws on each side (total 16
screws).
2. Mark the slightly
curved bottom line on the sides of the case by sliding along it with a
pencil that is placed on top of a (scrap) piece of 1"x1".
Adjust the bottom edge parallel to this contour line. Only the corners need some corrective filing.
To prevent possible leaks, double-check for a perfect fit.
Middle
Thwart
1. Check the
measurements of the middle thwart flush with the top edge of the dagger
board case. Place this
thwart in the hull. The
trunk with both sides on, is anchored in this thwart.
Temporary hold the thwart in place with screws through the side
panels. Stagger the
location of the screws from their opposite side. Double-check that the thwart is perfectly parallel to the
bottom.
2.
Draw a pencil line underneath the thwart on the side panels.
Make the thwart supports and glue them against the side panels.
3.
After a “dry run” that the case and the middle bench fit
perfectly, open the box and seal the insides with at least two layers of
epoxy or plastic resin. Glue
all parts in place. After
the glue has dried remove the 16 temporary clamping screws from the
dagger board case, drop some glue in the holes, and replace these screws
with 1" - #8 stainless steel screws.
4.
Remove the hull spreader and the (temporarily) attached
guardrails.
Mast
Foot Blocks, Mast Hole
1.
Cut out these two blocks shown in the lower drawing on page 10.
2.
In one block, drill a hole slightly wider than the diameter of
the mast.
3.
Sand the bottom side of the lower block in shape with the
curvature of the bottom.
4.
Glue this block onto the bottom fore against the dagger board
case. Glue the block with
the hole on top of the solid block.
Drill the mast hole slightly wider than the mast diameter in the
mast thwart, vertical above the mast foot hole.
Keelson
Install
the keelson fore of the mast foot block, and aft of the dagger board
case. The keelson is made
up from three 8' - ⅝"x½" wide slats that
were cut from the first 2"x4" as described on the
middle of page 11. Place
one slat ⅝"-wide on each side along the dagger board
box. Fill up the slits
between the two slats fore and aft of the dagger board case with parts
of the third slat.
Deck
1. Seal the horizontal,
inside seams of the bow and transom board panels with the same 4"
tape that was used on the outside.
2.
Install the deck that is made up from three pieces of 11/16"x3½"
battens mentioned on page 11 at the bottom heading Second 2x4.
Turn
over the hull. Attach parts
of an 8" – 11/16"x½" fore and aft of the dagger
board slot.
Skeg
1.
Make a template from Bristol board of the bottom curvature of the
bottom aft of the dagger board slot unto the transom board edge.
2.
Use this template to install the skeg flush with the ransom board
edge aft as is shown on page 10.
3.
Attach the skeg with four stainless steel screws of different
lengths from the inside through the keelson and the bottom into
predrilled holes. This is
one of the parts that are easily damaged.
Do not use glue!
Transom
Bench
1.
Make the thwart from the rest of the 11/16"x3½" battens
that were used for the deck mentioned on the bottom of page 11.
2.
Install two supports that keep the front edge of the bench
horizontally 2" above the floor of the bottom.
Keep an 1½"-wide space between the thwart and the
transom. It gives more room
to sit on. It makes
cleaning the space under the bench easier.
3.
Attach the bench with a stainless steel screw onto the two
supports. Double-check that
the screws don’t stick out under the bottom!
Note
that the only times screws inside the hull are used in this
project are to strengthen the dagger board case, to attach the skeg to
the bottom, and to attach the bench aft to the supports.
In this last case that is necessary to get to the screw of the
skeg in case this part needs to be replaced.
Rudder
|