Maddog!'s
Marbles
by Alan "Maddog!" MacBride themadmac@mindspring.com
Loose thoughts rattle around my brain like marbles in a
shoebox. Occasionally a marble pops out of the box and I come up with something
useful. Here are couple called "Lofting" and "Minimizing Errors". |
A perception I've developed from reading the numerous posts to
rec.boats.building, is that amateur boatbuilders seem to run screaming or cower in a
corner when the word "lofting" is mentioned. Lofting is nothing more than
nautibabble for Layout. You wouldn't dream of putting up a shelf without measuring its
length and width and measuring how high up off the floor you'd want to install it, but,
you wouldn't think taking these measurements was either difficult to do or complicated. So
why scare yourself with "Lofting"? |
Over the many years that I've been building things,
ranging from precast concrete skyscrapers to gold jewelry, and oh yeah, shelves, layout
has become the most important element of any project. Without proper layout to start, all
sorts of problems surface later on as building progresses. Still, no reason to
panic; whatever you're building, it's still only "length", "width" and
"height". So much for that monster under the bed. |
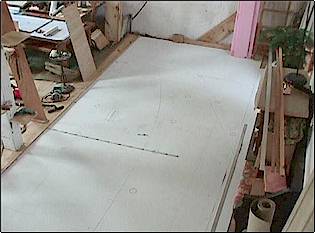
Lofting a 26' Junk
|
Typically, small boats and dinghies of the plywood panel
variety require measuring and marking a few points on the plywood, then bending a flexible
stick to the points to form the curved lines of the panels. The idea of using paper
templates is unnecessary, and measuring (scaling) from the drawing is preposterous. Paper
shrinks and expands. Blueprints are notorious for elongating the lines in the direction of
printing. That's why blueprints have numbers, dimensions. This notion is even more
ridiculous when dealing with bigger boats such as the 26' Penny I'm building. |
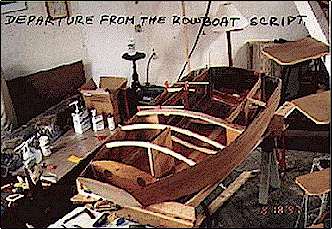
The D4
|
When I built my D4, I used the free plans from
Mertens-Gossens because they had dimensions. Later, after the hull was assembled, I bought
the plans from Jacques Mertens so I could compare the
two versions, and so he could take his girlfriend out to the movies. But, they
really weren't necessary, all the dimensions were on the free plans. |
Here's the second marble. "Measure twice, cut
once." makes a lot of sense. But time and again I've seen instructions that direct
the boatbuilder to lay out the pattern (for a panel), cut it, then use the first panel to
mark out the second panel and cut that one. Jeez! It was hard enough getting my
trusty Bosch saber saw to follow the lines the first time, now I was supposed to
accomplish that miracle again? Not likely! Granted, making a template to reproduce a lot
of identical pieces of something makes perfect sense. I'm a firm believer and practitioner
of making tools to get a job done. But for two pieces of something, it's just a PITA, and
introduces an unnecessary margin for error. |
So I came up with an alternative. "Measure
once, cut twice." My D4 was essentially two
whole sheets of plywood for the long hull panels and bits and pieces for the transoms and
other parts. The hull panels are mirror images of each other. Two bottom panels, and two
side panels. |
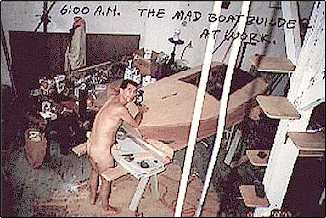
Maddog! playing with his dinghy
|
By laying the two sheets of plywood on my worktable... face to
face..., and screwing them together, I was able to layout (loft) the lines once, and cut
both bottom panels and both side panels at the same time. They were identical because they
were only measured once, like clones. Additionally, while they were still screwed
together, I was able to sand the edges where they needed, knowing that the two panels
would always be the same. |
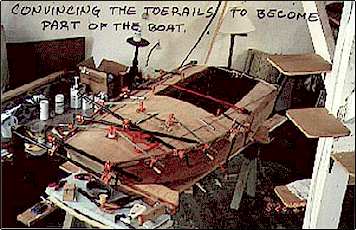
Installing the toerail
|
I'd love to lay claim to this concept, but the
truth is, I was passing through a clothing factory about fifteen years ago and saw them
cutting fifty layers of cloth at the same time with what looked like a very tall saber
saw. The impression this made on me became a marble that went into my shoebox. |

|